APPMA’s first Digital Lunchtime Series 'Investing in Resilience' panel discussion last Friday was facilitated by PKN's publisher, Lindy Hughson, who was joined by four industry leaders and experts in their respective fields to discuss the topic of manufacturing: adapting to the new normal.
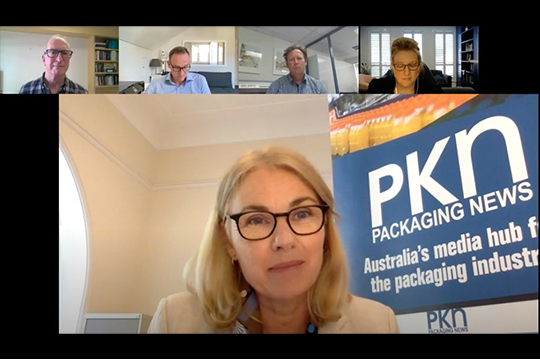
Brook Donnelly, CEO, Australian Packaging Covenant Organisation (APCO); Dr Jens Goennemann, managing director Advanced Manufacturing Growth Centre (AMGC); Tom Lunn, group general manager, marketing and innovation, Detmold Group; and Dr Peter Burn, head of influence and policy, Ai Group unpacked what the role of manufacturing will be in the post-pandemic recovery, and how a renewed focus on reshoring, supply chain security, and sustainable manufacturing could provide opportunities for industry growth.
Goennemann kicked off the session, by discussing his take on the state of manufacturing in Australia, and advising what we need to do strengthen our manufacturing base.
He identified that production and manufacturing are not synonymous.
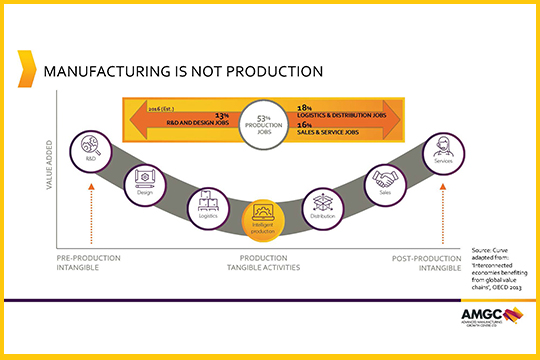
“Production is only one part of a manufacturing value chain and manufacturing consists of seven steps, so it is in our very best interest to understand the broadness of manufacturing and what it entails,” he said, pointing out that over 50 per cent of jobs are sitting outside production and these are the highest value, skilled and paying jobs.
Goennemann identified that another key gap was that 85 per cent of the 47,000 manufacturers in Australia employ less than 10 people. Clearly, we need more middle-sized companies to form the backbone of the industry, he said.
Responding to questions related to the factors necessary for Australia to become globally competitive, he pointed out that although Covid has been a key trigger to increase the focus on manufacturing, it was not enough.
He said that Australian manufacturers need to go from lucky to smart, and focus on not spreading themselves too thinly.
“We are too small to do everything,” he said, emphasising Australia’s recent truimph in producing Covid critical supplies within a short time frame.
“A consortium of Australian manufacturing companies was able to build 1700 invasive ventilators out of nothing in around five months – that’s not trivial,” he said.
Addressing the question related to workforce planning and skills retention, Peter Burn pointed out that new technologies often create workforce risk, along with opportunities.
He said that technological changes that create, rather than destroy, jobs can take quite a while to work their way through the economy.
“Where they can, businesses can benefit by being proactive, often in partnership with the relevant people, to address the risks, and to make the most of those opportunities so they can allow, and encourage staff to upskill and devote time to training,” he advised.
On the subject of an onshoring strategy, Burn was of the opinion that there were more fundamental forces determining the location and character of manufacturing, than the onshore government involvement.
“Manufacturing is subject to very powerful global forces such as globalisation, emerging economies, technological change, demographic pressures, and of course, environmental pressures,” he said. “These are likely to expose uncompetitive expansions based only on the hope of increased local demand without the sorts of things that will drive competitiveness, such as lifting investment, improving management, and workforce training.”
The conversation then turned to matters environmental, and the link between sustainability and business growth. Commenting on APCO’s experience of sustainability collaborations between government and industry, Brooke Donnelly cited positive examples and pointed to projects carried out with CSIRO on plastic packaging and the Ellen MacArthur Foundation’s Plastics Pact.
“We [also] see it with government, with the Recycling Modernisation Fund for nearly a billion dollars coming through,” she said, which when combined, is driving all kinds of activity in recycling in supply chain partnerships, some of which have never existed before, and such as the KitKat recycled wrappers project [which involved a large scale cross-industry collaboration].
Donnelly pointed out that a lot of these collaborations have been driven by the inception of the 2025 National Packaging Targets.
“[Also] there needs to be an understanding that we have a systems problem that we're trying to deal with here, rather than an organisational or even a sectoral issue, and there's different roles and responsibilities for everybody in that to resolve the problems that we have around packaging and its negative impact on the environment.”
Tom Lunn, whose company has seen first hand how a focus on sustainability can lead to business growth, discussed Detmold Group’s joint investment made with Woolworths on developing local capability for manufacturing paper shopping bags as an example of local investment in manufacturing off the back of a sustainability/ circular economy drive.
Discussing onshoring of manufacturing in general, he pointed out that since not everything could be locally manufactured, some materials would still need to be sourced offshore, and thus be subject to the vagaries of shipping challenges. But on the positive side, he said that brands and manufacturers are now thinking more about localising supply chains.
This, he said, presents a complex situation as there is still a price premium on localised goods and services.
On the subject of sustainability, he predicts that there could be pressure from the brand owners' side to buy more recycled content.
“So, there will be new businesses emerging and some of the fast movers will gain an advantage through that,” he said, pointing out that a lot more collaboration and partnerships could emerge within the industry.
“I think the plastics industry will really come together, and there'll be a lot more recycled-content plastics and other materials available that have been hard to buy over the years.”
The panel concluded that there is significant promise for Australian manufacturing. While there are pressures to face and challenges to overcome, overall there is opportunity to harness innovation and scale up manufacturing for export growth, and through a focus on sustainability and reducing supply chain risk, the local packaging and processing industry can prosper.
Click here to register for the next Digital Lunchtime Series session on cyber security on Thursday 23 September.