Garvey has leveraged Rockwell Automation's Emulate3D software and Australian industrial tech consultancy Glenvern Group's expertise to showcase its high-performance accumulation systems.
Garvey, a specialist in conveyor and accumulation systems and part of the Columbus McKinnon group, has long been recognised for helping manufacturers solve production line challenges. Its systems are designed to reduce downtime and increase throughput by introducing buffer zones between key manufacturing steps – particularly valuable in bottling, filling, labelling, or packaging operations.
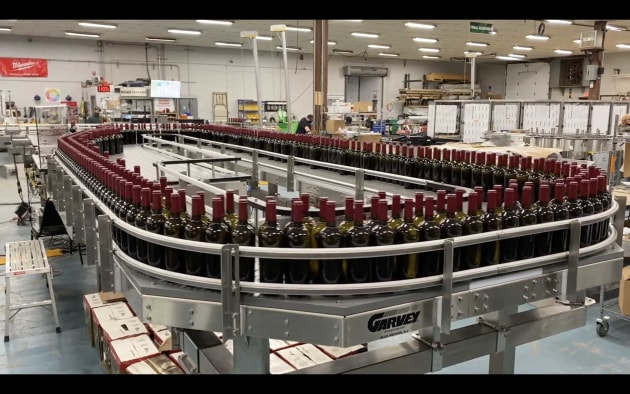
Serving an extensive customer base – from small breweries to the world’s biggest food, beverage, pharmaceutical, and household product brands – Garvey wanted a better way to showcase the impact of its accumulation tables. These tables come in various configurations – circular, rectangular, or custom – and play a crucial role in maintaining the steady flow of product, even when part of a line experiences a pause or delay.
“We’ve always been confident in our technology,” said Bill Reese, senior director of engineering at Garvey. “But we needed a more engaging, data-rich way to tell that story to potential customers.”
Strategic partnership
That opportunity emerged through the company’s relationship with parent company Columbus McKinnon, which had previously worked with Australian industrial tech consultancy Glenvern Group. Glenvern is a certified Rockwell Automation Partner, with deep expertise in implementing Rockwell’s digital visualisation software, Emulate3D.
Having seen Glenvern’s successful Emulate3D deployment for another Columbus McKinnon company, Dorner – also a conveyor specialist – Garvey recognised the potential for similar gains.
“It was clear that Glenvern understood our world,” Reese said. “They had already customised Emulate3D to help Dorner visualise system layouts and performance. We knew it could be a strong tool for us too – especially when targeting global beverage clients.”
Real-time impact
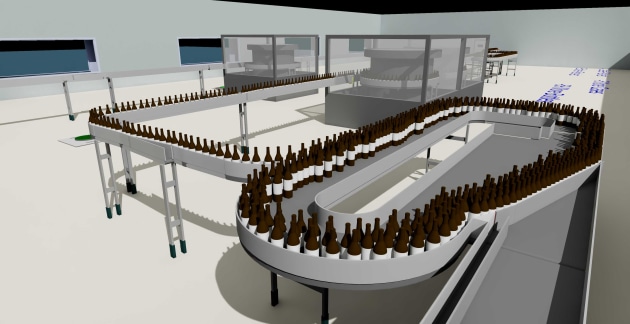
Garvey’s main goal was to visually demonstrate the production benefits of its accumulation systems – showing how they reduce bottlenecks, allow upstream processes to continue during downstream slowdowns, and enable better use of maintenance windows.
However, the company didn’t just want static visuals. It needed real-time interactivity.
“The challenge was finding a simulation solution that was intuitive, ran on standard hardware, and could be manipulated live in meetings,” Reese explained. “We didn’t have anything in-house that met that need – but Emulate3D ticked every box.”
Emulate3D allows users to make changes on the fly – altering variables during presentations to reflect different product types, line speeds, or stoppage scenarios.
“Being able to simulate multiple real-world conditions in real time has been a game changer,” said Reese. “It brings the impact of our solutions to life in a way that spreadsheets and PowerPoint slides just can’t.”
Powerful software
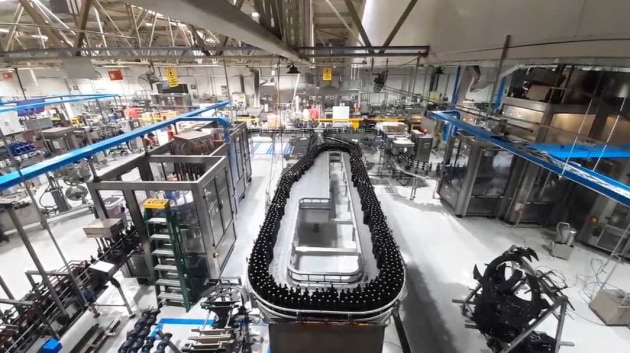
Emulate3D, developed by Rockwell Automation, provides a dynamic 3D modelling environment for creating high-fidelity simulations of discrete manufacturing and material handling systems. It combines visualisation with simulation, virtual commissioning, and digital twin capabilities – allowing teams to test and refine their designs virtually before physical deployment.
Glenvern Group has specialised in Emulate3D for over two decades and has worked with Rockwell and manufacturing clients globally to deliver bespoke simulation environments. For the Garvey project, the team created a fully visualised bottling line that showed in detail how accumulation tables improve flow, prevent stoppages, and maintain consistent throughput.
“Without accumulation, a single halt in production brings the entire line to a standstill,” said Alec Poulton, director at Glenvern Group. “With the right accumulation system in place, you create buffer capacity – meaning one part of the line can continue operating while another is paused.”
Glenvern’s visualisation also highlighted how strategic use of accumulation systems can support preventative maintenance, allowing scheduled interventions with minimal impact on output.
Measurable benefits
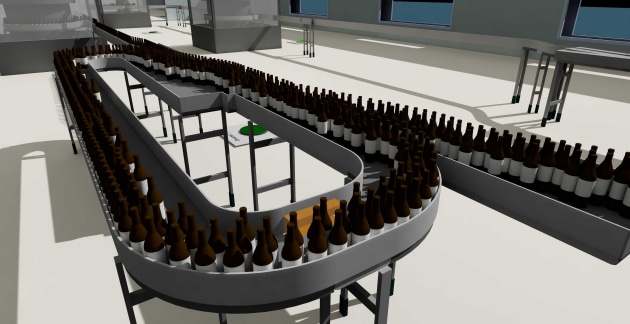
Garvey’s sales team now uses Emulate3D simulations to demonstrate its system benefits in meetings, trade shows, and training sessions. These demonstrations combine screen recordings and live interactions to present both visuals and performance metrics – such as bottles packed per minute, total output, and the impact of stoppage scenarios.
“We can run a ‘before and after’ comparison for customers,” said Reese. “The system calculates and displays key production data – and that makes a powerful case for investing in accumulation.”
This approach has not only helped to accelerate Garvey’s sales cycle but has also enhanced internal training, ensuring teams better understand system behaviour and benefits.
Widespread adoption
The success of the project has led to wider adoption of Emulate3D across the Columbus McKinnon group. Both Garvey and Dorner now actively use the platform, and Glenvern continues to provide training, project support, and technical services.
“Glenvern has been a fantastic partner,” Reese said. “Their team was responsive, technically sharp, and easy to work with. They helped us get the most out of the software and really understood what we were trying to achieve.”
Glenvern Group’s work with Columbus McKinnon spans multiple sites across the Asia–Pacific and North America – delivering visualisation solutions that help simplify complex production concepts and support customer engagement.
Sales Advantage
With its new interactive simulation capabilities, Garvey is in a stronger position to attract and convert customers across global markets.
“We’ve always known our systems deliver results,” Reese concluded. “Now we can show those results in a compelling, professional, and interactive way – and that’s making a real difference to how we engage with customers.”