Fibre King delivered a full turnkey conveying, robotic palletising and pallet handling solution for Australian agribusiness DAHall & Co. PKN takes a closer look at the project.
Queensland-based DA Hall is in the business of egg production, so as an important requirement, Fibre King’s solution had to be gentle enough to handle the delicate, yet weighty product, as well as meet throughput demand at the egg producer’s Millmerran facility.
Originally, the plans included a new factory build with imported equipment, however, with the onset of Covid, the company needed to look for a domestic solution.
“Fibre King managed to provide a solution that was not only tailor made for our site, but brought us along on the journey using 3D modelling for us to understand what we were going to get before we moved forward with them,” said Don Trefz, general manager of DA Hall.
“One of the biggest challenges when finding a suitable solution was to fit two [egg grading] machines into one build, and convey the eggs into one point for palletising; but not only that, the solution had to pack different product systems – caged, organic, free range, pasture raised, open range – and into export SKUs, local SKUs, egg sizes and more.
“Fibre King had to come up with a system that could pack those eggs, which we put into 131 different types of cartons, and still go onto one standard Chep pallet.
“No one can underestimate the amount of work that goes on in the background, that they had to put together to provide the solution to us within the quotation period, let alone to actually turn it into practice,” Trefz said.
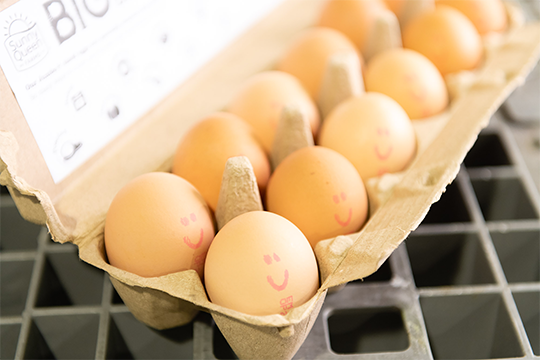
Phase One
The first phase was to deliver the conveyors to merge all the product from the existing grader from MOBA with the new grader that was to be delivered.
It involved installing a high-level conveyor, along with spiral elevators and lowerators, as well as merging and gapping equipment to distribute the cartons from those two graders to four new, fixed size taping machines, and one existing random taping unit.
From there, it was merged again onto a single line for distribution through to manual palletising.
At the end of phase one, which allowed a very small window for installation, Fibre King managed to get the plant up and running in under 24 hours, and enabled DA Hall to achieve higher efficiencies on the taping side of their business, while still being able to manually palletise.
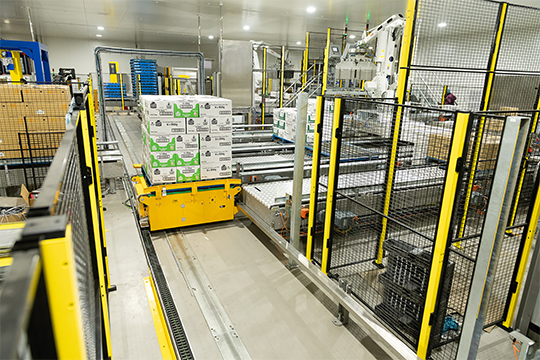
Phase Two
The second phase of the project was to install the robotic palletising system and the distribution conveyors to deliver to that palletising system.
Within another small window of approximately 15 hours, Fibre King installed a DARB conveyor from Intralox, which was to act as a bypass to the initial phase until the system went live.
Over the course of three weeks, Fibre King installed the three robot cells, pallet handling system, and the shuttle outfeed system to feed the Fromm stretch wrapper.
From there, the robot cells were commissioned one at a time, slowly taking the load off the manual palletising system, which was in place while the installation was underway.
Once the robotic palletising system was up and running in full, the manual palletising was only utilised for overflow products in excess of the 12 SKUs that the robots were handling.
Project Management
Fibre King coordinated with a number of OEM suppliers – Intralox (conveyor supplier and belt manufacturer); AmbaFlex (supplied spiral conveying), Insignia (supplied labelling and coding on the project), ABB (manufactured the robots), Track Automation (supplied both the robot grippers and the pallet shuttle system); and Fromm (supplied the stretch wrapping equipment and taping machines).
“The equipment that Fibre King has put in has significantly improved our production – having two grading systems within the same building meant we would be packing at 306,000 eggs per hour,” explained Trefz.
“One of the main benefits of the new system is improved work safety. Each carton of eggs weigh up to 10kg each, and on a typical day, staff were packing between 15,000-20,000 cartons.
“The manual handling side of the job was one of the biggest challenges for our workers, and this equipment has negated that. Now we are able to get the product out of the door with no manual handling, and no work injuries.
“Prior to having this equipment, we used to run 365 days a year and we managed to bring that down to a five day a week operation, while increasing production targets. You cannot underestimate what that has done for the worker morale and the long-term functioning of this business. It has really turned it around.”
According to Greg Constantinidis, innovation manager at Fibre King, the company derived significant job satisfaction out of the delivery of this turnkey project for DA Hall.
“To see their production figures increasing day in and day out has been really positive,” he said.
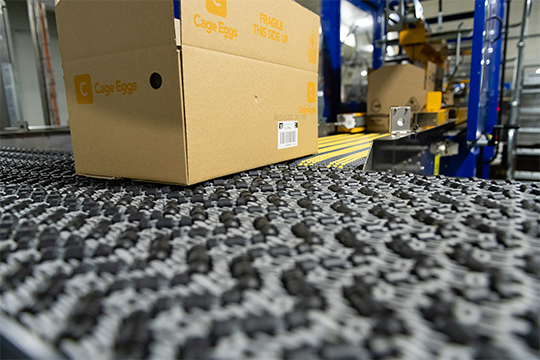
This article was published in the May-June 2022 print issue of PKN Packaging News, p20.