As part of Coca-Cola EuroPacific’s expansion of its Moorabbin plant, the company’s Neverfail spring water bottling facility was relocated to a brownfield site in Heatherton, Victoria. Engineering company Process Partners played a pivotal role in the project.
Plant relocation presents challenges at the best of times. In 2021, when the Neverfail relocation project kicked off, the Covid environment added layers of complexity around the construction with slowdowns, lockdowns and an extra level of care required to keep everyone safe and up to date with government regulations.
For independent food and beverage engineering company Process Partners, engaged initially to design a new spring water plant for the site and then commissioned to install the turnkey processing and packaging line, flexibility was the name of the game.
Coca-Cola EuroPacific (CCEP) project manager – Neverfail Relocation, Judi Brown says that having Process Partners handle the process end to end provided major benefits in design continuity and contractor management.
“Uncertainty around the government Covid restrictions meant that works needed to be rescheduled. Process Partners were flexible and worked hard to achieve the best outcome for Neverfail,” she says. “With good communications throughout the project and the ability to work well with other contractors on-site, their part in the project was delivered very successfully.”
It’s a point of pride for Process Partners – which counts among its customer base multinationals like Lion, Bega, Asahi and Mondelez – that the CCEP project was delivered in January this year on time and within budget, with the new site now fully operational filling locally sourced spring water into a range of container sizes.
Describing the scope of the project, Craig Gilbert, senior packaging engineer at Process Partners tells PKN, “The proposed site was a former warehouse, and as such, was not prepared for a manufacturing space.
“Further, a number of services were shared between Moorabbin and Neverfail. These services now had to be sized and designed, including systems for the air, power distribution and spring water, CIP, steam, compressed ethernet & control.”
The process implemented involved accepting delivery of spring water from the tankers and bottling this on the Neverfail line at a rate of 1050 bottles per hour in 15-litre returnable bulk water containers.
On average, the spring water delivery volume is 100,000 litres per day. Included in the implementation was ensuring the supply for CIP of the production line and for the washer.
Describing the challenges faced on the process and services implementation, Gilbert says the longest lead time item was the tanks, and it became challenging when Process Partners’ usual suppliers were both unable to meet delivery dates.
“After an extensive search of Australia, New Zealand, China and Vietnam we found BTM (Brisbane Tank Manufacturing) who could deliver the equipment within the required timeframe.”
Covid too presented obstacles, with an initial delay during construction when the primary contractor could only have limited numbers of personnel on site. This delayed Process Partners’ starting date by six weeks, putting pressure on the timeline for installation and commissioning. Nevertheless, commissioning started close to Christmas, and completed by mid-January.
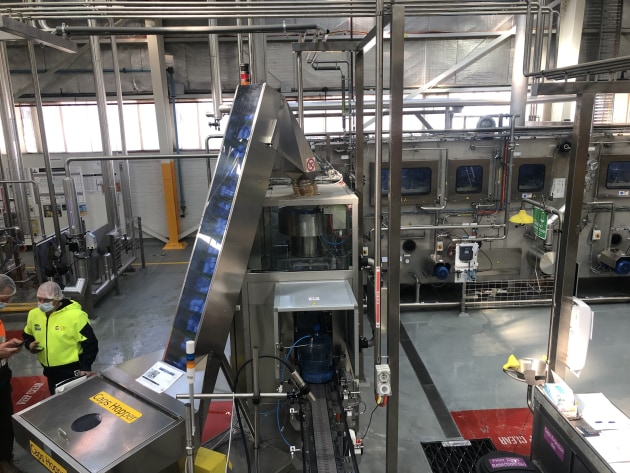
PACKAGING RELOCATION
For the packaging line relocation, the project scope included the mechanical and electrical disconnection, disassembly, removal, packing and transport of equipment and services currently installed and operational at the Moorabbin site, followed by the assembly and reinstallation of the same equipment to the site at Heatherton.
Packaging equipment relocated included:
- The washer/ filler/ capper, capable of washing and filling up to 20 bottles per minute;
- Empty bottle inspection and conveying system including decapping, vapour sniffer/leak detection and light inspection units on the infeed of the washer and a date coder at the outfeed of the filler/capper; and
- Stillage unloading and loading robotic system that automatically unloads 16 containers simultaneously ready for washing then once filled and capped, is automatically reloaded into the stillage.
Services connections were installed for product water, potable water, hot water, compressed air, and steam/ condensate. Additionally, there were numerous production related items including operator work benches, including sinks and walkovers.
“For this line, there was also a very short window to execute the relocation, from 28 December to the 13 January,” Gilbert says, noting that once again, Covid hurdles had to be jumped. “The disconnection team had to be replaced with a new team for the reconnection process. Essential crew were absent due to contacting Covid – at one point 13 welders were absent at the same time.”
Gilbert says that despite the challenges, the team pulled out all the stops to ensure installation proceeded and met the project timeline. Today, the Neverfail line is up and running at Heatherton, bottling spring water for nationwide distribution.
This article was first published in the March-April 2022 print issue of PKN Packaging News, p32.