Schulz Organic Dairy recently reached out to Rhima, as it had grown exponentially and was in need of a larger bottle washer. Rhima conducted R&D and created a bottle washer conveyor machine in line with the company's needs.

Schulz Organic Dairy, headed by Simon Schulz, first started providing milk in returnable, refillable glass bottles at farmers markets in 2017 but quickly sold out due to popular demand. He then launched a successful crowd-funding campaign to install a bespoke washing line at the farm to get more bottles into the cycle. The crowdfunding campaign was introduced in 2018 to fund the equipment needed to release 3000 glass bottles a week to their retailers which raised $106,100. He overshot the funding goal enabling the company to deliver 3500 bottles per week to retailers and farmers markets in their first year, eliminating 4.6 tonnes of plastic from the recycling system.
Rhima had initially proposed and installed a custom-built washer and sanitiser to clean his bottles at the rate of 400 bottles per hour, but since the growth of consumers buying the returnable milk bottles require Schulz to expand its business, this was no longer enough. As part of this extension, in 2023, an in-line continuous bottle washer, with infeed and outfeed conveyors, at a capacity of up to 6000 bottles per hour was required to cope with the current demand. This bottle washer, designed and built in Australia by the Rhima team, will be integrated into a fully automated bottle filling line.
“We already do so much for the sustainability of the farm and the environment here on site but the one thing we weren't tackling was the sustainability on the waste and packaging,” Simon Schulz said.
“Providing milk in returnable glass to retailers is a logistical beast of a process, and an expensive one to put in place. We needed help acquiring equipment and durable bottles designed to eliminate the need for labels.”
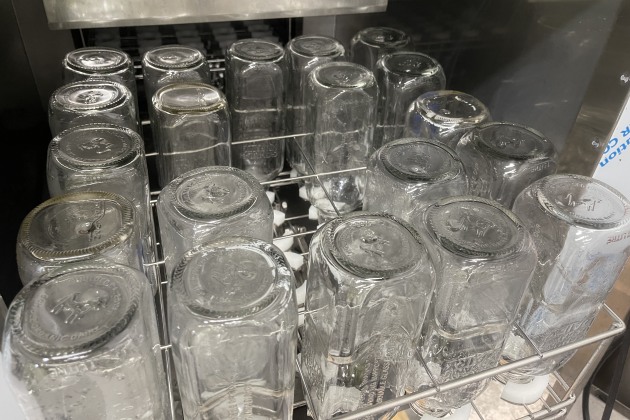
Schulz found the washer improves hygiene and cleanliness, as well as improved efficiency. If the glass milk bottles are not cleaned and sanitised properly and milk residue remains, this creates a food safety hazard, and the dirty bottles have to be thrown out due to their contamination risk.
The Design
Rhima says the bottle washer has been designed with a series of injector wash manifolds that allows each bottle to have its own specially designed spray nozzle. The Rhima design team started with one of its standard industrial washers and modified both the wash and rinse system as well as the programming and racking to achieve a design that met Schultz’s criteria. In particular, the special racking design, injection system, control system, and component selection required a lot of R&D, the design team said, explaining that this is to ensure that the bottles are 100 per cent clean while using minimal water and energy. The washer allows the reusable glass bottles to be available on the market. Without the ability to wash and reuse them hygienically this sustainable venture wouldn't be possible.
During the design and build process, the design team said it ensured suitable temperature controllers with temperature probes were selected to ensure best wash result at the required temperature outlined in HACCP guidelines. The unique design of the water injection system ensured all the inner and outer area of the bottles receive appropriate impact from water to remove milk residues.
This particular product/solution is new to the Australian market and doesn’t exist anywhere else in the world, according to Rhima. Since the first bottle washer was designed and produced by the Rhima team for Schulz, we have had a lot of interest in cost effective high throughput bottle washers. As a result of this, Rhima’s product development team has worked on a bespoke bottle washer and its capacity can be reached up to 5,000 bottles per hour depending on the application.
Rhima says its team is very solutions focused: “If a customer comes to us with a dilemma, we will do our best to come up with a cost effective, sustainable, circular economy solution”.
Industrial bottle washers exist, but most are developed for very large production runs in fully automated environments with high operation and maintenance costs. Smaller bottle washer/sanitisers are available too, but they are mainly aimed at the laboratory market with low capacities and long cycle times. The brief was to design and build a washer/sanitiser that would wash and sanitise to a HACCP program acceptable level, ease of use, a suitable and viable capacity while at the same time minimising energy and water consumption. The machine had to be commercially viable for it to be customisable and for use in different similar re-useable environments.
This solution would be suitable for wineries, refillable-returnable bottle companies, dairy farming industries and similar industries moving to the circular economy requirements and needing to wash reusable bottles. Rhima says it can easily reduce/increase the capacity depending on the requirements.
Sustainability
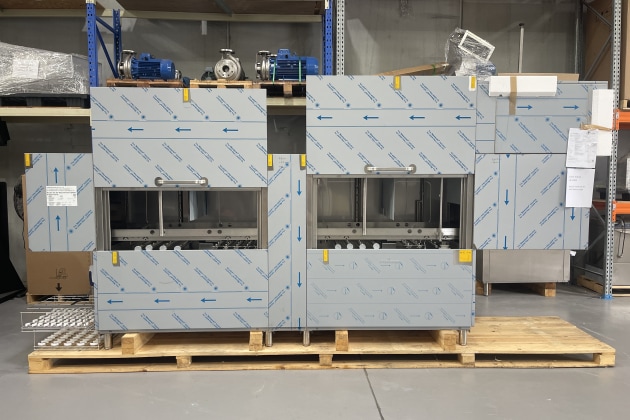
The reduction of plastic has significantly reduced the manufacture, processing, transportation and product use of plastic bottles. The old packaging had more of an effect on transport related CO2 emissions as the bottles were thrown in the recycling bin, picked up by a garbage truck, delivered to a depot, put in a container and shipped to China to be recycled. Schulz therefore gives customers the option of the refillable glass bottles, or plastic bottles in 1L and 2L sizes.
“We now deliver around 5000 reusable glass bottles of organic milk weekly, to around 100 retailers Victoria-wide, with a return rate of 95 per cent of bottles refilled and reissued. The initiative has averted 20,136kg of plastic bottles from landfill, as of October 2023 – incredible,” Schulz concluded.