With its L 310 full wrap labeller, Multivac is redefining the packaging of fresh eggs in boxes or plastic trays, promising to deliver highly attractive packs that also close with a secure seal.
The typical packs of four, six or 10 eggs are made of a recycled, paper-fibre-based material or transparent plastic. Branding and marking the packs is by means of pre-printing of the box, or alternatively, with either a cardboard sleeve or a pre-printed adhesive label on the top of the pack.
The L 310, which has patented, servo-driven press-on brushes, makes automated C labelling and D labelling, as well as traditional top labelling, of packs possible at an output of up to 120 packs per minute.
The maximum label width is up to 500mm, and it is possible to run packs with a base width of up to 250mm and a height of 140mm.
The labeller can be equipped with a zero-downtime function for even more efficiency and process reliability, as well as with an integrated printer and label/print monitoring at even the highest throughput.
If the L 310 is used for complete wraparound labelling, the full wrap label automatically seals the egg box closed. For retailers and consumers, this means that the products can’t be exchanged or contaminated with viruses and bacteria, or that the packs can’t be used to hide stolen products.
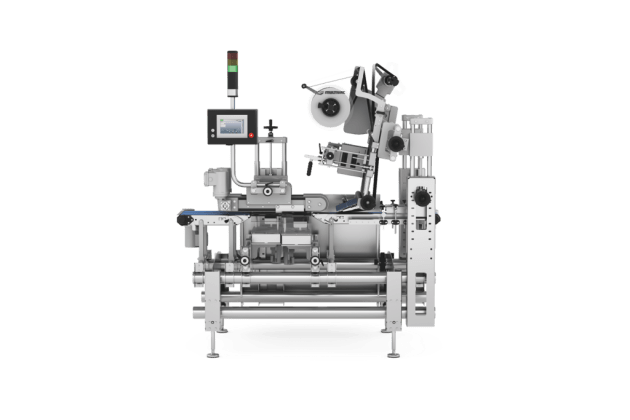
This makes the solution an ideal choice for aseptic or pasteurised eggs for the catering trade, hospitals and bakeries, or for infants and pregnant women. Packs like these have to be sealed in order to guarantee the highest level of safety, sterility and quality.
“In regards to pack appeal at the point of sale and the usable area for product promotion, this new concept for egg packaging surpasses the conventional top labelling or pre-printing of the box by far,” says Multivac.
“It even offers the benefit that, depending on the label material selected, it can be more cost-effective and above all, lighter than a sleeve. In addition to this, the full wrap label can be printed on different sides of the pack with variable data, such as barcodes, and it can also be applied automatically to the pack.
“A significantly higher-value look can be achieved for the pack, even with the most cost-effective material."
Another benefit of full wrap labelling is its high level of flexibility, since label shape, material type and printing can be individually tailored to the pack.
It is possible to run either film labels made of PP or PET, or alternatively more sustainable materials made from paper or renewable sources.
A perforation feature can be integrated into the label if required, so that the consumer can open the label easily. It is also possible to have printing on the back of the label for additional consumer information.
Label and packaging material can be matched to each other, so that the constituent parts of the pack can be separated to meet the recycling requirements.
Also, in the event of layout changes or faults in the pre-printed egg boxes, the complete stock of boxes must be destroyed, whereas with full wrap labelling it is only the pre-printed labels that have to be replaced.