One of the most progressive examples of packaging innovation in the Australia New Zealand region has been the design of the multiple award-winning Woolpack suite of insulated solutions, an alternative to polystyrene packaging for cold chain distribution. Lindy Hughson takes a closer look at the latest developments from the company behind the innovation, Planet Protector Packaging.
The environmental challenge presented by expanded polystyrene (EPS), a material commonly used in cold chain packaging, has been on the radar of Planet Protector Packaging (PPP) since the company’s inception in 2016. In its short existence, the company has been the recipient of a series of funding grants and numerous national and international awards for its packaging innovation that combats the hazards of EPS. Founder and managing director Joanne Howarth, a passionate protagonist for her cause – eradicating EPS from the chilled distribution supply chain – has also gained global recognition for her ingenuity and leadership.
EPS is a fossil-fuel based plastic that has been identified for phase out of use due to its difficulty to recycle and widely documented devastating impacts on the environment, oceans and marine life.
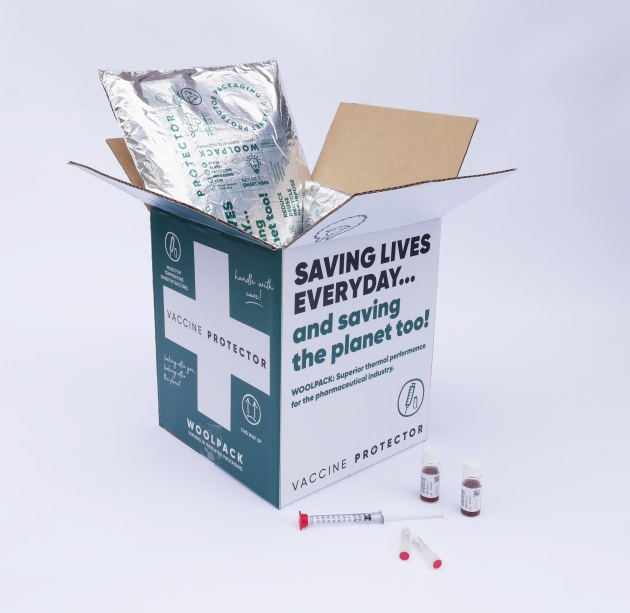
“It is estimated that EPS takes more than 500 years to breakdown,” Howarth says and goes on to cite the Australian Packaging Covenant Organisation (APCO) 2018/19 FY report, Australian Packaging Consumption and Recycling Data 2018-19, which estimates that of the 16,000 tonnes of EPS packaging put onto the Australian market, 4000 (25 per cent) was recycled. Further, she says, the report finds no evidence that any EPS in Australia, in that year, was made from pre – or post-consumer stocks, only virgin sources.
“Overall, eight million metric tonnes of plastic end up in the ocean annually, with a shocking 42 per cent emanating from the packaging sector,” says Howarth, who is determined to drive the change to an alternative solution.
To this end, the company is expanding its footprint across Australia and into Asia, has embarked on a capital raise to fund its expansion, has inked a distribution partnership for Woolpack with ASX-listed Pro-Pac Packaging (PPG), and is continuing to fuel its Woolpack innovation pipeline for food, beverage and pharmaceutical products.
TIMELY DEVELOPMENT
PPP’s latest commercialised development, the Vaccine Protector Solution, is a finalist in the ANZ 2021 Packaging Innovation & Design Awards in the Sustianable Packaging Design and Health, Beauty & Wellness Packaging Design categories.
[Ed's note: On 25 May, the PIDA winners were announced, and Vaccine Protector won the gold award in the Health Beauty & Wellness Packaging Design of the Year category.]
As its name implies, the pack has been designed for the temperature-controlled distribution of frozen vaccines and medicines. It could not have come at a better time.
According to Bernadette Scarfe, PPP head of pharmaceuticals, “With huge disruptions to the global supply chain, the COVID-19 pandemic has magnified the immense challenges surrounding temperature-sensitive pharmaceutical distribution.”
“With reports emerging of vaccine wastage across the world, there has been an increased focus on alternate, superior distribution methods,” she adds.
“The COVID-19 pandemic has reset the space for a sustainable global system and a ‘green’ recovery. Never has there been a better time for sustainable packaging and insulation to take the front seat in the pharmaceutical space,” Scarfe tells PKN.
“Wool is one of nature’s very best insulators, a biodegradable and renewable fibre that is at the centre of the Woolpack Vaccine Protector technology.
“Scientifically proven for its environmental and performance credentials, wool is a proven performer even under Australia’s harsh conditions, keeping frozen vaccines safe duringtransit.”
SAFE & SUSTAINABLE STRUCTURE
PPP’s Vaccine Protector is made up of three critical material components: the wool knop liner, the metallised polyethylene radiant barrier film, and the corrugated carton.
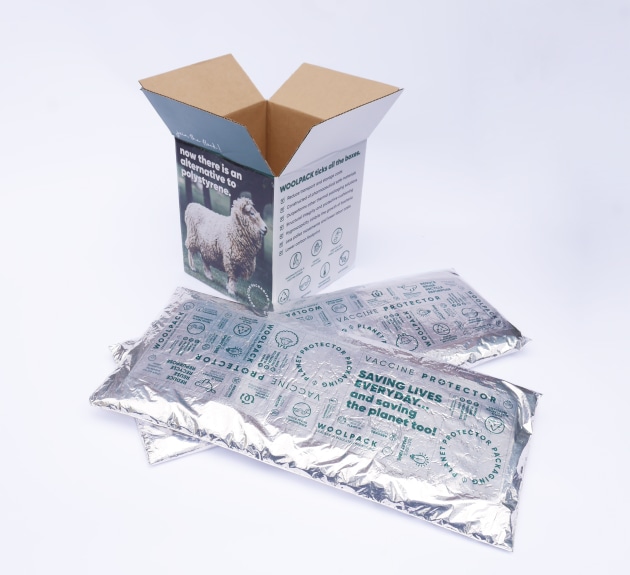
The wool knop liner is comprised of cylindrical pea-sized balls of wool that demonstrate extraordinary insulating properties, according to PPP. The wool knops’ large volume to mass ratio affords them a high thermal resistance with insulating air pockets created between the webbed knops.
“The wool that makes up Vaccine Protector’s insulation component, is nature’s own smart fibre, outperforming any synthetically made fibre on the market,” says Joanne Howarth, talking with the authority borne out of total immersion in the Woolpack product development for over four years.
“Nature intended that wool would keep sheep warm in winter and cool in summer; we have simply utilised the principles of biomimicry and leveraged the thermal properties of wool to create an alternative to harmful expanded polystyrene products,” Howarth says.
The wool liner, she explains, is made from coarse, “non-textile grade” waste wool. This is the wool with the highest crimp factor and medullation, characteristics which lend themselves to greater insulation properties.
When transporting frozen vaccines, which must maintain strict temperature profiles and stability, the hygroscopic wool fibres absorb moisture from the air, creating a thermal barrier and minimising condensation from within the payload.
“Beyond thermal credentials, our wool knops provide a protective cushion to safeguard products,” Howarth adds.
The wool liner is made of 100 per cent natural wool, a fully renewable resource that is biodegradable, sustainable, natural and compostable. PPP uses ‘waste’ wool that is too coarse to produce comfortable clothing and will not absorb dyes and so would usually be consigned to landfill – a wasted economic opportunity.
The wool is scoured, naturally washed with soap and hot water (no toxic additives) and processed using a propriety method that provides a sterile, consistent ‘knop’ product with optional insulation properties.
The liner is then cut to size for the customer’s desired corrugated carton size requirements.
The second component, the metallised polyethylene film, integrates a radiant barrier within the Vaccine Protector, and distinguishes this product from PPP’s standard pharmaceutical range.
“This combination of both radiant and convective heat barrier is key to the innovation PPP’s Vaccine Protector brings to the transportation of frozen vaccines,” Scarfe explains, noting that this material has been chosen for its wide recyclability across Australia, through the REDcycle program for soft plastics.
Bringing the Vaccine Protector’s sustainability credentials full circle, the third component, the corrugated carton, is made from 50 per cent recycled fibreboard content, reducing the need for virgin material. The carton can be recycled via commercial kerbside recycling infrastructure.
WHAT’S NEXT FOR PPP
Vaccine Protector joins a range of innovation already commercialised by PPP, much of it for the food export market. As this article goes to press, PPP is headed to Tasmania, where along with customer TasFoods it will showcase Woolpack at the Agfest show in Hobart in early May.
As a next step in the company’s expansion plans, it is soon to set up shop in Tasmania, supported by a Boosting Female Founders Grant.
“We have just secured premises for a warehouse facility adjacent to the Launceston Airport, from which it is the intention to service the entire Tasmanian market,” Howarth tells PKN.
PPP will be working with the Brand Tasmania organisation, which is keen to leverage the opportunities around sustainable packaging as a way of differentiating the premium Tasmanian product.
Asked where to next for the company after Tasmania, Howarth says, “We’re heading south to wine country, the Barossa Valley”.
The plan is to set up close to winemakers as the company prepares to debut its new Wine Protector range in late 2021.
“This range is designed to provide tailored solutions for both domestic and export shipping, anywhere from small gifting ranges to large pallet transportation,” she explains.
Intent on expanding its horizons beyond Australian borders, PPP is also looking at a launch in Asia, probably in 2022.
“We’re currently checking market entry feasibility for Indonesia and Singapore, where we’d be looking for distribution partners; and we’re in discussions with a distribution partner in Korea,” Howarth says.
To fund these ambitious plans, the company is in the process of a capital raise for at least $6 million. It has opened a data room to a range of private, institutional and impact investors spanning the globe.
“While pen has not hit paper just quite yet, we are confident we have found a major partner with whom we can rapidly expand and increase our impact,” Howarth says.
It is Howarth’s unwavering commitment, and the passionate desire on the part of her team to make a positive impact when it comes to protecting the planet from the ravages of polystyrene, that has brought the company thus far on its journey and will no doubt fuel its growth as its footprint expands.
This article was first published in the May-June 2021 print issue of PKN Packaging News, p36.