Coca-Cola Europacific Partners has pressed go on the most advanced canning line in its network in the Australasian region, a project that was two years in the making and delivered in partnership with key technology suppliers including KHS, GPI and Matthews Australasia.
The new line, housed at CCEP’s production site in Moorabbin, will allow the beverage manufacturer to scale its local can production significantly, and increase the flexibility around the packaging configurations it delivers to customers across Victoria, Tasmania and South Australia.
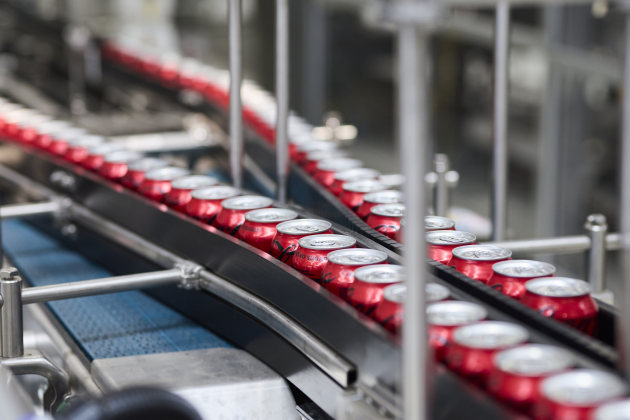
PKN spoke to CCEP project lead David Holden, who said he is excited to see this cutting-edge line up and running, after a two-year timeline, and said delivering this project required “tremendous teamwork and collaboration” with partners to overcome the constraints placed on them during Covid.
“The new Moorabbin line is a significant capability shift to provide a diverse range of products for customers across Victoria and interstate. It introduces leading technology available on the market, capable of packing over 37 different varieties of product, at a highly efficient rate over 24/7 operations to meet the demands of our customers,” Holden said.
Automating for flexibility
CCEP fills and pack cans into a range of pack formations, multipacks, cluster packs and slabs, across 37 different beverage varieties, including Coca-Cola No Sugar, Sprite, Mount Franklin Lightly Sparkling, Canadian Club & Dry, Monster, and Mother Energy.
Beverage packaging specialist KHS was tasked with leading the line integration project in collaboration with the CCEP team. It also supplied the majority of the equipment on the line.

KHS Australia managing director Jens Kautzky told PKN, “The KHS team handled the full execution and commissioning of the line using only local resources for project management and service support.”
Kautzky added: “This is the most automated canning line of its kind in the southern hemisphere in terms of its ability for fast changeover. With other lines like this, manual adjustment is required when changing between packaging formats, on this line it is fully automated.”
Processing capacity of the KHS Innofill Can DVD line is 1200 cans per minute for 500ml, 1500 cans per minute for 375ml and 1700 cans per minute for slimline 250ml cans. The line can handle a variety of formats and sizes, from mini 250ml cans to 375ml and 500ml packs. Cans are supplied by Orora Beverage.
Commenting on the sustainability attributes of the filling line, Kautzky described it as “truly world class”, not only because of its speed, but because it can fill at ambient temperature while still achieving the high speeds typically associated with cooler filling temperatures, saving energy and CO2 in the process, in line with efficient mixing system supplied by KHS.
Holden said that while the line is operational, validations are still underway with various brand partners. Once it is fully operational, he confirmed that it will have the capacity to provide an additional 11 million cases of product to the Victorian market.
Flexibility and agility is delivered not only through the KHS canning line but also the automated secondary packing systems supplied by Graphic Packaging International (GPI), including a QuickFlex TwinStack G3 machines for fully enclosed multipacks of between six and 30 cans and a Marksman for straight or gusset wrap around multipacks of four and six.
The KHS Innopack Kisters packer enables loose or prepacked product to be processed via an energy-saving shrink tunnel using tray and shrink or shrink only, rounding out the new lines ability to cater for all of CCEP’s current packing offerings.
KHS also supplied a high-speed, low-level robotic palletising system, integrating Kuka robots.
End-to-end traceability
Holden said another key supplier integrally involved in the project was Matthews Australasia, who played a significant role in delivering level of technology and systems capability to meet the high speed and flexibility requirements.

PKN spoke to Matthews regional sales manager Matt Nichol who confirmed Matthews provided a completely integrated solution using iDSnet to integrate to CCEP’s ERP (SAP) system using work orders to start a run and integrate all coding, labelling and barcode scanning technology across all formats of the production line – primary, secondary and palletising.
“iDSnet simplifies the start of run process catering to the multiple packaging formats CCEP is running on the high-speed production line,” Nichol said.
For primary coding, Matthews supplied a 100w Fiber laser (the SolarJet FL10) capable of printing at speeds of 2000 cans per minute. For secondary coding, Matthews installed several Linx 8900 series inkjet coders printing traceability codes onto the shipping packs. Matthews also integrated barcode scanners inside these packaging machines to ensure the correct packaging material is loaded, eliminating any potential packaging errors.
A range of CCEP pack formations require TUN labels to be applied for scanning through the supply chain. Nichol told PKN, “Matthews has installed TUN labellers capable of applying labels at 160 cases per minute. Our solution consisted of four labellers providing CCEP with a zero-downtime solution allowing them to continue running while changing labels. Their line never stops.”
Nichol explained that at the palletiser, Matthews has two print-and-apply SSCC pallet labellers that apply GS1 compliant labels to each pallet. This system ensures that the pallet, once complete, can be dispatched into the supply chain where it can be automatically scanned through Coles and Woolworths DCs uninterrupted.
“Matthews iDSnet software passes all the completed pallet data back to CCEP where they can update their inventory with finished goods,” Nichol said.
Matthews CEO Mark Dingley describes the level of technology, flexibility and systems capability across the line as “next level”. Dingley said: “I’m proud that Matthews and our very own iDSnet had a role to play in achieving such a successful outcome for CCEP.”
Sustainability built in
The advantage of investing in new technology plays out in increased efficiency and sustainability, and this line lays claim to being the most sustainable production line in the company’s Australian operations, delivering considerable water and energy saving efficiencies.
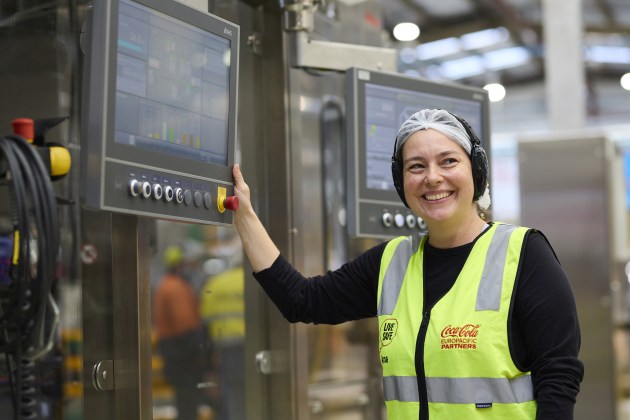
The plant uses less water than existing can lines and CCEP estimates it will save more than six Olympic-sized swimming pools of water every year.
The company also expects its energy use to drop by around 160,000 kilowatt hours each year, mainly because the equipment can fill cans at room temperature; eliminating the energy normally used to cool liquid as part of the filling process.
CCEP vice president and general manager of Australia, the Pacific and Indonesia, Peter West, said the facility reflected the company’s “value-chain approach” to operations.
“[We] continually assess the entire lifecycle of our products to unlock ways we can make, move, and sell beverages more sustainably, whilst ensuring we’re continually driving growth for our valued customers.
“This new can line at Moorabbin allows us to make a larger range of canned beverages from across our portfolio of non-alcoholic and alcoholic brands locally in Victoria, meaning our products are closer to the end-consumer. This minimises freight movements and, in turn, helps to reduce carbon emissions,” West said.
Orlando Rodriguez, vice president of Supply Chain – Australia, New Zealand, and Pacific at Coca-Cola Europacific Partners, said: “The requirement to move product between states in a country as vast as Australia contributes to greenhouse gas emissions and reducing this is a challenging task, but it’s not impossible.
“Our continued investment in more efficient infrastructure at our facilities will play a role in helping us
West also said the Moorabbin site has seen the company improve its gender equality goals by offering career opportunities for women in the supply chain.
“More than 50 per cent of the team that work on the new can line are women, and we’ve increased female representation across our total Victorian supply chain workforce by more than three per cent over the past year,” he said.
New look DC
Near to the Moorabbin site is CCEP’s Mentone Distribution Centre (DC), which has installed a $17.4 million Swisslog Automated Storage and Retrieval System (ASRS).
The ASRS has 12,000 additional pallet spaces to ensure it can support Moorabbin’s increased can production and the efficient dispatch of product orders in Australia’s southern states.
“Combined, the new infrastructure at Moorabbin and Mentone allows us to slash our inter-state freight by more than one million kilometres per year, cutting CO2 emissions by 830 tonnes,” said Rodriguez.
“These two major infrastructure projects work hand-in-glove to help us uphold our commitment great people, great service and great beverages, done sustainably and we couldn’t be more pleased to see them live and operational.”
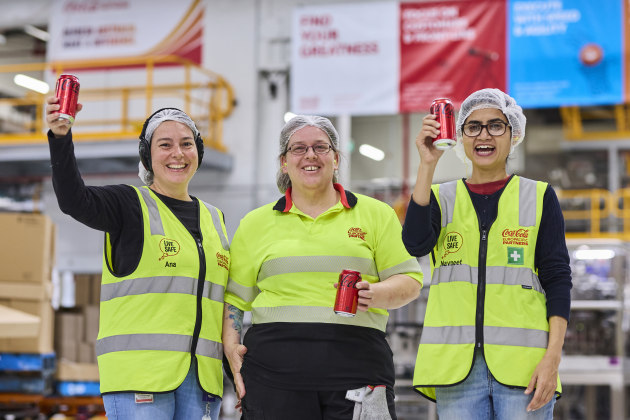