Jamestrong, manufacturer of metal cans for leading Australian and international brands, has partnered with the UNSW Sustainable Materials Research and Technology (SMaRT) Centre on a new project that is set to revolutionise aluminium manufacturing and recycling in Australia.
The Green Aluminium MICROfactorie project will see the deployment of Thermal Disengagement Technology, which has been developed by the UNSW SMaRT Centre, and which now, with Jamestrong's support, is a step closer to commercialisation.
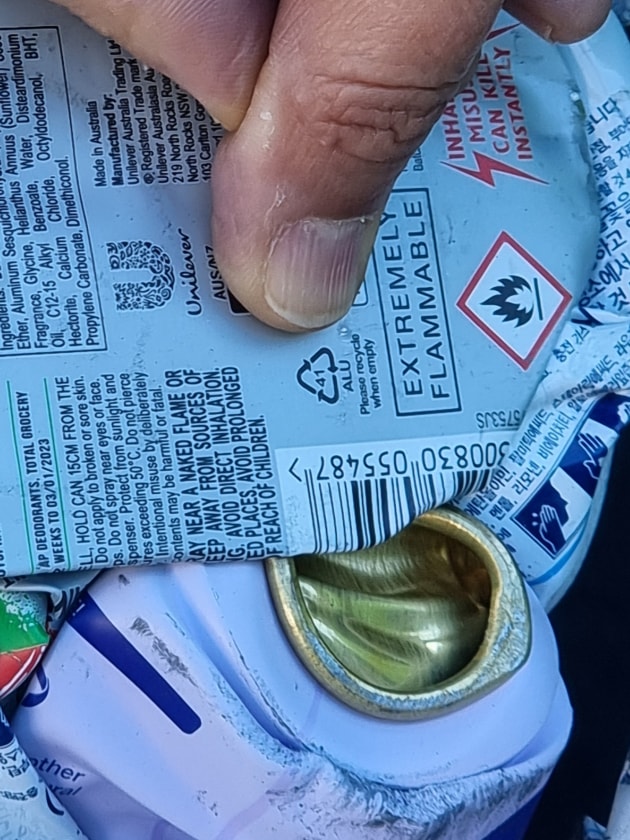
Through this technology aluminium can be recovered from a range of mixed waste feedstocks, including waste packaging.
PKN spoke to Jamestrong CEO Alex Commins, who explained the partnership kickstarts a process that will establish Jamestrong as one of the first aluminium aerosol can producers in the world to not only make aerosol cans from recycled content, but from waste currently not recycled because it contains mixed materials including plastics.
Funded by Jamestrong and UNSW through the federal government sponsored Trailblazer for Recycling and Clean Energy (TRaCE) program, the Green Aluminium partnership will commercialise UNSW SMaRT Centre’s advanced MICROfactorie recycling technology into Jamestrong’s can manufacturing process at its plant in Taree, New South Wales.
Jamestrong last year announced it would be investing $6 million in a new aerosol can plant at its Taree site, and it is here that the SMaRT Centre's Green Aluminium MICROfactorie recycling technology will be trialled and ultimately integrated.
Commins said the aluminium slug manufacturing line should be running by mid next year, which will see Jamestrong reshoring its production of aluminium slugs for aerosol cans, which the company currently imports from Thailand.
The Taree plant manufactures more than 100 million aerosol cans per year.
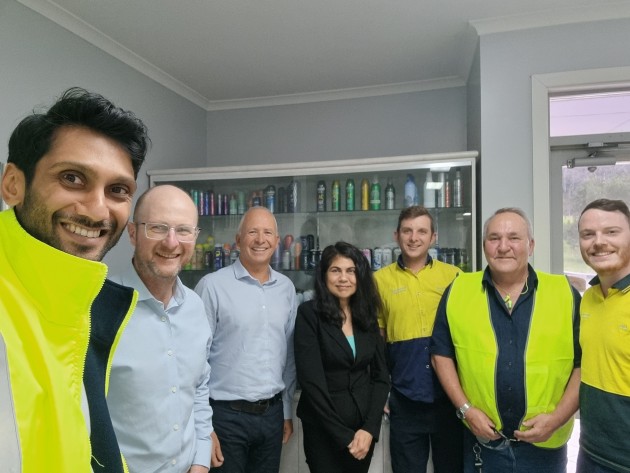
"With UNSW SMaRT Centre, we are advancing our aluminium casting line capabilities in the existing footprint of our plant in Taree. Through this project, recycled aluminium will be introduced into Jamestrong’s aerosol can production process, and the slugs produced on the new casting line will be used in the plant’s extrusion process to create new cans," Commins explained.
"The aim is that ultimately we'll be able to incorporate 100 per cent Australian sourced recycled aluminium into these slugs. It's early days on the project, but the technology is ready and we are committed to developing it to the commercialisation phase."
Commins said Jamestrong was excited to be at the forefront of recycling initiatives in the metal packaging sector, creating a more sustainable future for Jamestrong and its customers.
"The Green Aluminium MICROfactorie partnership will boost local employment at the plant and pave the way for continued progress in sustainable packaging globally," he said.
Professor Veena Sahajwalla, director of the UNSW SMaRT Centre said the partnership with Jamestrong had the potential to transform the use and re-use of aluminium by aligning recycling and manufacturing of mixed waste content, which is currently not subject to traditional recycling processes.
"Our Green Aluminium MICROfactorie technology is able to recover aluminium from a range of mixed waste feedstocks, including waste packaging," she explained.
"The innovative recovery of the recycled aluminium will be incorporated directly into the manufacturing process producing slugs, with varying degrees of recycled content available depending on production requirements."
Jamestrong is one of the largest private company employers in Taree, with 85 people operating the can manufacturing site, which celebrated its 30-year anniversary in 2021.
The new casting line will employ an additional 30 staff during construction and 15 in operation. As part of the partnership with the UNSW SMaRT Centre, additional technicians and scientists will also be on-site.