As the government trumpets headline inflation figures coming down, the reality for many manufacturing businesses is that government charges themselves are skyrocketing, putting a significant burden on business.
Aleks Lajovic, managing director of Australian tube manufacturer, Impact International, based in Smithfield, NSW, is among those frustrated that fees charged by government and statutory agencies are soaring way past inflationary numbers, making operational costs unsustainable.
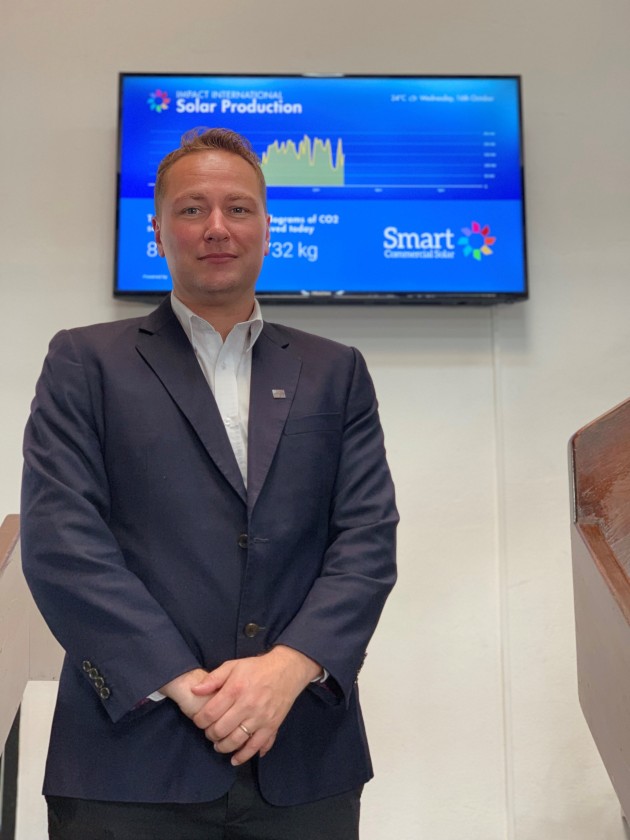
He said, “All levels of government tell us inflation is getting under control and that they are committed to supporting local manufacturing. As a proud Australian manufacturer, we appreciate the sentiment.
“So, with annualised inflation apparently now running at less than four per cent, we analysed some of our cost inputs that are directly controlled or heavily influenced by the NSW state and / or federal government.
“We compared what we paid in 2022 to what we are paying in 2024, and below is the percentage increase over the last two years – it is a sobering read.”
Lajovic’s figures show:
* Local council rates: up 26.6 per cent in two years.
* Total ISR insurance premium: up 46.7 per cent in two years (our insured value was constant).
* NSW land tax: up 74.5 per cent in two years.
* NSW Fire Services Levy paid as part of insurance coverage in NSW: up 26.6 per cent in two years.
* Energy cost per kWh: up 140 per cent (disclosure: Impact did come off a long term contract this year).
* Network charges set as part of our energy bill: up 25 per cent in two years.
* Environmental charges set as part of our electricity bill: up 65.1 per cent in two years.
Lajovic said, “None of these cost inputs show any correlation to the inflation numbers. No manufacturing business can operate in Australia without paying for the above items.”
Soaring land tax, up by a whopping 74.5 per cent in the last two years, translates to higher rents, or for businesses like Impact, which own their own building, an additional extra burden after the costs of purchase.
Lajovic said, “These costs need to stabilise or reduce in 2025 otherwise local manufacturing will only get less competitive and weaker. We are already seeing this with our supplier base shrinking each year.”
The rapidly increasing fees cited by Lajovic, and replicated across many businesses, seem to show the federal and state governments are saying one thing – we support Australian manufacturing – but doing another, in driving up costs so high that work will be driven offshore.
This rings true for northern NSW plastic bottle manufacturing company Ant Packaging. PKN spoke to managing director John Clark, who says in the last six months the company has lost business to imported products due to spiralling costs.
Clark concurs with Lajovic’s findings: “The reality is, it is a real struggle. Insurance and electricity costs are the big killers – and these are government-controlled charges.
“We were looking at investing in a recycling project, and were quite far into progressing this, but while we were doing our research, we visited a fellow recycler and discovered he has had to shut the business because insurance costs hiked from $80,000 a year to $250,0000. We realised then that our project would probably not get off the ground.”
So, while government is making moves to invest in recycling, and is considering legislation that will drive a circular economy, the attendant running costs spiralling out of control will make it impossible for local companies to develop the necessary infrastructure.
Trying to meet these costs impacts the ability to invest in new technology too. John Galea, managing director of label converting business Wagner Labels tells PKN that with order numbers decreasing and volumes slowing, the company is holding back on purchasing new machinery.
“When I look at those figures Aleks has shared, the scary part is the amount these costs have gone up by, they’re spiralling, and this impacts everyone in the value chain. If we’re not investing, our suppliers will suffer.”
Ashley Goldsbrough, director at Dimension1, a NSW company that services the food packaging and printing businesses by cutting materials to size, says the company is finding it difficult to run the business due to high insurance, among other costs. “Our client base is shrinking as businesses close, and we're holding back on further investment for now. We have been in business a long time, much like Impact International, but even though we know things do get better when a recession lifts, there's a lot of pain now.”
Another concern raised by everyone PKN spoke to, is that with businesses closing, or downsizing, the industry is losing valuable expertise and skills that will be difficult to replace.
On the skills front, Brendon Holmes, managing director of Victorian-based packaging company Caps & Closures, says the industry shortage of skilled workers is hampering his business' growth and ability to expand.
“I concur wholeheartedly with Aleks' comments,” Holmes said. “We're being offered government incentives to invest in local manufacturing, but these are in direct conflict with the other costs we're facing.”
PKN has reached out to other manufacturers, and will update the story with further feedback.