Collaborative robots, known as cobots, are emerging as a force for good in the ongoing battle against Covid-19.
Whether they are disinfecting and sanitising, conducting Covid-19 tests, helping to manufacture personal protection equipment (PPE), or ramping up respirator production, cobots can work alongside humans safely or on their own.
They are the answer to accelerating repetitive tasks in the manufacturing environment while simultaneously addressing concerns around social distancing and the safety of employees.
Universal Robots has noted an uptake in the demand for its cobots in various industries across the globe.
Darrell Adams, head of Southeast Asia and Oceania for Universal Robots, said locally the pandemic has seen many companies shifting towards robotic technology to help ramp up production.
“As the fastest growing sector in the robotics industry, cobots are easy to program and deploy remotely. Viewed as a niche product in the past, cobots are now the fastest growing segment in the industrial robotics sector,” Adams said.
“By 2025, cobots are expected to jump from niche status to thoroughly mainstream, accounting for approximately 34 per cent of global robot spend.”
The pandemic has seen an increase in demand for effective deep cleaning and disinfection technologies that do not involve direct human contact with potentially infected areas.
In mid-April, researchers at Nanyang Technological University (NTU) in Singapore unveiled the eXtremeDisinfection roBOT (XDBOT), which comprises a UR5 cobot fitted with an electrostatic spray nozzle all mounted on a mobile platform.
Researchers programmed the cobot to mimic human hand movements so that it can get into hard-to-reach areas such as under beds and tables – a feature that has been missing from traditional disinfection robots that are not as dexterous.
Adams said the team is now preparing to trial the technology at local public hospitals.
“These cobots are capable of running for four hours straight on a single charge and have been successfully tested in public areas on the NTU campus,” he said.
Adams said the UR5 cobot with its built-in safety features can work safely and collaboratively with humans too.
Covid-19 has also resulted in unprecedented demand for medical testing. In response to this extraordinary demand, Universal Robots co-founder Esben Østergaard turned his creative energies to the design and development of the world's first autonomous throat swabbing robot launched by Lifeline Robotics, a company he co-founded with the Maersk Mc-Kinney Moller Institute at the University of Southern Denmark (SDU).
This robot uses UR3 cobot arms fitted with a custom 3D-printed end-effector. The process is simplicity itself, beginning with the patient scanning their ID card. Right away, the robot prepares a sample kit, consisting of a container with a printed ID-label and it picks up the swab. Then, using its built-in vision system, the robot identifies the right points to swab in the patient’s throat. As soon as the swab process is complete, the bot places the sample in a jar and screws on the lid. The jar is then sent to a lab for analysis.
“The process takes around seven minutes and the swab takes just 25 seconds,” Adams said.
Meanwhile, Texas-based portable detection manufacturer, DetectaChem unveiled a smartphone-based Covid-19 testing solution in late May. The company's at-home, low-cost Covid-19 test provides results via smart phone in just 15-30 minutes.
Cobots inherent flexibility helps to support the rapid development and deployment of automation, a feature that comes to the fore in times of crisis. In March, for example, the Spanish car manufacturer SEAT decided to transform one of its assembly lines from its original automotive role to ventilator production. The auto giant installed a UR10e at the end of the line to perform a quality check of the locking mechanism on the unit’s control box.
Based in Ontario, Canada, Hannafin Automation looked to a UR5 cobot to tend the entire 3D printing cycle of face shields. The cobot picked up a Cognex vision camera to inspect the completion of each print. When print is done, the cobot picks it up, places it in a bin, and presses the printer’s touch screen to start a new cycle.
Each printer makes 25 face shields per day and these are donated to local police fire stations, paramedics, and nursing homes.
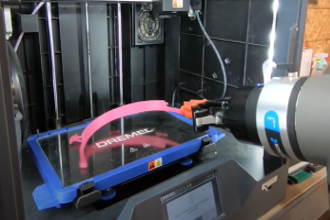
Adams said as the local economy starts to ramp up again, there is an ongoing call by government for more local manufacturing to take place.
“More and more, the country is looking to local, sustainable and cost-effective manufacturing practices to help reaccelerate the sector,” he said.
“Sometimes overlooked, cobots seek to add value in the business and allows employees to focus on strategic tasks rather than repetitive and mundane tasks. We have seen many companies putting flexi hours into place, here, cobots can assist during the downtime and can work continuously to ensure ongoing productivity.”