Experiencing a recent surge in demand for home entertainment, white goods and other personal electronics in the ANZ region as a result of the Covid-19 lockdown, Universal Robots says competition in this sector is tight and leaves no margin for error, and quality is what will differentiate companies from the pack.
Quality has become a defining factor and major competitive advantage for companies offering the same or similar products, and in the manufacturing sector, the pursuit for quality and excellence remains firmly at its forefront.
“Quality is at the heart of every successful business, and for many, it’s a constant chase to maintain and even improve it,” explains James McKew, regional director for Universal Robots Asia-Pacific.
“Every company starts out with the intention of delivering high-class quality to happy customers, however, as the business grows and the production touch-points increase, so do the opportunities for errors, and this is where an increase in cost and a decrease in profits lives too comfortably.
“Our definition of quality goes beyond product features. We focus on a customer’s total costs, which includes lifecycle costs such as expenses on service and maintenance.”
Recently, electronics and entertainment products developer, JVC Electronics, turned to robotics automation company, Universal Robots, to improve its productivity and ensure consistent quality at its subsidiary in Indonesia.
In an age of consumerism, where every cent counts, consumers are demanding higher quality goods at lower costs. At the time, JVC Electronics Indonesia (JEIN) was heavily dependent on manual processes and saw the increasing need to automate.
JEIN manufactures over 400,000 products each month, meaning turnaround time and quality is critical to meeting its production targets, while always still keeping the safety of its workers always top-of-mind.
To meet the electronic giant’s needs, Universal Robots recommended its flexible UR3 collaborative robot (cobot) arm, which is perfect for light assembly tasks and automated workbench scenarios.
The compact table-top cobot weights only 11kg, but has a payload of 3kg, 360-degree rotation on all wrist joints, infinite rotation on the end joint, and a compact form factor – making it good fit for tight workspaces.
Its small footprint is great for benchtops or built directly inside machinery, making it also well suited for light assembly and screwdriving applications.
“Eliminating human error and committing to zero defects ensures zero wastage and a smooth-running production line. This also allows companies like JVC to be more competitive,” McKew adds.
“Compact and lightweight, UR3 cobots were selected as they met the company’s requirement of space-saving, flexibility and safety, along with being easy to operate, requires less maintenance, and is competitively priced.”
Since its implementation, the UR3 relived staff from handling high-risk tasks, such as soldering and separating cut PCB parts, which emit hazardous fumes and dust particles.
Also, with a key feature of the UR3 being its force control for adaptive safety, where the cobot senses external forces and stops immediately when a collision is detected, JVC workers were able to work in close proximity with the machines with no safety guarding after risk assessment.
“These cobots now perform these dull and repetitive tasks while the staff can focus on adding value to the business,” McKew says.
“The company has improved both their production efficiency and output quality, and operational costs have been reduced by more than US$80,000 annually. Thanks to the success of this project, JVC is now looking to deploy cobots in other countries.”
McKew notes that Universal Robots has seen an rise in customers interested in exploring the benefits of cobots to deliver continuous and consistent quality – with emphasis on Australia and New Zealand.
He adds that while automation has had its fair share of resistance in the past, it is now being embraced by manufacturers both big and small, particularly with the urgent need for local manufacturing, reshoring, increased productivity, and competitive pricing.
“Despite being armed with digital callipers and other tools for quality and inspection tasks, human workers simply cannot achieve the same levels of accuracy and consistency provided by cobots – making these tasks an ideal fit for automation,” says McKew.
“Automation is proving to give companies a competitive advantage. Competition is hotting up in our economic climate, where lockdowns, social distancing, additional costs surrounding health and safety, supply chain issues, and extreme pressure on pricing is at the fore.
“In particular, the emergence of cost effective, easy-to-use cobots over the past decade has changed all that, making advanced automation easily accessible to companies of all sizes.”
Universal Robots will be hosting regular webinars help customers get started with cobots and explore automation opportunities.
Furthermore, local support, service and maintenance, as well as training offerings through Universal Robots’ UR Academy, global network of Authorised Training Centres, and UR’s extensive UR+ ecosystems are also locally available.
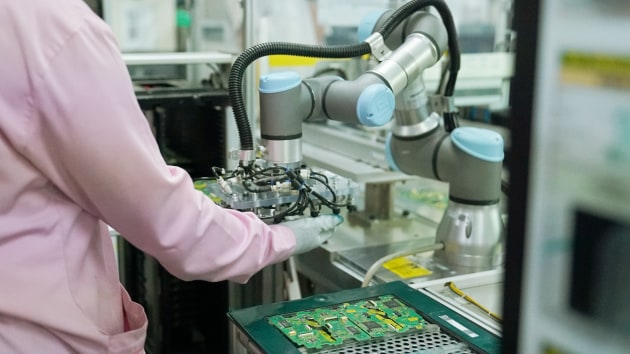