Today, the benefits of automation in the packaging industry are well established – those who adopt automation can reduce labour costs, improve worker safety, and increase productivity. While smaller operators can be put off by the cost or the perceived difficulties of implementing automation in a smaller facility, but being small doesn’t stop you from being smart.
According to research by Global Market Insights, the APAC food packaging market was valued at $125 billion in 2018, and it is expected to grow at a CAGR of over 4.5 per cent, reaching $170.4 billion by 2025. The rise of e-commerce is seen as a key driver of this growth.
For companies to remain competitive and enjoy their share of this market growth, EU Automation's APAC country director John Young says upgrading to smarter facilities will be key.
“The label smart began as an acronym for self-monitoring, analysis and reporting technology,” says Young.
“Today, when technologists speak of smart technology, they usually mean technology that can talk back to us. Smart machines are still in their relative infancy, but machines need to be future-ready so they can scale up when necessary.
“Automation is a key part of smart technology and packaging automation has progressed substantially in recent years.
“What might once have been the preserve of larger facilities, who could afford higher capital costs, is now an opportunity that everyone in the industry can begin to explore.”
Cobots and soft robotics
In the field of robotics, Young highlights two key developments that are allowing increasing benefits for smaller and medium-sized facilities in the packaging industry today – soft robotics and the rise of cobots.
Soft robotics is a sub-field of robotics that deals with the construction of robots from highly compliant materials, allowing for increased flexibility and adaptability, as well as the ability to operate safely around humans.
“This makes them ideally suited for packaging jobs that require a softer touch than your traditional industrial robot,” explains Young.
“In packaging, soft robots utilise silicone-covered tentacle grippers to grasp objects, guided by cameras and sensors that allow for precise and delicate movements. They are being used in picking in the food industry, as they can grasp objects and produce without bruising or damaging it.”
When it comes to cobots, Young comments on the accelerated uptake of cobots across multiple sectors, particularly in the last two years.
“Cobots are robots that are specifically designed to operate alongside human workers, in contrast to industrial robots that are often housed behind safety cages,” Young continues.
“As well as becoming more affordable, cobots are designed for ease of use, removing the need for a highly trained engineer to facilitate their operation. They are usually programmed through a hand-guided demonstration from a worker who requires only rudimentary training.
“Their smaller footprint also makes them an attractive option in facilities where floorspace is restricted. Your average cobot will range in size from 5kg-50kg, so they can be moved around the factory safely and easily.
“A cobot arm utilising soft robotics might be a handy investment for smaller facilities looking to exploit greater automation, but worried about limited space or high capital costs.”
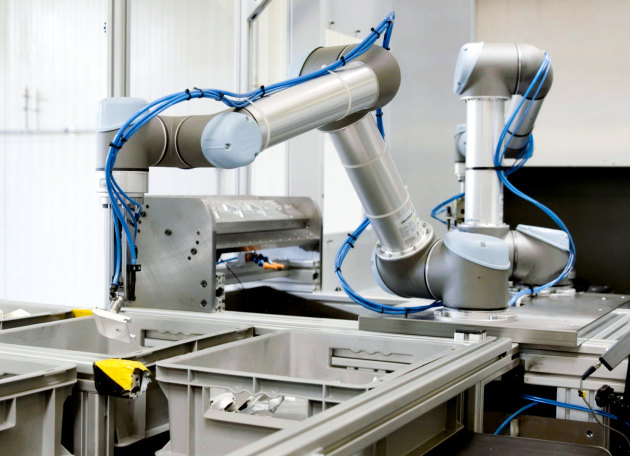
Smart sensors
For Young, investing in automation need not mean an entire system overhaul. Instead, smaller factories can add to their automation capabilities incrementally. And Young says a great way of doing this is by adding smart sensors to pre-existing machinery.
“For example, suppose your existing machine cannot reliably detect when a box flap is up or down. Failure to detect this could cause a halt to the production line.” Young says.
“Adding photoelectric sensors with background suppression help solve this problem. The sensors would scan the angles of the packaging to determine if the flap angle will cause a problem with case-sealing operations.
“Were the sensors to detect a problem, it would automatically send a message to halt the line, allowing an operator to correct the situation.”
According to Young, sensors are highly efficient for inspection tasks such as the one previously mentioned, as they detect faults more reliably and consistently, as “unlike humans, machines don’t get tired or bored”.
And, although there used to be a trade-off, Young says technological improvements have fixed these issues.
“Automating inspection tasks that have previously relied on experienced inspectors was more complicated than, for example, detecting whether a package was opened or closed,” Young adds.
“Similarly, taking high resolution photos for visual inspection often meant compromising on speed.
“Thanks to technological improvements, problems such as these are being solved. Companies are using powerful AI to match the skill of an experienced human operator. The latest cameras, meanwhile, can capture reliable images at speed, meaning the job of multiple cameras is replaced by one.”
Overall, if smaller facilities want to invest in automation, Young suggests they make incremental upgrades and experiment to discover what works best for them.
“Ensuring your factory is ready for the future does not automatically require high capital costs, generous floor space or complete system overhauls. It turns out that being small doesn’t mean you can’t also be smart,” Young concludes.
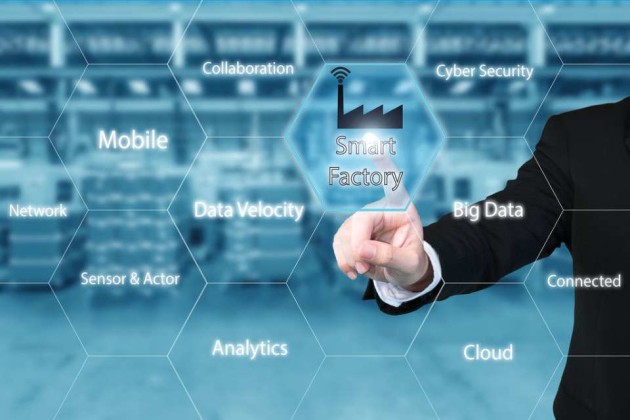