Australia’s brewing industry plays a vital role in the national economy, with around 878 businesses contributing an estimated $16 billion in economic activity and supporting 100,000 jobs across the supply chain.
From large-scale breweries to independent craft producers, the sector has experienced remarkable growth over the years. However, operating in a country with the world's third-highest beer tax presents significant challenges, increasing financial pressure, squeezing profit margins, and reducing market competitiveness.
To stay ahead of these challenges, many breweries are turning to automation – particularly smart automation – to streamline operations and improve efficiencies.
Brewing up innovation
No stranger to the sector, Rod Ryan, head of business development (End Users) at SMC Corporation, has been collaborating with SMC’s customers for more than three decades.
“SMC has worked hand-in-hand with the sector since our early days in the market. We have a sound understanding of their needs and continue to evolve with them,” Ryan said.
“Today, we are able to support all aspects of the production process on-site. We work closely with OEMs to ensure they provide scalable, energy-efficient systems.”
Embracing the 4-bar factory strategy
Like many industries, breweries are increasingly focused on energy efficiency across their production lines.
“We continue to see rising demand for energy-saving systems as producers recognise the importance of saving on energy bills, reducing their carbon footprint and improving efficiencies. One of the most effective ways to achieve savings in a compressed air system is by simply reducing pressure,” explained Ryan.
“Globally, SMC is committed to energy efficiency initiatives. By lowering pneumatic line pressure from the standard 7-bar to 4-bar, our customers can reduce energy costs by up to 29 per cent.
“Breweries can start this process by requesting an energy-saving audit. SMC’s team will review your site and advise on next steps for an energy saving audit.
“Any subsequent system optimisations are conducted at a plant level, rather than focusing solely on individual machines, to ensure savings across the board.”
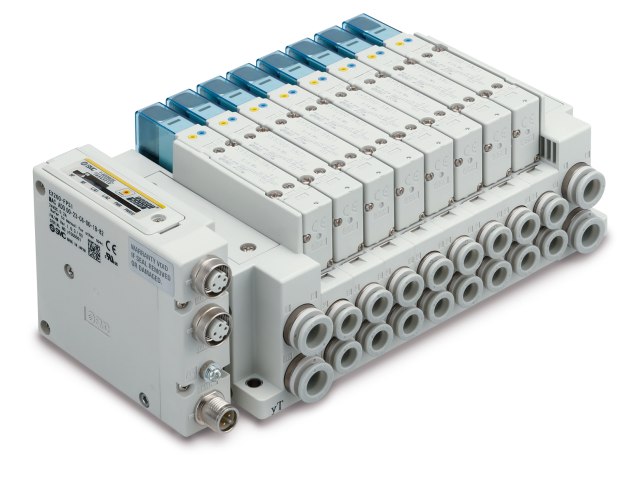
Smart, flexible production for all breweries
Demand is growing for smart, modular and flexible production systems that allow independent brewers to adapt and change quickly.
“This is particularly exciting for independent breweries wishing to scale at will, and wireless products are central to this mission,” says Rod.
“SMC is working closely with our customers to deploy new-generation technologies that will not only save installation time and reduce downtime, but also allow us to perform updates both on and off-site.”
Cheers to two industry heroes
According to Ryan, SMC’s EX series continues to make waves as a unique product offering that delivers a host of big benefits.
“Technologies such as these have shown themselves to be integral to process control and upgrades. In fact, we have seen customers save as much as two days’ worth of shutdowns by simply deploying a solution such as this one,” Ryan said.
He highlights the EX260 as a compact, cost-effective fieldbus solution for output applicable to SMC's most popular directional control valves, such as the SY series.
“It can control up to 32 solenoids in one manifold and is suitable to all major protocols such as EtherNet/IP, PROFINET, EtherCAT, PROFIBUS-DP, DeviceNet and CC-Link,” he added.
The EX260 series has standard dual-port connectivity, eliminating the need for switches or branch connectors. In addition, it’s IP67 enclosure rating ensures protection against dust and washdown environments.
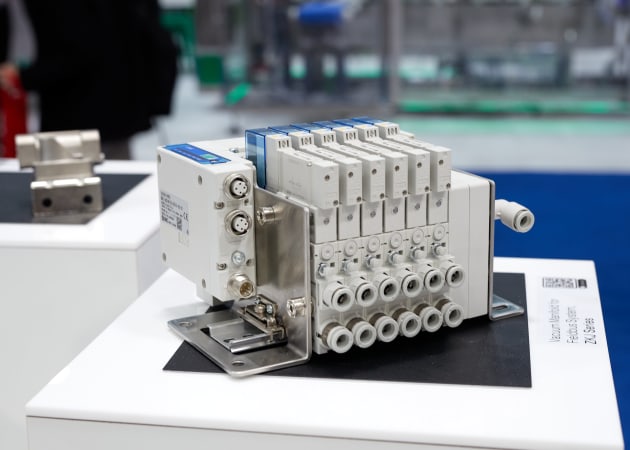
The EX600, on the other hand, offers a full suite of diagnostics and programmable parameters to meet the most stringent requirements.
“This series offers excellent flexibility including digital input, digital output and analogue input unit options. With the use of D-sub output blocks, a maximum of 9 remote D-sub manifolds can be attached to one EX600 communication module,” Ryan said.
Available protocols include Ethernet/IP and PROFINET, and it’s also available as a wireless solution (EX600-W).
To conclude, Ryan said, “SMC is more than just a supplier of automation components, we actively collaborate with our customers – and OEMs – to develop tailored solutions that address both their current and future needs.
“I strongly believe that real energy savings can only be achieved when we work together, and this is why we are so focused on partnering with OEMs from the get-go.
“Through innovative technology and energy-efficient strategies, SMC continues to support the brewery industry in optimising performance and maintaining competitiveness. We look forward to where the next decade takes us.”