New Zealand’s iconic Whittaker’s chocolate company has installed a new, custom-built piece of machinery that can weigh and bag up to six different flavours of chocolates in one operation.
Founded by J.H Whittaker more than 120 years ago, Whittaker’s remains a family-owned and operated company now managed by the third generation, Andrew and Brian Whittaker.
With almost 200 staff at its factory in Porirua, Wellington, Whittaker’s produces chocolate products for the domestic and export markets.
New product, new equipment
When Whittaker’s decided to add a new product line, new equipment was needed at the production facility.
Whittaker’s engineering manager Herbert Aregger approached Enmin Vibratory Equipment to design and build a custom piece of equipment. It needed to be a multi-pack delivery system connected to a six-split multi-head weigher. A crucial requirement was that the new equipment would integrate seamlessly with existing components. It was to be a full turnkey installation by Enmin.
Aregger said the entire project was designed using Enmin’s Autodesk Inventor software and all components were prefabricated outside the country and then shipped to New Zealand for assembly.
“The integration with the other components was seamless. All the mechanical components fitted with minimal or no modifications and electrical interfaces were also prepared by Enmin. The entire process was well thought through,” Aregger said.
“Cabling of the equipment was also prepared and any modifications requested (mechanical or electrical) were taken seriously and executed in a timely manner with good workmanship. Overall, it was a great install with no major issues.”
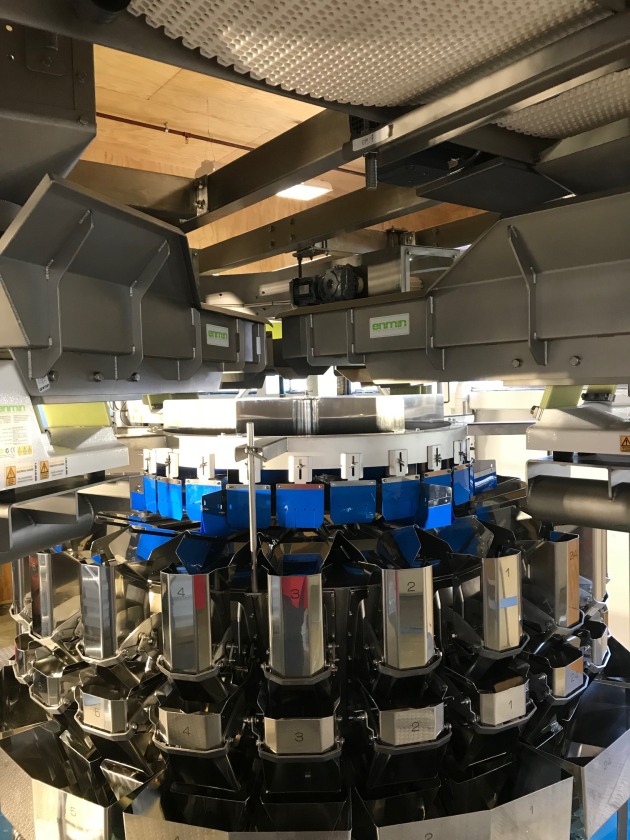
According to plan
The entire installation was delivered in the original time frame. “Since the installation, it has become an efficient and reliable line that’s gone above projected sales,” Aregger said.
Whittaker’s also recently commissioned a mixing line that was designed and built by Enmin. Aregger said, “Enmin has helped us increase our efficiency and productivity and we are very pleased with this new equipment; manual handling has been reduced by 70 per cent and our output increased by double.”
With the help of Enmin’s equipment, there will be plenty more peanut slabs and new confections, rolling out of the Wellington factory well into the future.