Südpack and Ulma Packaging will present two sustainable packaging concepts at this year’s Interpack: flow pack and thermoformed packaging solutions based on mono-materials that are fully recyclable.
Visitors will be able to watch the production of flow packs live on the FM 500 horizontal flow pack machine as well as the production of thermoformed packaging on the TFS 600.
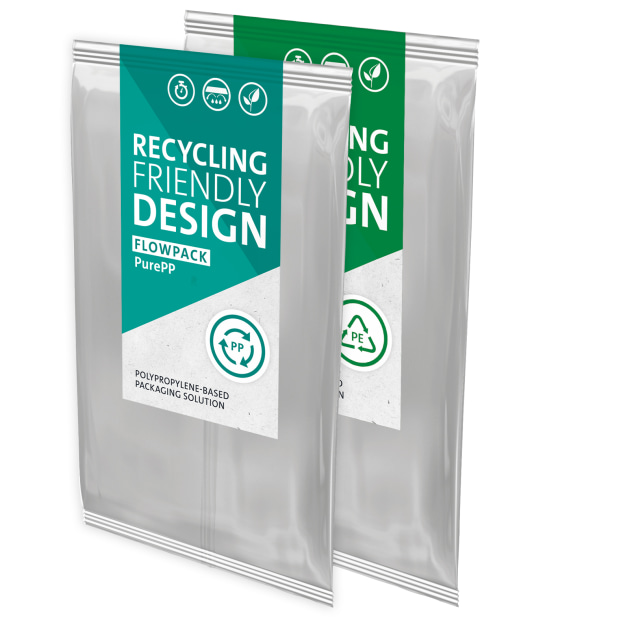
The companies say the focus is on flow pack mono-material solutions as sustainable alternatives to conventional flow pack films. These mono-structures are designed to ensure efficient processing with a high output on standard flow pack machines. They say the solution can be equipped with different barrier properties and combined with a wide sealing range, delivering process and packaging reliability. At the same time, the structure of the sealing layer allows the in-line application of common zipper systems.
Despite their reduced material thickness, the flow packs based on Pure-Line films offer a level of product protection that is comparable to conventional packaging systems and thus prevent food from premature spoilage, the companies say. They also contribute to a significant reduction in packaging weight – for example, material savings of up to 60 per cent can be achieved by substituting rigid tray packaging with flow pack solutions, they added.
At Ulma’s stand at Interpack, Landjäger salami will be packaged in a modified atmosphere on the FM 500 horizontal flow pack machine. The company says this machine can output up to 200 packs per minute and is equipped with an LD (Long Dwell) cross-sealing head, which ensures the packages are airtight even at high production rates thanks to a long sealing time combined with a rotary motion.
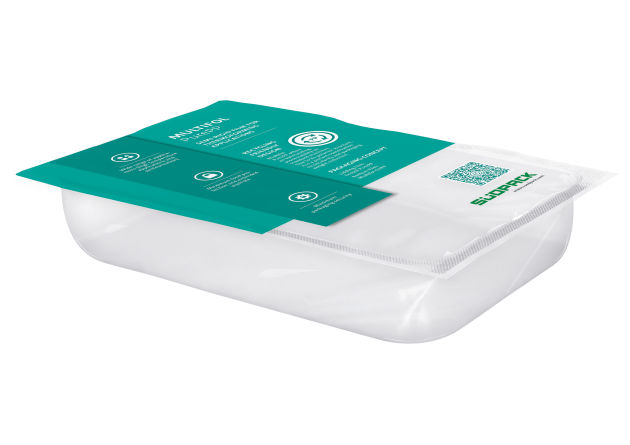
This recyclable flexible film concept for the production of thermoformed packaging is based on Südpack's PurePP film and is processed on Ulma'ss hygiene-certified TFS 600, a thermoform packaging machine designed for the production of both modified-atmosphere and vacuum packaging for a wide variety of food products, according to the company.
Thanks to its thermoforming properties and good machinability, the Multifol PurePP bottom film can be processed on standard machines such as the TFS 600 with only minor adjustments – even at high cycle rates in continuous operation. The top web, an Ecopol PurePP Peel, ensures good sealability. The companies claim the flexible film concept is suitable for a wide range of applications, such as stackable packaging, large-volume gastronomy applications and even fresh pasta.
For those heading to Interpack, you can see all of this and more at Hall 5 Stand C23.