As Covid restrictions eased in early 2022, there was a marked uptick in announcements regarding investments in new facilities and equipment, as well as facility openings and ground breaking on greenfield sites. We bring you a review of major developments this year.
Most recently, Coca-Cola Europacific Partners (CCEP) unveiled a $43.7 million upgrade of its Moorabbin canning facility. The revamp will allow CCEP to produce 11 million more cases of product for the Victorian market.

Processing and packaging partners including APPMA member beverage packaging specialist KHS, which as project lead provided line processing and packaging equipment with robotic palletising systems integrating robots from another APPMA member, Kuka.
Labelling and coding expert, and APPMA member, Matthews Australasia played a significant role and provided a fully integrated solution using iDSnet to integrate CCEP’s ERP (SAP) system with all coding, labelling, and barcode scanning technology across the production line – primary, secondary, and palletising.
The increase in demand for canned beverages across alcoholic and non-alcoholic beverages was reflected in Orora Beverage’s announcement in May, that it was investing $85 million to expand its can body production capacity at its Revesby plant in Sydney. This was the latest commitment from Orora, which is investing around $200 million in can production over the next three to four years.
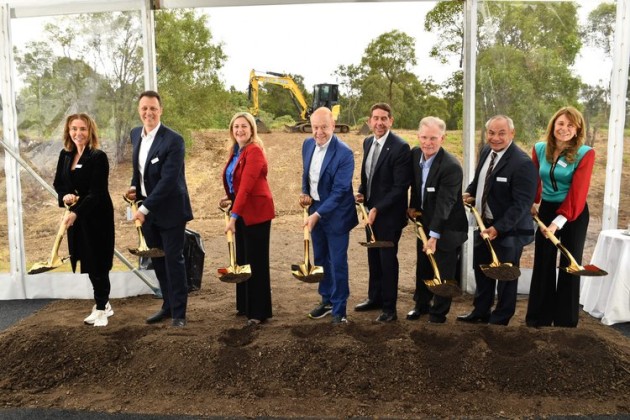
The company is addressing the glass market as well, announcing in October that operations had begun at its $25 million glass beneficiation plant in Gawler, South Australia. It will recycle 150,000 tonnes of post-consumer glass each year, which will enable its glass manufacturing plant next door to produce 900 million glass bottles with an average of 60 per cent recycled content by 2025.
In May, Visy said it was committing $700 million to recycling and re-manufacturing in Queensland.
The company will invest $500 million to build a new glass food and beverage container recycling and manufacturing facility in Yatala; a new $150 million corrugated box factory at Hemmant; and $48 million in major upgrades to the company’s Material Recovery Facility (MRF) on Gibson Island.
Visy will also relocate its current glass re-manufacturing operations from South Brisbane to Yatala, expected in 2025, with the site along the Brisbane River to be used as the International Broadcasting Centre for the 2032 Olympic Games.
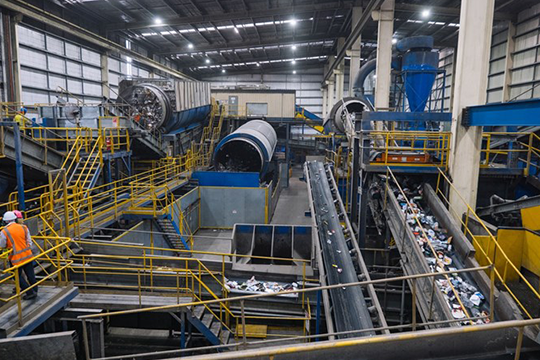
It also increased the processing capacity of its Auckland recycling plant by 28 per cent to 180,000 tonnes a year, with a NZ$16.6 million Covid-19 Response and Recovery Fund.
And in May, Visy announced it could now produce milk bottles made from 50 per cent recycled plastic, following a $29 million recycling plant investment which would divert two million plastic bottles from landfull.
Still with bottling, in April, three contract filling companies from Western Australia (Portavin Integrated Wine Services), South Australia (San Miguel Yamamura Australasia (SMYA) group), and Victoria (Best Bottlers) merged to form Sanector, offering extensive beverage packaging capability.
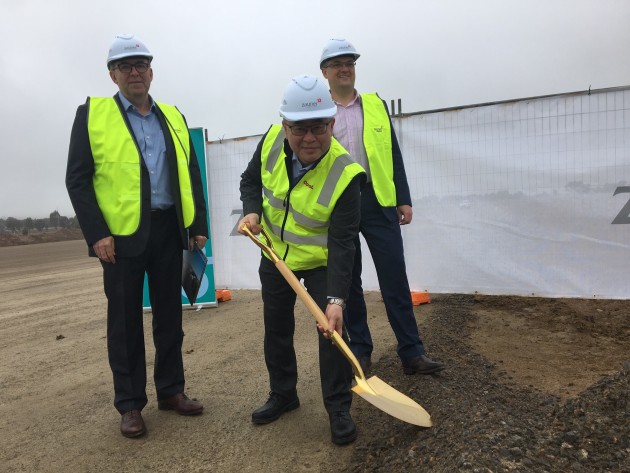
Paper and fibre packaging manufacturer and APPMA member Opal Group is making a major investment to construct a high-speed manufacturing facility for cardboard packaging in regional Victoria. The new facility is a strategic investment by parent company Nippon Paper Group, enabling Opal to meet increasing market demand for corrugated cardboard packaging. The total $140 million investment includes the cost of the land, facility construction, and the technology and equipment – a mix of locally and internationally sourced kit that will fit out the plant.
In April, Perth-based manufacturer of fibre-based linear-formed composite packs, Zipform Packaging, said it would be investing in a new $8 million composite pack manufacturing line in Melbourne, trebling its production capacity. It’s expected to come online in the first quarter of 2023.
Meanwhile, Circular Plastics Australia JV, with CCEP, Asahi Beverages, Cleanaway Waste Management, and Pact Group, opened its first $45 million PET recycling plant in Albury-Wodonga. Its second plant is due to open in 2023 on the outskirts of Melbourne. APPMA member Laco Automation was involved in the equipment supply for the Albury Wodonga facility, which earned it an APPMA Award of Excellence earlier this year.
In the food and beverage sector, there were a multitude of announcements and openings of new or refurbished processing facilities.
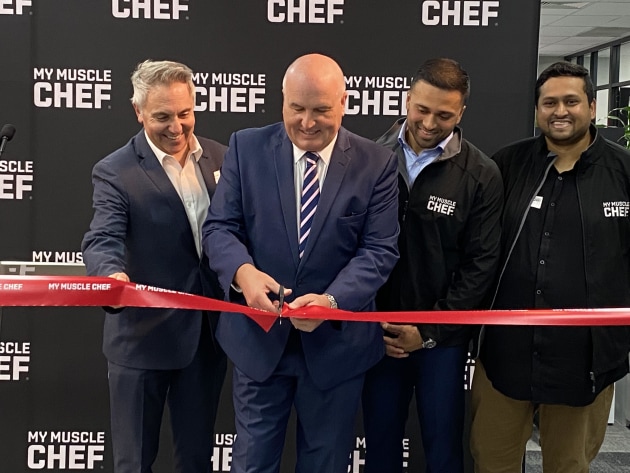
My Muscle Chef opened its new $55 million plant, increasing the ready meal company’s capacity from 500,000 to 1.2 million meals a week. The build and fitout took 2 years and employed around 200 people. It produces 65 different SKUs each week in two production runs, with three lines and room for a fourth. Two of the lines are automated with the remaining line manual. Founders Tushar and Nish Menon are determined that while the business scales it maintains the essence of its products and brand, that of homemade, chef prepared meals.
Another meal prep company Youfoodz also undertook a new build, bringing its three production sites as well as marketing, administration, and distribution all under one roof
Frucor Suntory made its intentions to establish an Australian production footprint known when it announced in March a $400 million beverage production facility in Ipswich, Queensland. The first sod was turned in October, with the project expected to be completed in 2024. It will produce up to 20 million cases of beverages every year, with scope to scale in the future.
Regional Australia has seen some significant investments as well. Plant-based ingredient producer Unigrain announced its plans for an oat milk facility, saying it would be the first in the country to integrate oat processing and oat milk base production. Located in Smeaton, Victoria, once operational it will produce enough fresh oat milk base to support the production of more than 50 million litres a year.
Mars Wrigley has continued its investment in its Ballarat facility with a $25.5 million spend to expand production, increase sustainable packaging, and operational efficiencies. It announced the rolling out paper-based wrappers for its chocolate bar lines in November.
Also in Ballarat, George Weston Foods announced a $133 million investment in a new flour mill, creating around 220 jobs.
Simplot said the $65 million upgrade to its Bathurst manufacturing facility in New South Wales’ Central West will transform the site into “a frozen vegetable centre of excellence”. The plant produces Birds Eye and Edgell shelf stable and frozen vegetable products and the iconic Chiko Roll.
And still in the Central West, tending to the growing market of premium pet food, Nestle’s Purina PetCare facility in Blayney had a $90 million expansion in April, bringing the total invested in the site over the last 10 years to more than $200 million.
Meat processor Frew Foods also announced a multi-million-dollar grant from the Victorian government that will almost double its lamb production, upgrade equipment, build a new cold store, and install a traceability system.
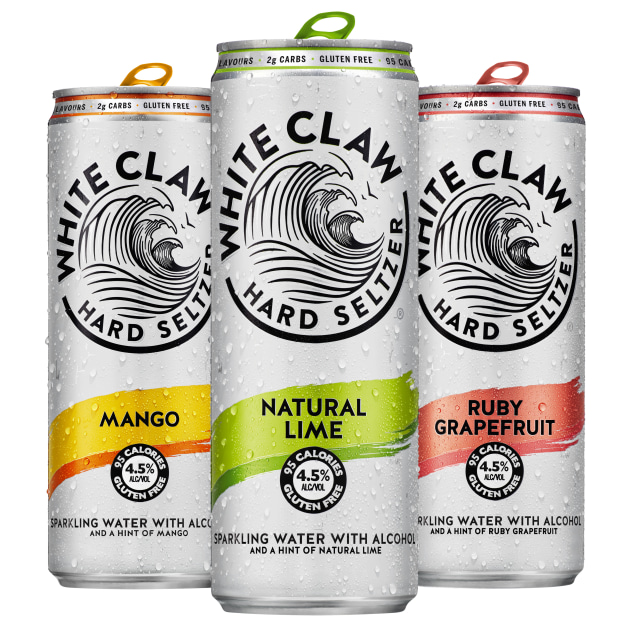
Evidence of shifting consumer preferences was all the more clearer when Lion announced a $5 million expansion of its iconic XXXX brewery would be for the production of hard seltzers, including the domestic production of White Claw, rather than beer. Research firm IRI said the Australian hard seltzer market grew 282 per cent in 2021 to become a $210 million category and now accounts for 16 per cent of the light RTD category. Similarly, recent data from Roy Morgan shows Australian consumption of RTDs (including hard seltzers) is at an all-time high, while beer consumption fell 2.3 per cent.
Another beverage giant, Asahi Beverages, launched its upgraded Wulkuraka manufacturing plant in South-East Queensland. The site will produce more than 300 million litres of soft drinks, iced tea, waters, and juice every year.
Beer consumption might be declining but Treasury Wine Estates shows no concern for wine with its $165 million production facility in South Australia’s Barossa Valley. It is TWE’s largest bottling operation in the world, packaging up to 216 million bottles per year, operating four bottling lines, and exporting to more than 70 countries.
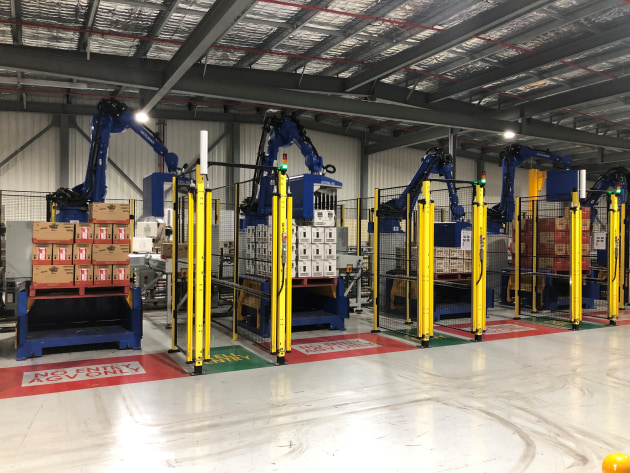
In the land of biscuits and snacks, Arnott’s Group also completed the large-scale $50 million expansion and automation of its warehousing facility at its Huntingwood site in Western Sydney. It can now store almost five times the number of pallets it could previously, and features a 5000 square metre, 35-metre-tall high bay fully automated warehouse.
Kez’s Kitchen worked with specialist food engineering group Process Partners to improve its process flow and efficient use of space. The $4 million project, with a federal Modern Manufacturing Initiative grant, was completed in a record three weeks at the height of Victorian lockdowns.
Cadbury launched its packaging with 30 per cent recycled soft plastic in September and Nestle started rolling out its commercial scale recycled soft plastic wrapper on KitKat bars in June.
One of the biggest commitments made this year was the $378 million investment in the construction of three plant protein manufacturing facilities in South Australia. With funding from federal and state governments, it is being developed by a joint venture between Australian Plant Proteins (APP), Australia’s only commercial scale pulse protein extraction facility, Thomas Foods International and pulse and ingredient supplier AGT Foods Australia. The project will establish the state as a major hub for the growing plant protein sector.