Operational excellence expert Ishan Galapathy explains why we need to improve the food manufacturing sector first, to improve Australia’s manufacturing sector overall.
Since its heyday in the 1960s, the Australian manufacturing sector has declined from 30 per cent to just 5 per cent of GDP.
The Australian food and grocery (AFG) sector remains Australia’s largest manufacturing sector contributing $127 billion turnover – a 32 per cent share of the total manufacturing turnover. The AFG sector also provides employment to approximately 275,000 people of which 40 per cent are located regionally across Australia, with New South Wales, Victoria and Queensland major hubs.
So, if we are to revive our struggling manufacturing sector, we better focus on the AFG sector first.
However, the AFG sector is not growing to the extent it should be. The last ‘State of the Industry’ report published in 2019 by Australian Food and Grocery Council’s states that capital investment is actually -3.5 per cent on a five-year compound annual growth rate (CAGR).
So, what are the challenges we need to overcome?
1) Rising input costs
This has been the number one challenge putting pressure on profit margins and impacting willingness to invest. Many try cost cutting approaches as opposed to cost reduction approaches. This is not just a play on words. World-class companies use structured Operational Excellence (OpEx) methodologies to engage and involve employees to identify and improve year-on-year performance and productivity.
Cost cutting is generally executed by reviewing line items in the profit and loss statement and cutting anything viewed as unnecessary. Such approaches tend to create an environment where employees aren’t engaged; they are uninterested and frustrated.
OpEx methodologies provide opportunities to identify cost reduction initiatives through employee engagement and involvement. The best part of this approach is that most opportunities don’t appear on the profit and loss statement.
2) Data rich yet insight poor:
Many businesses are obsessed with technology and data collection, yet they don’t have the fundamental OpEx processes for providing insights to employees.
Holding effective daily huddles to understand if they are winning or losing and establishing a cadence to identify real improvement opportunities are essential elements of an effective OpEx framework.
In his bestselling book, Atomic Habits, James Clear writes, ‘You do not rise to the level of your goals. You fall to the level of your systems’. I couldn’t agree more.
3) Two steps forward, three steps back:
A recent study conducted by University of Technology Sydney (UTS) on behalf of the Australasian Supply Chain Institute (ASCI) found that in 2018-19 our overall supply chain maturity dropped by six percentage points from 52 to 46 despite off-the-Richter-scale advancements in automation.
Many businesses implement technological solutions without first trying to understand the strategic problem that requires addressing. Clearly, this approach is not working.
While the Australian government is now investing $1.5 billion through technological advancements to resuscitate this ailing sector, most of our Australian factories are struggling to leverage technological interventions.
If you want to advance the Australian manufacturing sector, focus on improving productivity in the AFG sector:
1. Focus on the basics: Establish production rates, waste levels, changeover times, number of employees per product and so on, to understand the base performance level.
2. Learn structured problem-solving methodologies: Improve year-on-year performance.
3. Make it effective first and efficient second: Create basic processes first, then work on technological enhancements.
Solving day-to-day chaos doesn’t improve year-on-year performance, so re-evaluate your improvement approach.
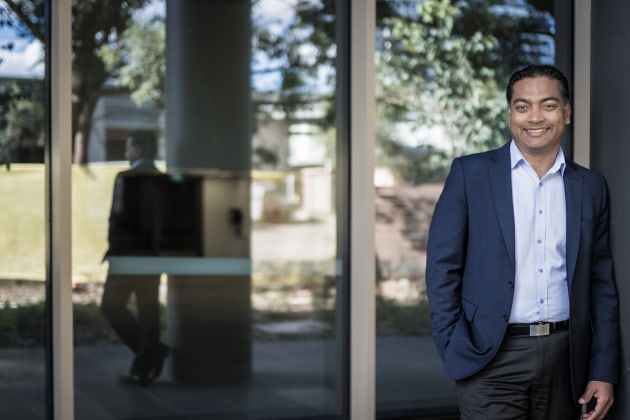
Ishan Galapathy, author of ‘ADVANCE: 12 Essential Elements to Supercharge Productivity & Profitability’, has a wealth of knowledge in the field of Operational Excellence (OpEx), having worked in this field across six countries for over two decades. Renowned for his simplified techniques, Galapathy works with manufacturing businesses to help them move from 'Chaos to Excellence'.