In order for local manufacturers to harness the possibilities unlocked by implementing advanced manufacturing techniques, they are going to need to be ready to embrace change, and at the Modern Manufacturing Expo (MME) Romar aims to show them how.
“Advanced manufacturing is about breaking new ground – it sometimes involves the manufacturing of products that have never been made before, changing the way in which you currently manufacture, or sometimes it means finding out how to make hundreds of the one product you have created,” said Alan Lipman, CEO of Romar Engineering, who will be exhibiting at the upcoming MME in September.
“The manufacturing process required to produce cutting-edge products often requires similarly modern machinery and materials, with material science playing a big role in advanced manufacturing.”
Romar delivers complete and scalable solutions to manufacturing problems in a wide range of applications, including the medical, aeronautical, aerospace, defence, rail and industrial.
Romar Engineering understands the benefits of advanced manufacturing and have invested heavily in enhancing their local capabilities.
“We recognised its potential early on and invested heavily in making sure that we had the latest in equipment, software and people to make sure that we could deliver on what is required to implement these solutions,” explained Lipman.
“Innovation is key here. We have an entire project team whose focus is on doing R&D work for customers – testing materials, testing different processes, and creating designs to help identify the solution best-suited for their needs.”
Must be scalable to be advanced
The guiding principle at Romar is to deliver manufacturing solutions that are scalable, and the company guides customers who maybe in the early stages of building something to figure out how they can use advanced manufacturing techniques to make hundreds, or even millions, of the same product.
“They bring us their prototype product and we help them to manufacture at volume so that they can reach commercial levels of output. Smart scaling plays a big role in making Australian manufacturers more competitive,” said Lipman.
Another crucial component of ensuring that local manufacturers remain competitive is using advanced manufacturing techniques to increase efficiencies across the production line.
Lipman also believes that considering scalability and efficiency gains when implementing new technologies and techniques will enable manufacturers to evolve.
“Advanced manufacturing is about finding efficiency in what you do – there are a range of options to choose from, and you can manufacture goods in many different ways, but at its core, advanced manufacturing will bring more efficiency to your business,” he added.
“Traditional manufacturing methods will always be around, and rightly so, but considering a new approach maybe what’s needed to give you an edge over the competition. This is why Romar continues to invest heavily into product and process development.”
Not just a financial investment
There’s no denying that there is a significant initial investment required to implement advanced manufacturing – both in financial and time requirements.
This may explain why there has been some hesitation amongst local manufacturers to begin their transition to modern manufacturing, despite the obvious benefits, such as increasing competitiveness and enhancing local capabilities.
“We see a number of customers who want to re-shore, but because local manufacturing can be expensive due to high labour and material costs, we need to ensure a higher quality product, or higher production output to justify this expense,” said Lipman.
“This is why we stress the importance of considering all aspects of a new production process before making any investment.”
Another aspect that manufacturers must consider before embarking on this journey is the need for expert guidance.
“None of these tools are plug and play, and if you buy an advanced piece of equipment, you must ensure that your company either has the internal capabilities, or is working with people who will help you derive its full potential, both in the short and long-term,” Lipman explained.
“There is quite a lot of complexity involved in becoming an advanced manufacturer, which is why we try to keep things as practical as possible when working with customers.
“Our approach is designed to take the guess-work out of transitioning to advanced manufacturing, by staying solutions-focused.
“We do a significant amount of work internally to understand and extend the manufacturing capabilities of our equipment and processes in order to get the desired end result for the customer, not generally available from other competitors in the market. This approach is driving growth at Romar, both in customer numbers and employees.”
Compete with overseas manufacturing dollar-for-dollar
A robust approach to testing gives Romar a realistic perspective on the possibilities and limits of advanced manufacturing, and Lipman said that they are always happy to share the knowledge they have gathered over the years with local manufacturers.
Lipman and his team feel that the more local capabilities are enhanced, the more investment will be made in people, equipment and skills training, and this will be beneficial to Australia in the long-term.
“We are an open book and welcome anyone who wants to come and see what we’re doing and why,” he said.
“We can compete with countries such as China at volume – they’ve had an advantage over us in labour costs, but when manufacturing at high volumes, you’re basically engineering the labour out of it.
“Romar has run the numbers and when it comes to quality, output speed and labour skills, Australia performs very well in those respects, and once you consider the costs involved in overseas manufacturing – shipping, export fees, exchange rates and country risk – we compete dollar-for-dollar, all the advantages are here.”
The movement to strengthen and advance Australian manufacturing is a core focus of the upcoming MME, organised by the International Exhibition & Conference (IEC) Group.
“We are extremely happy to have a company with the calibre of Romar Engineering onboard for the MME, and we look forward to continued discussions on how our organisations can work together to advance manufacturing in Australia,” said Marie Kinsella, IEC Group CEO.
Romar will have several members of their engineering team at the Expo to answer visitor questions.
“More than anything, we are looking forward to the interesting discussions that will take place, bringing advanced manufacturing to the top of the agenda,” said Lipton.
“It will be a great opportunity to network with the industry and identify opportunities for collaboration. We are always interested in finding companies to partner with, so we can expand our manufacturing and skills base.
“Advanced manufacturing is relatively new, and it is important to talk to as many people as possible and ask all the questions you may have, to better understand the possibilities it can unlock in your own business. There is no such thing as a dumb question.”
The MME will take place at the Sydney Showground on 20-21 September. The event includes over 50 exhibitors, free access to the Expert Arena, and a ticketed Smart Manufacturing Conference on Tuesday, 20 September.
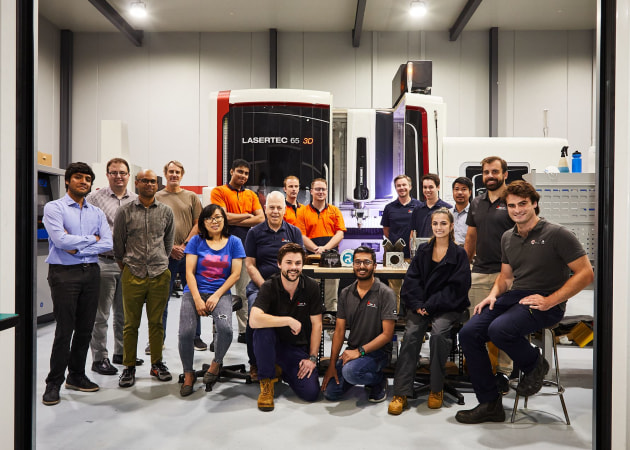