Nearly 36 per cent of all plastic produced worldwide is used to create packaging, 85 per cent of which ends up in landfills or as unregulated waste. Traditional packaging materials like expanded polystyrene (EPS) foam, which have become popular for their durability, low cost, and versatility, are costing us dearly. In landfills, this popular plastic leaches toxic chemicals into soil and groundwater and releases methane – a far more potent greenhouse gas than CO2.
Thankfully, nature has a solution to tackle the packaging waste crisis: waste wool.
While waste wool is unusable in the textile industry, it possesses all of the excellent protective and thermal characteristics of wool fibres. It is also reusable, compostable, and recyclable. As the founder of a sustainable packaging company [Planet Protector Group], my experience with waste wool has been nothing short of transformative. In this article, I share why leftover waste is an unexpected but powerful solution that this plastic-choked world desperately needs.
The problem with conventional packaging
A large majority of plastic packaging, like polystyrene, does not break down in nature. It only fragments into tinier and tinier pieces with the help of sunlight and wind. These pieces are small enough to invade every inch of the environment. In the waterways and ocean, they are often ingested by marine animals, resulting in internal injuries and death.
Many companies market styrofoam packaging as recyclable. Technically, yes, it is recyclable, but the additives used in this material are a nightmare to separate. Moreover, the lone recycling technology capable of salvaging EPS is itself highly toxic and polluting.
The environmental harms linked to plastic packaging waste are fueling numerous regulatory interventions across the globe. For example, the EU charges its member states a uniform tax of €0.80 (A$1.31) per kilogram on non-reusable and single-use plastic packaging. The member states have the option of financing the tax by passing the costs on to producers and consumers. Another tool that many European countries are relying on to curb plastic waste is Extended Producer Responsibility (EPR). Under this scheme, producers are held legally and financially responsible for the management of their products and packaging, including their disposal.
In the US, 11 states and hundreds of cities and counties have passed laws to ban or phase out the use of expanded polystyrene. The mounting scrutiny and shift in consumer attitudes are forcing businesses to find sustainable alternatives to conventional packaging.
Wool’s natural advantages over plastic
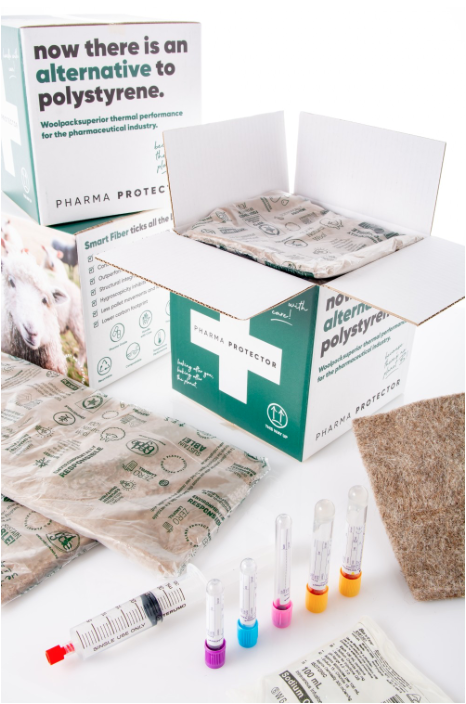
Wool’s naturally smart fibres trap and release moisture from the air even when they are inside a box. This gives them superior thermal insulation and moisture management abilities while being an environmentally-responsible alternative to plastic foam. During manufacturing, polystyrene releases numerous chemical by-products, including large amounts of ozone, causing environmental harm and affecting the health of the community living near the production facility. Unlike polystyrene, wool is abundantly available in nature as a by-product of raising sheep.
Research shows that wool fibres are 100 per cent biodegradable in terrestrial and marine environments. When they break down, wool fibres release valuable nitrates back into the earth. Polystyrene, on the other hand, never fully disappears and continues to pollute our planet by only breaking down into microplastics. In landfills, polystyrene leaches styrene, which the International Agency for Research on Cancer (IARC) classifies as “probably carcinogenic” to humans.
In addition to its vast environmental benefits, wool is also a space-saving material. The high resiliency of its fibres means wool packaging can be flat-packed to save space. It’s also light and easy to move around. Businesses that switch to wool-based packaging not only cut down on logistics costs but also lower their transportation-related carbon emissions.
Rethinking waste – the wool solution
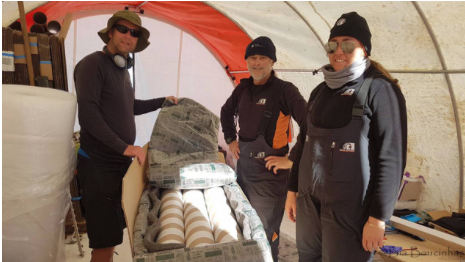
According to industry estimates, about 50 per cent of wool is thrown away in the sheep-farming countries of Norway, Austria, Sweden, and Switzerland. Wool from sheep raised for meat and dairy is a vastly underused resource. Its coarseness makes it valueless to the textile industry, leaving farmers with no other option than to send it to landfills, dispose of it into the soil, or incinerate it.
In our search for a sustainable yet commercially viable alternative to polystyrene, we rediscovered waste wool. We sourced crossbred from Australian and New Zealand sheep farms where livestock is primarily raised for meat. The wool is a byproduct of annual shearing – a process necessary for the welfare of sheep. This wool, being of lower quality, usually ends up in landfills. At Planet Protector, we channeled this waste stream into creating high-performing packaging solutions and a steady source of revenue for domestic sheep farmers.
Our waste wool packaging outclasses polystyrene in various parameters, including protecting temperature-sensitive products such as frozen food, vaccines, and pharmaceuticals during transit and delivery. The wool fibres breathe and create a natural cooling system to insulate products. Flat-packed Woolpack liners also enable companies to optimise warehouse storage space and reduce pallet movements and freight costs.
Circular economy in action
Wool checks all boxes of circularity. It is reusable, recyclable, and home-compostable. In fact, wool is the most reused and recycled fibre among the most common apparel fibres. A by-product of sheep rearing makes wool a renewable and abundantly available resource. Sheep grows new fleece every year and needs seasonal shearing for overall well-being. Fleece shorn from sheep’s hindquarters or belly is generally considered too coarse for fabric production. At Planet Protector, we’ve transformed low-quality waste into insulating Woolpack liners that are fully compostable at their end of life.
Waste wool packaging not only reduces environmental impact but also benefits local economies. We only use wool sourced from Australian and New Zealand-based sheep farmers, creating a market for leftover wool otherwise destined for landfills. To date, we’ve replaced 20 million polystyrene boxes from supply chains, diverted 8,000 tonnes of waste wool from landfills, and generated nearly $15 million in revenue for local sheep farmers.
Industry impact and the future of sustainable packaging
Consumer demand for sustainable solutions and intensifying regulatory efforts are fueling a transformation in the packaging industry. Wool, a readily available, naturally insulating, and inherently circular fibre, has the potential to become a commercially viable and cost-effective alternative to polystyrene packaging.
At Planet Protector, we’re on a mission to make the waste wool supply chain sustainable and disruption-proof. Approximately 90 per cent of Australian wool clip is sent overseas for cleaning and scouring. With the launch of our manufacturing facility in Victoria, we’re ready to bring fibre processing back to Australia.
Capable of processing 150 tonnes of fibre each week, this facility will not only enable us to scale up the production of Woolpack products but also introduce wool-based solutions to more industries and markets. For example, the launch of our 100 per cent sheep wool building insulation will help the Australian construction sector reduce its consumption of expanded polystyrene. Our sovereign fibre manufacturing line also enables us to expand Woolpack across Asia, starting with India and Singapore.
Make the switch
Sustainability in packaging is a trend no business can afford to ignore. Having insidious plastics like EPS in the supply chain can leave your business exposed to regulatory pressure, negative public perception, and increased operational costs.
By switching to circular wool-based solutions, your company can build a competitive advantage, reduce packaging waste, and create long-term business value. For forward-thinking leaders and business owners, the choice between sticking to the status quo or prioritising sustainability is a simple one.
Woolpack is proof that the right materials and innovation can pave the way for cost-effective solutions that are environmentally and socially responsible.