While chemical recycling capacities are showing signs of growth globally, legislation surrounding chemical recycling is still lacking. Joshua Dill, analyst for Plastics Recycling at ICIS, considers the importance of mass balance in chemical recycling.
The global chemical recycling capacity has the potential to grow 8x from its current position by 2029 if all projects (including pre-FID) come to fruition, according to data from the ICIS Recycling Supply Tracker – Chemical.
For the chemical recycling industry to realise future growth, it would be beneficial to establish clear guidelines as to how companies can allocate chemically recycled material to their products as they try to hit recycling targets. The lack of guidance in this area adds to the overall uncertainty around chemical recycling from a legal standpoint, which negatively impacts investment in the nascent industry. Investments in chemical recycling are important to broadening the scope of recyclable feedstock by targeting those plastics and their specific applications that are not suitable for mechanical recycling.
Mass balance is particularly challenging with thermal depolymerization/conversion recycling, even when compared to other types of chemical recycling, at these processes typically produce more than one output. As a result, the input recycled material must be distributed to various outputs, complicating the mass balancing process. Since thermal depolymerization technologies (i.e., pyrolysis and gasification) are expected to have the largest growth globally based on announced plants, mass balance is now at the center of many discussions.
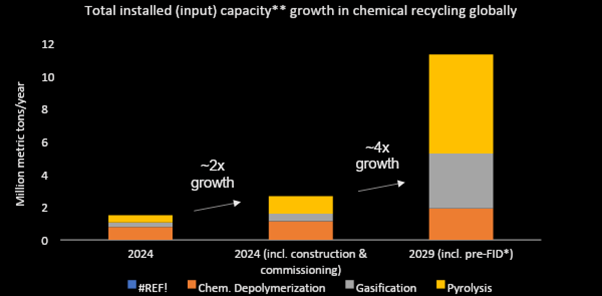
Chemical recycling and mass balance
Mass balance is a method of bookkeeping to ensure proper allocation of input material in the final product. As the chemical recycling industry continues to grow and mature, the concept of mass balance is becoming increasingly important to maintain clarity on how the recycled material is being allocated.
Chemical recycling is an umbrella term that encompasses many different processes to chemically break down plastics into its constituent parts. Thermal depolymerisation is a subgroup of chemical recycling that involves processes that break plastic down with heat and pressure. One example of a thermal depolymerisation process is pyrolysis, which is mainly used to turn polyolefins (PO) such as polyethylene (PE) and polypropylene (PP) into pyrolysis oil.
Pyrolysis oil — whether directly or after being refined — is mixed with virgin material before being further processed. This mixing happens early in the supply chain, and once it does, the virgin material is indistinguishable from the recycled material. At this point, mass balance takes effect to keep track of the recycled portion of the overall mixture.
As this mixture continues to be processed, it is separated into various chemicals and fuels, all with their own potential end-use applications. Although the total amount of recycled material that was inputted at the start of the process is known, how these recycled units are allocated to each output will vary based on the type of mass balance approach adopted.
Different Approaches to Mass Balance
Free allocation is a method of mass balance that allows for the total allocation of recycled material to be in any output. This allocation method would benefit advancements in the chemical recycling industry by providing the best cost incentives to chemical recyclers, making investing in the space more appealing. Although they cannot claim more recycled material than was inputted, they can claim all the recycled input in the polymer portion of the output to maximize value. Hence, the chemical recycling industry favors mass balance that errs on the side of free allocation.
There is pushback on this style of mass balance by certain non-governmental organizations (NGOs), mechanical recyclers, and waste management companies. NGOs often say that the production of fuels in processes such as pyrolysis should not count as recycling because the production of fuel does nothing to reduce the reliance on virgin plastic and the fuel itself cannot be recovered once it is used (not closed-loop recycling). However, if thermal depolymerization is considered recycling, NGOs believe that free allocation should not be adopted. NGOs—along with mechanical recyclers and waste managers—agree in principle that a free allocation approach would lead to unreliable recycling claims about recycled content to consumers, with recycled material that should have been allocated to fuels or other outputs being claimed on plastic products.
Mechanical recyclers and waste managers have additional concerns about the incentives a free allocation approach provides. The added cost benefits could lead to a competitive market edge for the chemical industry on recycling, putting chemical recycling in a position to compete with mechanical recycling rather than complement it. Furthermore, the parties cite that adopting a method of mass balance that allows for an easy integration with current technologies used to produce virgin plastic would hinder the transition away from virgin plastic.
Those who oppose free allocation suggest a stricter method of mass balance called proportional allocation as an alternative. This method of mass balance proportionally distributes recycling units to each output based on the amount formed. Advocates for proportional allocation cite this style of mass balance as being more scientifically justifiable—that is, it better aligns with how the recycling units are realistically distributed in the final output.
There are other mass balance approaches that are not as extreme as either free allocation or proportional allocation, but instead lie somewhere in the middle. The fuel-exempt approach, for example, dictates proportional allocation of recycled units to fuels, while allowing free allocation of the remaining recycled units to all other outputs. Alternatively, there is the 'polymers-only' method, which dictates proportional allocation of recycled units to all outputs except polymers, which can be allocated freely.
Each of these methods have their pros and cons, and ultimately lead to different claims of recycled material content in the various outputs. The chart below shows possible virgin and recycled combinations for different output scenarios depending on the mass balance approach adopted.
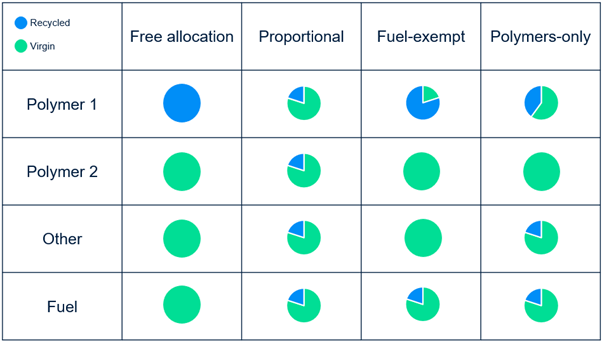
Currently, the official adoption of chemical recycling in legislation is unclear, while mass balance considerations are further down the road. In the United States, for example, the adoption of chemical recycling is happening on a state-by-state basis, with 25 states currently onboard. Mass balance claims, on the other hand, are typically certified by external bodies such as the Internation Sustainability and Carbon Certification (ISCC) system.
The European Union (EU), for comparison, is developing an EU-harmonized method. Directive 2008/98/EC (Waste Framework Directive) — the piece of legislation most cited to provide a legal definition of recycling — does not make the full recognition of chemical recycling clear. In the EU, mass balance claims are similarly certified by bodies such as the ISCC system.
Regardless of the type of mass balance approach adopted, without the coadoption of chemical recycling and mass balance, the chemical recycling industry will continue to be shrouded in uncertainty, leading to hampered industry growth.