When Schulz Organic Dairy started supplying milk in returnable glass bottles to close the packaging loop, demand soared, but a shortage of sanitised bottles soon became a challenge. The dairy company turned to Rhima Australia to develop a bespoke bottle washing system.
For third-generation family-owned dairy business Schulz Organic Dairy, sustainable production is deeply ingrained in the farming and processing practices, and this extends to its packaging too. The company is run by father and son duo Michael and Simon Schulz, operating from their farmhouse factory in Timboon, Victoria. Both believe that creating a circular economy is the only way to truly minimise waste.
Simon Schulz first started supplying milk in returnable, refillable glass bottles at farmers markets in 2017, but found the product sold out quickly due to popular demand, and the turnaround on the bottles wasn’t fast enough to keep pace. Simon then launched a successful crowdfunding campaign to fund the installation of a bespoke washing line at the farm to get more bottles into the cycle.
As a next step, Schulz Organic Dairy reached out to Rhima Australia to develop and manufacture a bottle washer that could wash the custom design bottles, a crucial component to match supply with demand.
HOME-GROWN DESIGN
The brief was to design and build a washer/sanitiser that would wash and sanitise bottles to a HACCP-approved level. It had to provide ease of use and operate at optimum capacity, while at the same time minimising energy and water consumption. The machine had to be commercially viable for application in similar re-use environments
The bottle washer was designed and built in Australia by the Rhima team, drawing on its expertise with other bottle washing systems.
Commenting on the design process, Rhima CEO Mark Hollingsworth explains, “Industrial bottle washers exist but most are geared up for very large production runs in fully automated environments. Smaller bottle washer/sanitisers are available also, but they are mainly aimed at the laboratory market with low capacities and long cycle times.
“The Rhima design team started with one of our standard industrial washers and modified both the wash and rinse system as well as the programming and racking to achieve a design that met the required criteria.
Hollingsworth continues, “In particular, the special racking design, injection system, control system, and component selection required a lot of R&D. This is to ensure that the bottles are 100 per cent clean while using minimal water and energy.”
The Rhima bottle washer has been designed with an injector wash arm that allows each bottle to have its own spray nozzle.
During the design and build process, the design team ensured suitable temperature controllers with temperature probes were selected to deliver the best wash result at the required temperature outlined in HACCP guidelines.
“The unique design of the water injection system ensured all the inner and outer area of the bottles receive appropriate impact from water to rid milk residues,” Hollingsworth says.
“The washer allows the reusable glass bottles to be available on the market. Without the ability to wash and reuse them hygienically this sustainable venture wouldn’t be possible,” he adds.
“The washer improves hygiene and cleanliness as well as efficiency. If the glass milk bottles are not cleaned and sanitised properly or at all, and milk residue remains, this creates a food safety hazard for Schulz and the dirty bottles must be thrown out due to their contamination risk.”
CIRCULAR PROCESS
Schulz’s returnable glass bottle system is designed to deliver a circular process for waste elimination, cutting out both recycling and landfill. All (clean) returned bottles that Schulz receives are rewashed, sanitised, and refilled inside its processing facility. Customers are encouraged to wash the bottles and remove the plastic closure and cardboard sleeve (all kerbside recyclable) before returning it via the retailer or farmers’ market where it was initially purchased.
Schulz has implemented an additional element – a $2 refundable deposit per glass container unit. The company says this will ensure it will get many uses out of these glass bottles and it believes that putting a price on the vessel is the best way to do this. Evidence Schulz gathered from overseas markets showed that a container deposit scheme ensured a bottle was more frequently returned if a deposit was requested. Schulz hopes that a returnable deposit helps incentivise consumers and retailers to return the bottles.
The company estimates that each bottle will have a lifespan of at least eight refills, although the re-use has in fact been higher than that to date. Schulz’s custom-moulded bottles have the year of manufacture embossed into the glass, which is an indicator of the bottle’s longevity.
The packaging and reusable bottles have played a role in supporting Schulz’s circular ambitions, however, it wouldn’t be a viable project without the efficient HACCP-compliant washing system. Nor would the reduction of plastic use be possible. According to Schulz, each glass bottle sold saves approximately 40g of plastic, or 120 kg per week across 3000 bottles.
It’s fair to say the partnership between Schulz and Rhima has led to a reduction in packaging waste, while creating a replicable business model with potential to become an important contributor to the circular economy.
This article was first published in the November-December 2022 print issue of PKN Packaging News, p42.
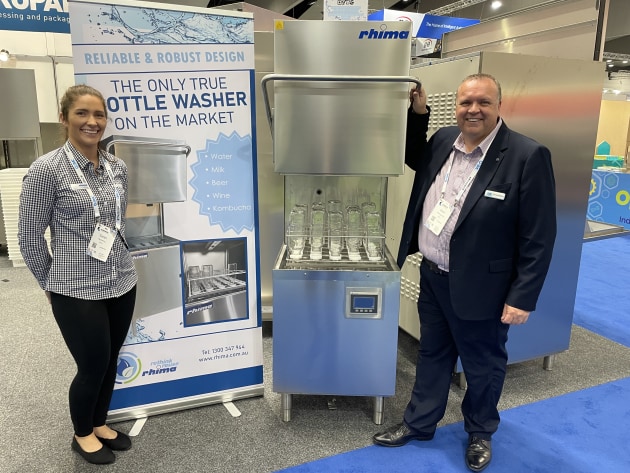