West Australian craft brewer Blasta Brewing Co has installed a new Krones Craftmate C filler and Ferrum seamer in its production facility in Perth. This is Krones’ first installation of the filler in WA, and the ninth of its kind in Australia.
Blasta Brewing was founded in 2015 by CEO Steve Russell and, winning numerous awards for its brews along the way, has grown into a collective encompassing a gastrobrewery, a beer hall with alfresco dining, a tap room, and the jewel in the crown – one of WA’s biggest beer production facilities with an annual production capacity of 15 million litres.
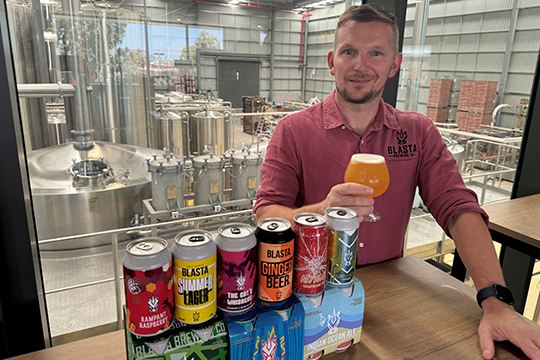
The company has just invested in a plant expansion, which includes the new filler, capable of handling a range of can sizes and able to produce over 15,000 cans per hour.
As part of this total brewery project, Blasta also purchased and installed a Steinecker/ Krones Combicube 50HL four-vessel brewhouse.
Integration with the BOTEC-F1 control system allows the team to have complete process control of the filler, as the packaging line has a single point of seamless control. The downstream packaging line is fully automated with cluster-to-case packing and a robotic palletising system, which complements the world class machinery purchased from Krones.
The equipment has been designed with specific engineering considerations for Blasta’s product range. This includes bespoke hot-side whirlpool controls and equipment, as well as brewhouse modifications. The 50HL system is capable of 11 turns per 24-hour period, significantly increasing Blasta’s production flexibility.
Selecting the best
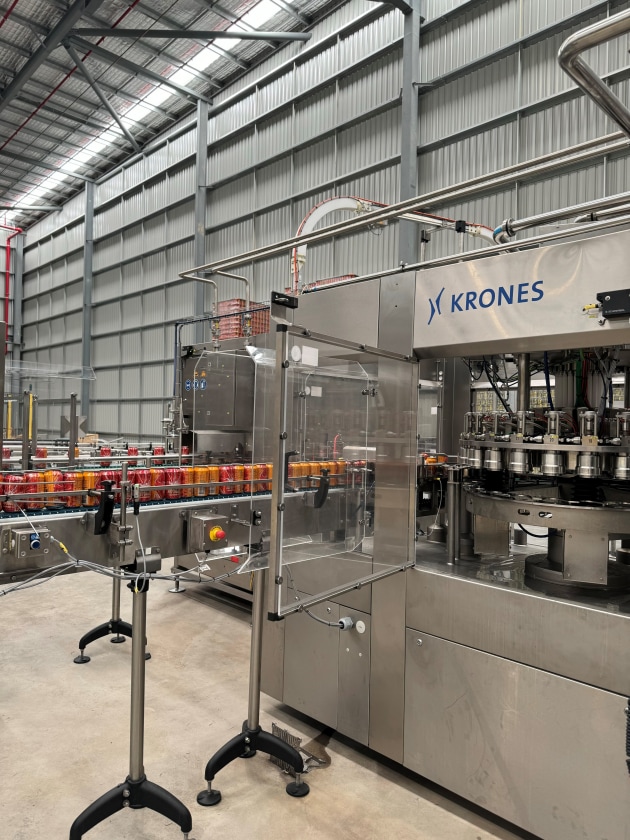
The deciding factor for Blasta when choosing this equipment was its proven track record of repeatability, quality and capability, specifically the quality controls in relation to maintaining critical DO (dissolved oxygen) and TPO (total packaged oxygen) at the lowest points possible.
Blasta explains that Steve Russell, who has an engineering background (he worked in oil and gas prior to venturing into the brewing industry) took the time to fully assess the machinery and components on offer and made the choice to partner with Krones for the project as it was “deemed the best in class for the business”. That, coupled with insights from others in the craft beer world who have purchased this machine, gave Blasta confidence that this was the right choice.
Krones Craftmate C filler incorporates the same technology as some of the larger machines used by industry worldwide, renowned for robustness and reliability. When it comes to the product being filled, the volumetric filler gives the assurance of accurate fill levels of beer products (and any other carbonated beverages). These can be produced in different can sizes and shapes with predictable outcomes. This, Blasta says, gives it confidence in its fills and also the efficiency and reduction of product waste.
Commenting on how this will benefit Blasta’s business, Steve Russell says, “With the filler being capable of speeds up to 15,000 cans per hour this allows us to grow our business exponentially and have the capacity to cater for third party packaging and brewing contracts. The team has realised a six per cent reduction in fill intolerances, which results in significant reduction of waste product and costs.”
Krones’ Steve Karavendzas adds, “With a combination of a Steinecker brewhouse and Krones craftmate can filler, Blasta is taking all the consistency that comes with industrial brewing scaled down to producing quality craft beer for years to come.”
Technical support
The installation process was undertaken by a team of specialists working for Blasta along with the experts from Krones. With the modular design of the filler, there was limited on-site major works which resulted in a speedy set out and install of main services, and allowed the team from Krones to supervise and guide the intricate coupling of the machine to the seamer, along with the supporting components such as the Checkmat fill-level inspection unit which utilises X-ray technology for can fill level assurance.
The process was not without its challenges. Blasta made an investment decision some six months prior to the Covid outbreak, and the resulting pandemic had a significant impact on the construction of Blasta’s new brewery facility in Perth, Western Australia. However, despite the global situation, Krones managed to deliver the machine on the agreed date as scheduled. The pandemic did, however, leave Blasta to overcome planned production commitments, which included the machine being installed and producing products.
Russell says, “We are really proud of the brewery we have built in Perth. This greenfields project is the largest and most capable world class facility that has been installed in WA in over 40 years. With a well-planned layout, upfront infrastructure and future proofing vision, we are capable of producing over 15.5 million litres of beer products from this site at a highly competitive price point.
“The investment allows us to compete in markets with historic barriers due to efficiency and agility.”
With the full gamut of a modern production facility, Blasta Brewing Co can now open doors to a wide variety of products including non-alcoholic, alcoholic and virtually any other beverage that can be packaged in a can.
Cheers to that.
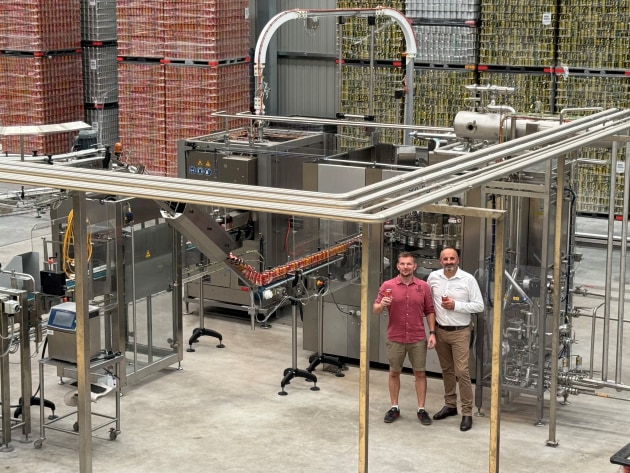