To mark Lantech’s 50th birthday this year, David Fullerton, sales director at Lantech talks history, new innovations, and where the company is now; and elaborates on its focus at AUSPACK to help visitors to the stand achieve their sustainability initiatives.
At AUSPACK, on Stand B045, Lantech will showcase both its case handling machine and wrapping machine and not only demonstrate the technology, but also show how the machines can intuitively help reduce damage that occurs in the supply chain.
Lantech came into existence in 1972, when US founder Pat Lancaster invented the first rotary stretch wrapping machine with his brother Bill. Years later, Pat pioneered the concept of pre-stretching the film – reducing film usage (and related costs) by half.
Since then, Lantech has been continuously improving its technology and has expanded globally. With the acquisition of the Rembrandt Company in 2001, the company also offers case and tray handling equipment, which has become a success story.
David Fullerton, who has been with the company for 15 years, has worked on Lantech technology for at least 30 years when he started working for Lantech distributor GrowMark in 1992, which was later procured by Amcor.
With a background in engineering, he initially took up the role of sales engineer at the company and sharpened his skillset by learning as much as he could about packaging, stretch film and Lantech machines.
“Back then, the Lantech machines were easy to replicate so we were able to manufacture them in Australia. We were quite proud of the fact that although it was a foreign brand, we were actually manufacturing locally,” he said.
Fullerton moved over to Lantech a few years after Amcor stopped manufacturing its machinery. Around that time, Lantech in the US was going through major changes, initiating a complete redesign of its equipment and most significantly, adopting Lean (or the Japanese term Kaizen) principles to improve its various processes.
The strategy of Lean, made popular by Toyota, helps increase efficiency, and sat well with Lantech’s founding principles “that anything and everything can be improved”. By receiving goods only as needed for the production process, inventory costs and wastage are reduced, while productivity and profit are increased.
“The Lean process has helped us produce at maximum capacity – we can produce one of our semi-automatic machines every 40 minutes if we need to,” explains Fullerton.
The 2001 purchase of the Rembrandt Company in Holland was an important landmark for Lantech. Fullerton reports that the uptake of the case and tray handling equipment was initially quite slow in Australia, but 10 years ago, with more focus on the case handling side of the business, started to explode, and has now become a success story.
“Fifteen years ago, our ratio would have been 90 per cent stretch/10 per cent case. And now it’s 50/50,” he says.
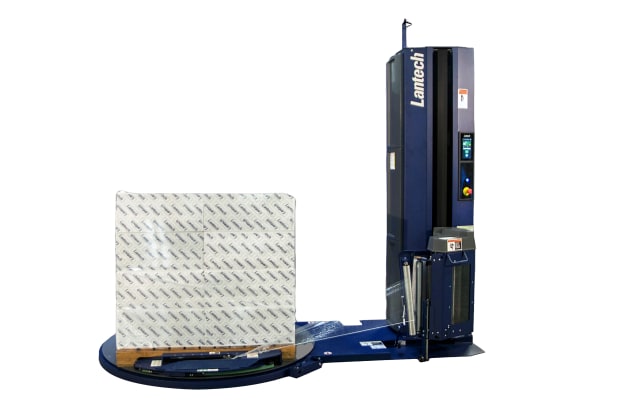
“We’ve been building machines for 50 years – we know how to make them easy to use and reliable, but we really want to engage with customers and support them in their initiatives to reduce waste,” said Fullerton, pointing out the company’s mission to dramatically reduce the billions of dollars of damage that happens in transit – making sure products are wrapped correctly and that they get from the factory floor to the retailer’s door in pristine condition.
Another sustainability initiative which the company is focusing on, is the reduction of plastic in its stretch film.
“We are continuously working to drive the amount of plastic stretch film downward,” he adds. “We work with the world-leading stretch wrap manufacturers, and they are starting to introduce recycled content. There’s even a company up in Scandinavia now that is pioneering stretch paper.”
Lantech has a huge global footprint but at its heart the company is still a small family-owned and operated business. One where everyone knows each other’s names and respects the value its staff provide to its customers – and for each other. This may be why many staff have worked at the company for a long time, as has Fullerton, and are proud to do so.
Pat Lancaster is in his eighties now and still heads up the innovation team. In the middle of his career, he stepped into a role in R&D to make way for his son Jim to take over the reins.
“There’s a kind of pride within the company, knowing that Pat pioneered the stretch film for the packaging industry,” says Fullerton. “Now, we want to continue to innovate.”