Amid the Covid-19 crisis, as government calls on industry to make products in short supply, manufacturers are turning to local packaging companies for help.
PKN spoke to Impact International, Wellman Packaging and Caps & Closures about their response to the crisis and the growing need for Australia’s self-sufficiency, especially when it comes to the supply of essential items for public safety.
Impact International
Local packaging suppliers are seeing a change in demand from the market as manufacturers who were dependent on overseas supply chains find themselves in a position they would prefer not to be in. So says Aleks Lajovic, managing director of Australian-owned tube and closure manufacturer Impact International.
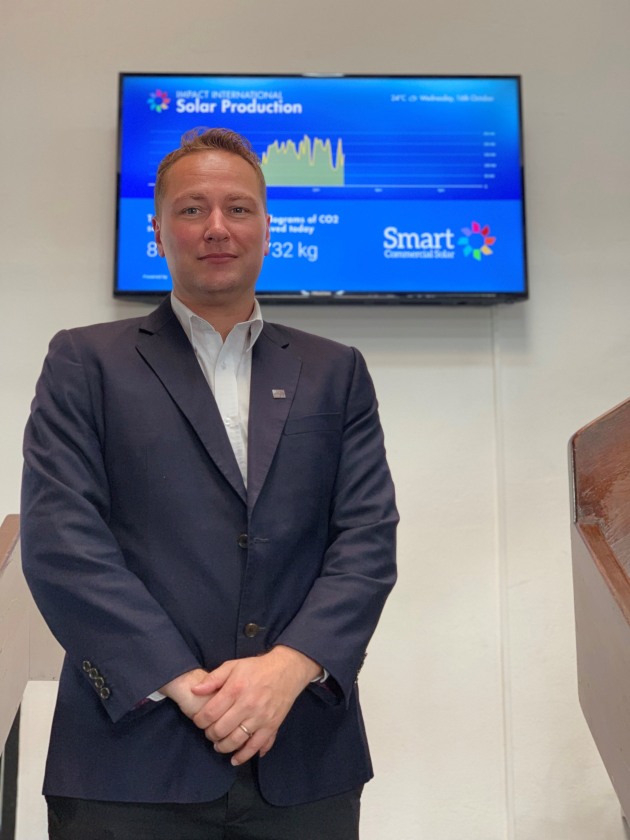
He tells PKN Impact is prioritising tube production for demand from existing, loyal customers as well as for items that the Australian Government views as “essential”, such as hand sanitiser.
“We have tried to offer customers tubes that maximise efficiencies on our production lines and we have tried to reduce the number of change-overs required on each production line,” he adds.
“Our staff and our suppliers have been fantastic, with everyone pitching in so that we can manufacture as many tubes for hand sanitiser products as possible. We are running extra shifts across our site as we try and assist as many people as possible."
Commenting on the reported packaging supply shortages for hand sanitiser (typically supplied in a plastic bottle with pump dispenser) Lajovic says, “When you think of a container, say a plastic bottle, there is not one company that I know of in Australia who covers off the three main areas of manufacturing the bottle; manufacturing and/or applying the cap or pump head; and decorating the bottle using either direct print or a label.
“Trying to manage these three areas in this current environment is extremely challenging. The pump supplier is probably based overseas, has huge orders and international freight is far from routine at the moment,” he adds.
“At Impact, we manufacture the tube, we manufacture the cap, we fit the cap onto the tube and then we decorate the tube, so all in-house and you get to deal with one company… plus, the tube understands how gravity works, so the product is already sitting at the dispensing orifice, you are not trying to get the product to flow ‘uphill’.
“We are also pricing in Australian dollars, so there is no exchange risk when dealing with us,” Lajovic says.
As Lajovic observes, a lot of companies are now reconsidering their packaging supply chains, the problem is that everyone is doing it at once. Consequently, the next challenge for Australian packaging manufacturers will be supply of raw materials (especially plastic resin). According to Lajovic, in the last week, two resin suppliers have moved to allocated supply of certain resins for the next few months.
Wellman Packaging
Sydney-based family owned company Wellman Packaging supplies rigid plastic packaging across a range of sectors but primarily food, household care, personal care and pharmaceutical, and therefore has a broad exposure to the types of products that have come under heavy demand due to the Covid-19 crisis.
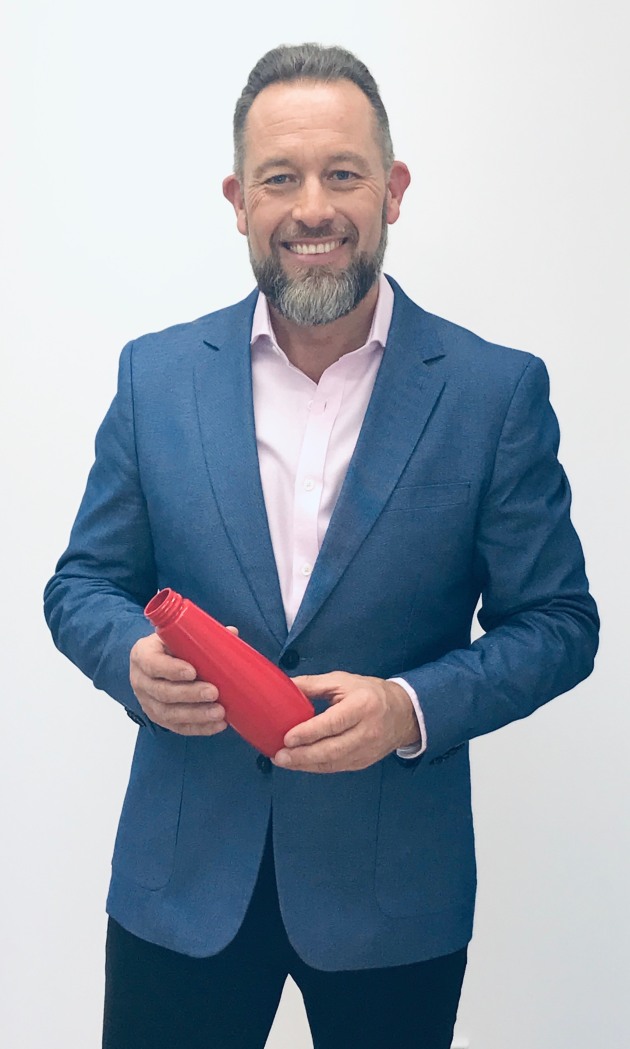
CEO Craig Wellman tells PKN that the bottles, closures and caps the company produces for these sectors, including domestic and commercial cleaning products – and hand sanitisers – have seen increased demand.
“The rapid elevation of the crisis and resulting panic buying by consumers together with a significant increase in the general levels of sanitisation throughout the community have driven this,” Wellman says.
“I expect this to continue long after the Covid-19 crisis has abated in strict medical terms because this pandemic has changed consumer and social behaviours that most likely be ‘locked-in’ as part of the ‘new normal’. This will translate into higher demand for products of this kind over coming years when compared to general average demand of say 2019,” he says.
Wellman says this is also the case for food with high volumes on products consumed in the home as a result of social distancing and work from home policies – and of course many restaurants closing or being restricted to take-away only.
“As demand normalises after the panic buying of recent weeks, demand in this sector should also continue at a generally uplifted level until the people return to public places like restaurants – and have the money to do so noting that we are heading for 10-15 per cent unemployment and possibly a deep and protracted economic contraction,” he adds.
Commenting on the packaging and product shortages around hand sanitiser, Wellman notes that aside from having put in place “hospital grade” procedures for combating infectious diseases so that the company may continue to supply packaging to other “essential businesses” for their cleaning chemicals and hand sanitisers in the fight against Covid-19, Wellman Packaging has also commenced its own production of hand sanitiser internally.
“For us it is a common supply item – we’ve had dispensers on the walls everywhere for years and something that we have been giving out to our staff and their families since the start of Covid-19. However, now our regular supplier, Johnson & Johnson Medical is struggling to keep up,” he says.
“So, we have now gone into the market and procured a long-term supply of the materials necessary to blend this including isopropyl alcohol, aloe vera and lavender oil. Our first batch will be around 1000 litres and is underway right now. Aside of internal use, we will be distributing this free of charge to our staff, their friends and families, suppliers, customers and other parties associated with Wellman Packaging – so that we help to keep them safe as well as widening the circle of protection around our operation to further insulate our supply line into other companies who are also mission critical in this battle,” Wellman says.
Wellman Packaging is also looking at the production of face masks in conjunction with the Victor Chang Research Institute.
“It’s game on and we all need to play a part in the control and management of this outbreak – including being respectful of social distancing rules. I very much doubt that this will be the last time we as a community need to rally against a contagion of this kind so developing the infrastructure and skills to deal with such events will certainly not be a wasted effort.
As Wellman says, if Covid-19 has taught us nothing else it is that excessive reliance on manufacturing from China and other parts of the world – of not being self-sufficient – is no longer an acceptable option, especially for items of an essential nature in terms of public safety.
Caps & Closures
Melbourne-based Caps & Closures continues to experience unprecedented demand for a wide range of closures and dispensing options, with staff working through Easter to fulfill requirements, as managing director Brendon Holmes tells PKN.
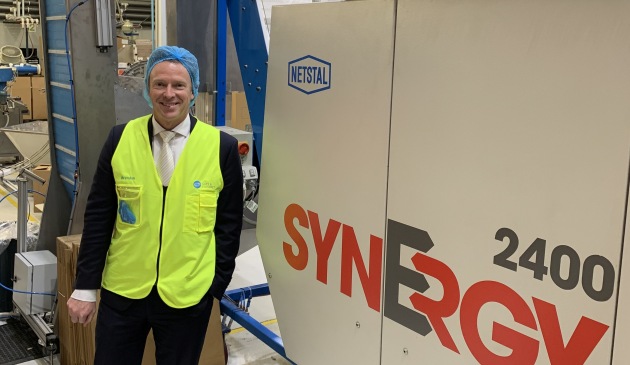
We continue to use every measure to cater for this unprecedented demand by increasing production, extending operating hours, employing additional staff and working around the clock to keep lead times to a minimum,” he says
He too cites the panic hoarding from the public as causing a significant shortage of essential products, like hand sanitiser and handwash.
Holmes says the company has put measures in place to increase production to meet the nation's essential packaging needs.
“Even with the global supply chain network in crisis, our experienced staff have done great work in managing the influx of emergency orders, production planning and fulfilment logistics.
“We are attracting new customers who are seeking an Australian manufacturer with credibility and a proven record, to fast-track supply of product to the consumer. We are innovating with existing caps and developing new designs to serve their needs. We have committed additional shifts for production round the clock, with careful planning, to support our customers both locally in Victoria as well as interstate to ensure the quick production of essential commodities by their manufacturers. That way, we can get it out to those who need them quickly,” Holmes says.
“Now is the time, as the Industry Minister Karen Andrews and NSW Premier Gladys Berejiklian recently pointed out, to learn from the pandemic experience that has exposed Australia's reliance on overseas supply chains, and support investment in retooling for products that should be manufactured domestically.”
Holmes relates that Caps & Closures has seen some "amazing outcomes" within its customer base, with local operations from breweries, distilleries, and bottlers converting lines to meet the ever-increasing demands of sanitiser and cleaning products.
One such customer is Urban Alley – a Melbourne-based independent craft brewery located at Docklands, now using its resources and facilities to produce hand sanitiser. Holmes tells PKN Caps & Closures was able to put measures in place promptly to adapt to the requirements of Urban Alley and at the same time save an estimated 100 jobs in the supply chain.
According to Holmes, the company is also developing a portfolio of PPE (personal protective equipment) products to serve a new Australian way of life and manufacturing industry that will demand availability of face-shields, masks and sanitising aids for example.
“The challenge going forward is to continue to support our new customers and expand our business together, in a highly competitive industry with many international competitors,” Holmes says.
Holmes and Lajovic concur with Wellman, who points out that one of the silver linings from Covid-19 will be a more robust manufacturing sector in Australia that after decades of neglect will once again become the engine room for innovation, economic growth and especially job creation.