In an Australian first, plastics food packaging manufacturer Genfac Plastics has become the inaugural Australian Packaging Covenant (APCO) signatory to gain approval to emboss the Australasian Recycling Label (ARL) logo on its take-away food packaging range.
Genfac says the inclusion of the ARL logo is a key step in driving its desire to see increasing quantities of polypropylene collected and recycled for retention in the productive economy. The logo, which will be prominently embossed on the side of the containers, starting with its popular regular G750 take-away container, will make it easy for consumers to understand recycling information and make the right choices at the point of disposal, the company says.
"It is so exciting to see Genfac’s continued industry leadership and commitment to the ARL Program. Ensuring consumers have clear, consistent and correct information to make the right choices when disposing of packaging is critical for effective behaviour change. It’s so pleasing to see APCO members continue to prioritise a circular approach to packaging and the inclusion of the first embossed ARL is a fantastic signifier of the importance of the program," said Chris Foley, CEO, APCO.
As an active member of the Australian Packaging Covenant Organisation (APCO), Genfac is invested in the broader industry’s vision to "collaborate to keep packaging materials out of landfill and retain the maximum value of the materials, energy and labour within the local economy". To deliver on this Genfac Plastics takes a life-cycle approach to embedding sustainability and effective stewardship into its everyday business.
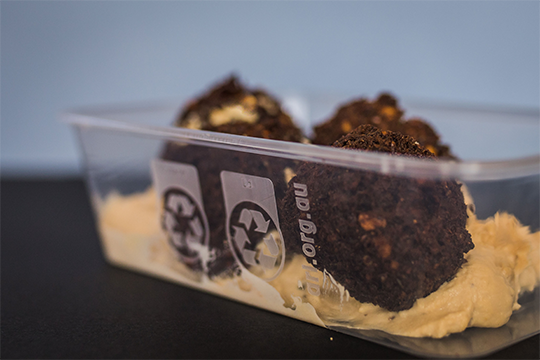
Cameron Tu, managing director at Genfac Plastics, said, “While we constantly strive to be the best and most reliable supplier of food packaging products that meet the needs of our customers, we are also constantly looking to demonstrate leadership. To that end, being a responsible corporate citizen that entrenches the philosophy of the triple bottom line is important to us and as a company we are investing heavily to meet the challenges of the future.
"Australia’s Waste Policy Action Plan sets a target of 80 per cent average recovery rate from all waste streams by 2030, and to significantly increase the use of recycled content in the products we produce."
"At Genfac we are very conscious of these national targets and the role we play to bring them to fruition. Our products are therefore made from a highly recyclable, food grade virgin grade polypropylene material which has a high post-consumer value if it is disposed of and recycled correctly," said Jan van de Graaff, sustainability and product stewardship advisor at Genfac.
"Post-consumer polypropylene containers are often being captured by recycling facilities already given its value as a source for recyclate material for the manufacture of new products including flower pots, furniture and other household items. Polypropylene as a material can be constantly recycled and fits in well to the circular economy approach."
Genfac has recently been working closely with its key supply chain partners Viva Energy and Martogg Plastics recyclers to investigate how it can further improve economic circularly and viably incorporate recovered polypropylene recyclate into its existing product range.
“Viva Energy Polymers was delighted to carry out the initial proof of concept for the embossed ARL logo at our market development laboratory. We are now excited to see Genfac launch the first application of this in the market which will deliver better recycling outcomes for these containers," said Robert Moran, product development and sustainability lead for Viva Energy Polymers.
Australian-owned Genfac Plastics is a manufacturer of plastics food packaging, including take-away food containers, and has been operating for 35 years and producing "safe, quality and fit-for-purpose food packaging products" at its production facility on the outskirts of Melbourne. This facility, which has one of the country’s largest privately owned roof-top solar farms, generates 1.2 megawatts of power and goes close to fulfilling all the company’s total energy needs.