Cutting edge sorting and processing technology forms the backbone of Martogg’s new Circular AU food-grade plastic recycling facility, on track to be up and running in Melbourne before year end.
As I sit down with Austen Ramage, Heath Boucher, and Ben McCullough to talk about this project, their enthusiasm and excitement is evident. The trio are part of the Martogg Group team bringing this first-of-its-kind development in Australian plastics recycling to fruition, and they’re keen to share the good news.
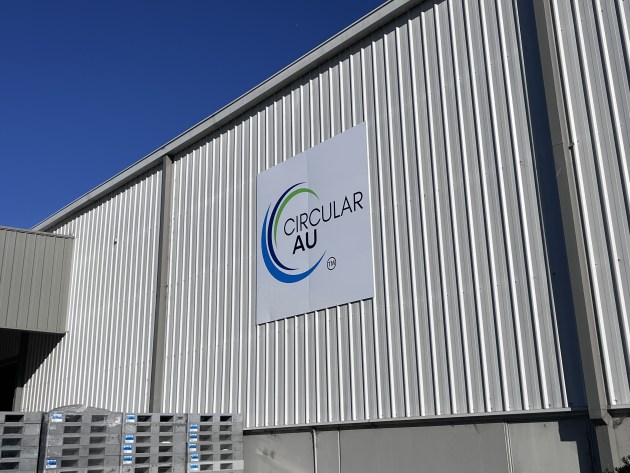
Plastics recycler Martogg, based in Dandenong South in Melbourne, produces high-grade recycled PET (rPET) under the marPET food-grade brand. When the company first entered the food-grade recycling market in 2016, the recycling sector was in flux, as players worked out how best to structure the industry including the feasibility of setting up their own sorting and washing facilities. While this development was underway, and Martogg established its local customer base for marPET, the company sourced its feedstock largely from the SE Asia region, as well as from some local suppliers.
As the ‘flakes settled’, it soon became clear that it was time to make a significant investment in advanced sorting and washing technology, and the Circular AU project was born.
“The Circular AU plant is the most sophisticated of its kind here in Australia,” says Austen Ramage, group manager Sustainability at Martogg LCM. “It enables us to close the loop on Australian waste, for Australian re-manufacturing applications.”
The emphasis is on Australian, Heath Boucher concurs. He is general manager of the Circular AU division. He says, “Transitioning to an Australian circular economy is critical, we have to be processing Australian waste for use in Australian packaging. This allows us to put our hand on our collective heart and say this is Australian sourced and made.”
“And that’s what Australian brands and consumers want,” says Ben McCulloch, product manager for marPET. “It strengthens Martogg’s position as the leading independent supplier of recycled resins for packaging. It’s a project that’s been a long time in development, and one we’re proud to bring to life.”
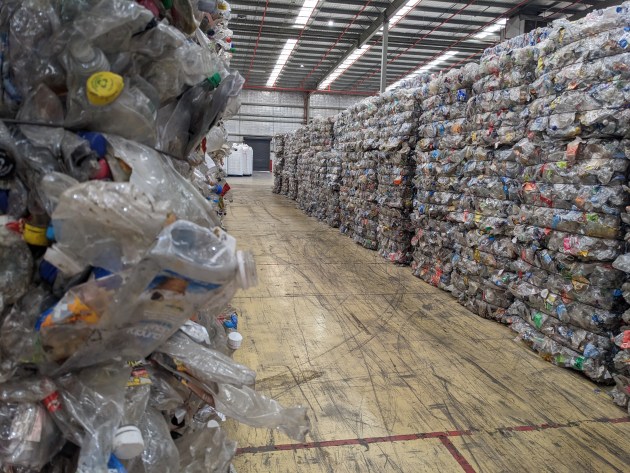
The Circular AU plant is currently in commissioning. Once operational, it will reprocess plastic packaging waste, with feedstock sourced from kerbside recycling and CDS streams, to produce food-grade recycled plastics for converting into food packaging.
In phase one of the development coming on stream later this year, the plant will have a 4000 tonnes per hour (40kt per annum) sorting capacity, and two tonnes per hour (20kt per annum) washing capacity.
“This equates to about a billion plastic bottles a year from the 40kt sorting,” Boucher says, noting that in the second phase of the project, washing will match sorting capacity, scaling up to two billion bottles a year.
The company has worked with European technology partners who have customised the equipment to Martogg’s requirements, delivering capability to identify and sort different post-consumer packaging materials, to ultimately produce pure 99.5 per cent pure plastic recycled flakes used to make marPET pellet and sheet, ready for converting into packaging.
“Technology like this does exist in Australia, but not to this level, which means we can accept a wider variety of plastic,” Boucher says.
The process involves magnetic, mechanical, and optical sorting, separating any metal and other non-plastic material from the stream and removing labels.
One of the most advanced parts of the sorting process engages AI technology, sourced from French company Pellenc, to identify the type and shape of the container. Selected bottles are channelled to the washer using air nodules.
The initial wash is friction-based, to remove any glass fragments that might have slipped through in the collected recycling load. The plastic is then ground into flakes before being submitted to two stages of hot, caustic washing (85 degrees, pH 12). The latter phase sees the removal of any adhesives or other impurities.
Drying is the next step, after which the flakes are rinsed with fresh water to remove and process residue. And finally, the clean flakes are de-dusted and passed through the optical sorter again, yielding a guaranteed 99.5% food-grade quality plastic.
Apart from the advanced technology involved, this marks a major investment by a local recycler, and it’s certainly Martogg’s single biggest investment to date. The plant has been developed with support from the Victorian Circular Economy Recycling Modernisation Fund. This fund supports projects that improve the quality and quantity of recyclable materials in Victoria by upgrading infrastructure, technology, or processing capacity.
Ramage, Boucher and McCulloch are looking forward to the plant opening next year, and to seeing the full impact of the investment and the contribution it will make to Australia’s circular economy.
They concur: “The business is already passionate about recycling in general, but it’s exciting for us to be recycling Australian waste and creating products for Australia.”
Developing an Australian circular economy will require buy-in and contribution from all brand owners, and all parts of the supply chain. Martogg Group is demonstrating leadership through this investment at a critical juncture for the Australian packaging industry. With the recent landmark decision by government to regulate packaging recycling and mandate the use of recycled content in manufacturing, the timing of Circular AU coming on stream could not be better.