Opal Group has opened its doors for Australian Institute of Packaging (AIP) members via a virtual site tour of its facilities, giving insights into its recycling operation, its Botany Mill, its fibre and specialty packaging divisions, and its bag solutions.
This year, Opal will collect around 600,000 tonnes of cardboard from its customers around Australia, and around 500,000 tonnes of that will be recycled on its B9 paper-making machine at its Botany Mill.
Due to only needing a certain amount of cardboard to make its paper, any excess Opal collects from its customers around the country will be exported.
“The different types of businesses that opal deals with, first, a big portion of that being the big retailers such as Woolworths, K Mart, Target, Aldi, and others – they are more than just customers, we see them as partners. They have a lot of cardboard that we have a need for, and they have a need to recycle it, which we can deliver,” explained Daniel McHugh, national sales manager at Opal Recycling.
“We also deal with waste management organisations, who obviously have a promise to their customers to recycle domestically, and we have the infrastructure to do that, so we take a portion from these companies.
“And we also have the brand – the customers that we are selling our packaging to. They recycle material on their sites, and we also bring some of that back to our mill as well.”
The Botany Mill is a 100 per cent recycled paper mill, and this year, Opal is expecting to make around 430,000 tonnes of paper.
In terms of what’s collected for use, Jacob Chretien, general manager of Technical & Strategic Projects at Opal Paper Division, explained that unfortunately, along with the cardboard, some plastic and glass and other unwanted waste will unintentionally get collected.
To counter this and to remove all the waste that isn’t fibre, Opal puts the recovered materials into a pulper, where water is added to make a slurry. After that, Opal has a number of unit operations through the process that pulls out the non-fibre materials – starting with the big bits, then working its way down to the very fine bits like sand or printing ink.
“The goal is that we remove all of those materials to prepare for the paper machine, but the fantastic bit is because the paper machine needs good quality furnish to perform well, the quality of the paper we make for our customers is exceptional,” said Chretien.
“We do need to consider all of the different products that we can make, and so, as a result, when the B9 was built, it needed flexibility to be able to make this wide product offering.
According to Chretien, there’s a whole area of opportunity around resource recovery and closing the loop in the market
“It is not just about being a paper manufacturer, but also being an integrated recycler – we make paper, we make boxes, we recover boxes after they’ve been used to come back into the process and go around again,” Chretien added.
Opal Fibre has 11 manufacturing facilities in its network – eight in Australia and three in New Zealand. All sites in Opal’s network source paper from its 100 per cent recycled Botany and Maryvale mills.
The company has a 2800mm-wide BHS corrugator that has the capability of running to 400 lineal metres per minute. Opal has several converting machines, variations of RSCs, flexo folder gluers, and rotary die-cutters.
Brad Hinds, group general manager at Opal Fibre Packaging ANZ, said that Opal also has a unique capability thanks to its Zytech machines, which are both held in Queensland.
“Opal has a strong focus on paper innovation, which allows the company to provide market solutions to varying customers with varying packaging needs,” Hinds explained.
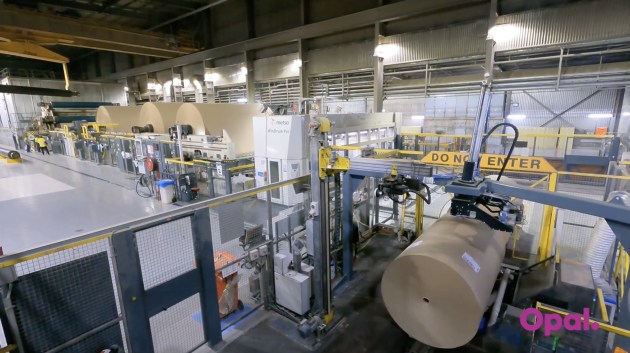
“Rather than following a conventional corrugated medium, our mediums in our Zytech machine allows us to have tip-to-tip corrugating, which provides additional strength that allows us to use less fibre in our packaging.”
As for transportation, because it is quite hard to transfer the initial 50-tonne (about 50km of paper) product created, Opal cuts it down into customer rolls through its winder, which range from 600mm wide, all the way to 2.8m wide.
That paper then goes into Opal’s finished product store for dispatching to its customers in Australia, North America and Asia.