Pernod Ricard Winemakers’ new high-speed combination can and small format bottle line, the fastest of its kind in the southern hemisphere, is up and running, catering to growing demand in the RTD sector.
The new line, with a processing capacity of up to 24,000 cans per hour, is set up at Pernod Ricard’s Rowland Flat site in South Australia. The line delivers efficient canning and bottling capabilities that will enable Pernod Ricard to produce its Ready-to-Drink (RTD) range in-house for the Pacific market, as well as supporting its small format still and sparkling wine ranges.
The RTD market is booming, and Pernod Ricard says it anticipates that RTD volumes will represent more than 20 per cent of the total Australian production volume by 2026.
More than 100 different products will be filled and packed on this line, including Jameson Cola and Jameson Sodas (375ml); Absolut cocktails (250ml); Malibu cocktails (250ml); Malfy Gin & Tonic (300ml); Altos Margarita (330ml); and Jacob’s Creek Still and Sparkling (200ml).
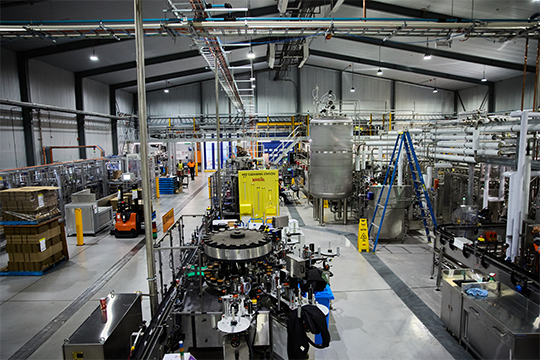
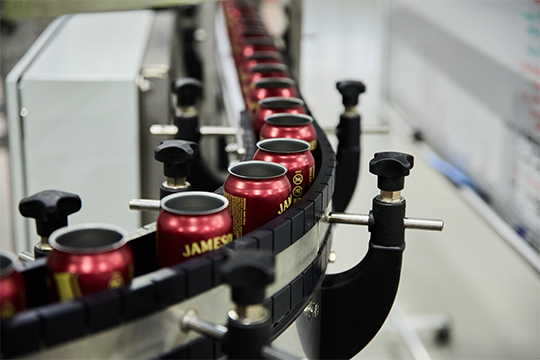
Pernod Ricard previously outsourced RTD production to three co-packers based within Australia, supplying for the Australia and New Zealand markets.
Robert Taddeo, operations director – Australia Operations, told PKN, “Due to the growing RTD category and Pernod Ricard’s RTD portfolio growth, we reached a point where the scale of production would benefit from in-house capacity. This enables us to have greater control of the supply chain, including service, quality, cost, flexibility, agility, and smaller minimum order quantities (MOQs).”
“Bringing production in-house gives us the flexibility and speed we need to meet the evolving requirements of the RTD category, improving cost competitiveness, and enhancing our existing operations across Australia and New Zealand. It is an exciting step forward for Pernod Ricard Winemakers, the AsiaPacific region, and Pernod Ricard’s RTD ambitions,” said Brett McKinnon, chief operating officer, Pernod Ricard Winemakers.
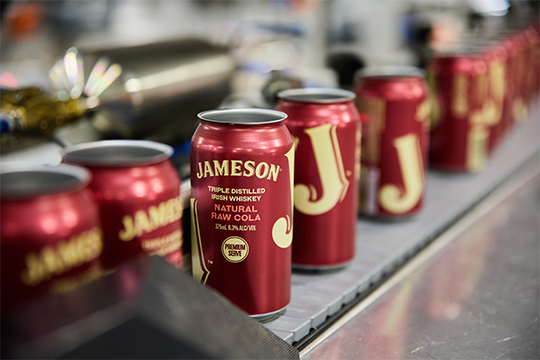
Asked why speed on the line was so important, Taddeo responded: “The demand for RTDs reached a scale that meant we needed to ensure productivity would be a key factor in the design of the line, and that we could align capability with our shift requirements, as well as looking toward future growth opportunities.”
On the line's flexibility, Taddeo said, “It allows us to be agile with scheduling and MOQs, which is particularly important when factoring in forecasting, sales variability, and new product development. We also wanted to ensure the new line would be efficient, meaning we could meet the demands of the market and changing trends.
PKN first reported on this pending installation back in 2021, but the ongoing repercussions of the Covid-19 pandemic, which resulted in factory shutdowns, labour shortages and shipping delays, ultimately impacted the project’s timeline. The company commenced installation of the line in April this year, with the first product commissioned in early June.
SUPPLY PARTNERS
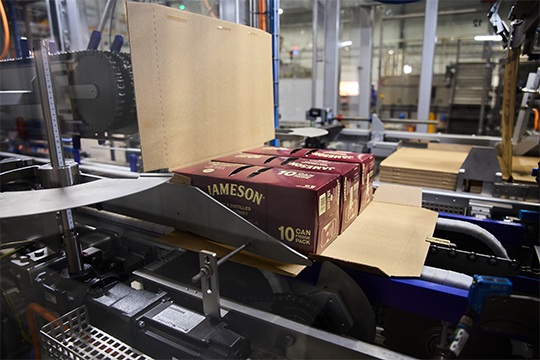
Foodmach was involved in the turnkey project delivery, which includes Foodmach palletising and depalletising equipment; a GEA Vipoll All-In-One Filler; Petek tunnel pasteurising with an advanced water saving system; can and bottle drying; an extensive range of inspection equipment including empty and full container inspection, X-ray, and fill height; Markem-Imaje laser and inkjet coding and print and apply labelling with compliance software; Meypack wraparound case packer; Robopac stretch wrapping; and Ambaflex portal and spirals, with Foodmach conveying and safety systems as well as line control.
Outside of the Foodmach contract, GEA supplied the liquid processing system comprising the GEA Visitron, an all-in-one rinser/filler block with crown seal, screw cap and 200/202 can seamer; and liquid delivery and CIP (clean in place), including inline carbonator, flash pasteuriser and Blue H2O Filtration system.
Paker supplied the cluster packer for multipack formats.
SUSTAINABILITY INITITIATIVES
Related to this project, Pernod Ricard incorporated a closed loop steam condensate return for its new boiler, waste-water recovery and treatment on the tunnel pasteuriser, and ‘lights out’ CIP (clean in place), prior to the weekly start up, to reduce our overall impacts during development and operation of the new line.
“Outside of this development, Pernod Ricard Winemakers is constantly working on sustainability initiatives linked to our Sustainability and Responsibility Roadmap, Good Times from a Good Place,” Taddeo says.
“For packaging, some of these include lightweighting our bottles and increasing recycled glass content, moving to Kraft board for the majority of our product ranges; moving to wet strength recyclable jacket wraps; and transitioning to hoodless sparkling for a select range within our portfolio.”
In other steps, Pernod Ricard has rolled out irrigation management software for its own vineyards, and is converting forklift fleet from gas to electric.
FUNDING
The project was supported by a $1.2million grant from the South Australian Department of Primary Industries and Regions, through their $15 million strategy for regional growth. The funds were announced by the South Australian Government in 2020 to help fast track the recovery of regional economies after COVID-19 restrictions, with a focus on projects that could demonstrate greater private-to-government funding ratios and strong economic outcomes.
Brett McKinnon said, “We sincerely thank the South Australian Government for supporting our investment in the RTD category with the development of our new combination line, and in turn their commitment to regional growth in South Australia.”