Zipform Packaging has opened its new $8m manufacturing facility in Dandenong, Victoria, for linear formed composite packaging, doubling the company's production capacity and expanding its footprint on its Western Australian base. The opening ceremony was attended by customers, suppliers and key industry stakeholders. PKN was there.
Addressing guests, managing director John Bigley said that this showcase plant was the product of the hard work and collaboration of many stakeholders, and he thanked everyone who had played a part.
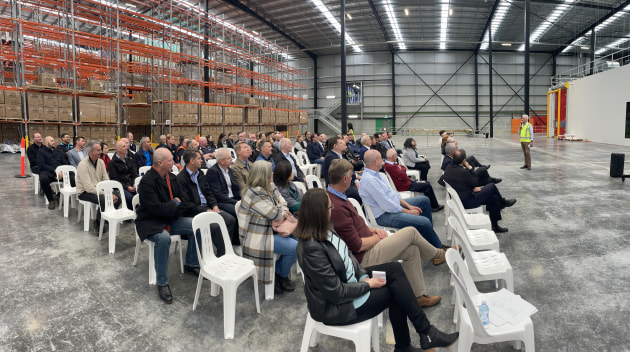
Two years in development, the new 10,600m2 facility, comprises a manufacturing zone and a 1000m2 cleanroom. The adjacent warehousing space is operated by Zipform’s 3PL partner CRL Express. The manufacturing line incorporates the latest linear forming technology for composite packs.
In conjunction with capacity at the Perth facility, the new line will enable Zipform to deliver over 40 million packs per annum in the first phase. Bigley told PKN potential future expansion would take capacity to 100 million packs.
Zipform’s linear forming technology is the first of its kind in the Australian and this second line installed in Melbourne, and one of only three in the world producing linear formed composite packs for food packaging.
“We can honestly say we are leaders in this technology in the region,” Bigley said. “We have been operating the forming technology for over ten years and the paper-bottom technology for over seven years. It’s satisfying to see the likes of Kellogg’s Pringles finally moving away from a metal end to a paper bottom in Europe, but we have been able to deliver this format here for some time.”
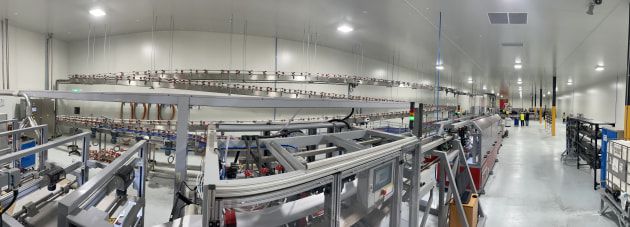
The linear forming technology hails from France, and Bigley explains that the material structure Zipform uses has around 92 per cent fibre and has passed the Pulpability Protocols as set out by APCO with “excellent fibre recovery outcomes”. The pack by weight contains over 60 per cent post consumer recycled content.
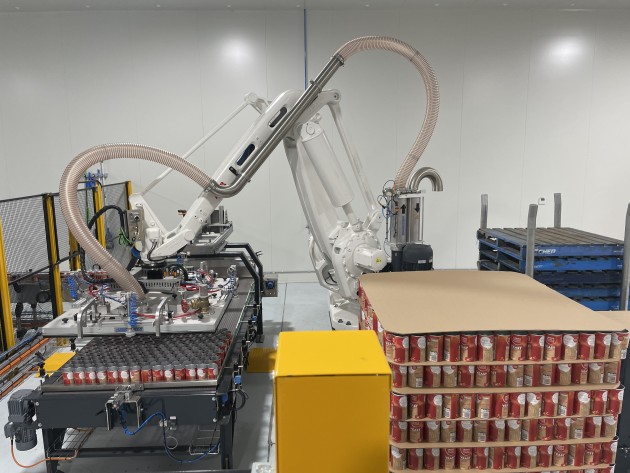
The line itself has a few more “bells and whistles” on versus the Perth line, Bigley explained, with in-line print inspection and higher ultrasonic welding speed capability. The back end of the line is fully automated, and incorporates an air rinser and in-line vision system ahead of the robotic palletiser.
The facility has integrated manufacturing and warehouse systems, enabling a finished pallet of packs to leave the cleanroom strapped, wrapped, and labelled. Pallets are picked up by CRL, scanned and placed into the warehouse or straight onto trucks. This means that Zipform only require two people per shift to operate the facility.
“Aside from the manufacturing and cleanroom areas, there’s a new office area where Zipform can welcome stakeholders to the plant and showcase the technology in a world class environment,” Bigley said.
Zipform now has installed capacity to meet the ever-growing demand for packaging that meets the 2025 National Packaging Targets in terms of recyclability and recycled content.
“As was the case for out Perth facility, the Melbourne plant will be assessed against the BRCGS packaging standard and should achieve AA status as Perth has,” Bigley said. “The facility is a showcase for the technology and customers can be assured that Zipform will continue to invest to fuel our growth plans.”
Asked about next steps for the company, Bigley said, “This is only Phase One for Melbourne and the layout we have designed will allow a speed expansion in Phase Two, with a possible second line in Phase Three.
“We have future-proofed the facility with regards to space and power supply. We are ambitious to grow our footprint regionally and globally, and the design of this line and cleanroom can be used for future facilities.
“Melbourne will really be a showcase and we are excited to see what it delivers.”