Foodmach, sponsor of the newly released Top 100 Food & Drink Companies 2024 report, published by Food & Drink Business with data from IBISWorld, shares four examples of how its latest palletising technology is transforming FMCG businesses.
In an era of rising costs and heightened consumer demands, FMCG manufacturers face a daunting challenge: how to produce more, faster, and with fewer resources.
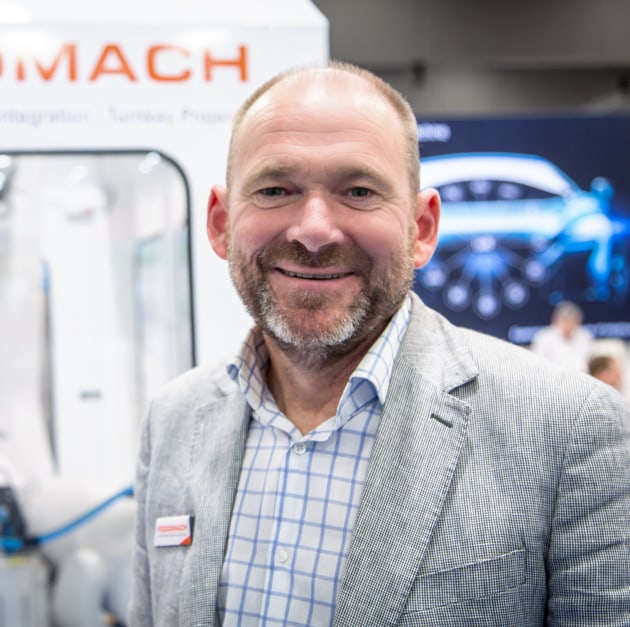
"With manufacturers feeling the pressure to find operational efficiencies more than ever, it is worth noting that inefficient production line bottlenecks – often caused by outdated palletising systems – account for 20-30 per cent of annual productivity losses," says Phil Biggs, Foodmach strategy and sales director.
The good news? Modern palletising solutions can quickly resolve these inefficiencies and improve Overall Equipment Effectiveness (OEE), delivering measurable ROI within months.
Escalating delays
One of our a mid-sized food manufacturing customers was facing escalating delays due to manual palletising. Its operators were also struggling to manage heavier cases efficiently, resulting in workplace injuries, costly overtime, and recurring production bottlenecks.
For its needs, the all-in-one Instant Robot Palletiser i35 offered the best solution. Designed for ease and efficiency, its key features include:
- High payload capacity: Able to handle cases up to 34 kilogram at 12 cycles per minute, or 24 cases for 17 kilogram cases.
- Advanced software: Multi-variable case pick-up software enables the robotic arm to select one or two cases at a time, optimising pallet layer patterns dynamically.
- Plug-and-play design: Operators set up the system in under five minutes with no technical expertise required.
- Continuous operation: Dual-pallet configuration ensures uninterrupted production as pallets are swapped out.
Six months after the system was implemented, the manufacturer saw a 25 per cent increase in productivity and 40 per cent reduction in manual labour costs. Within 10 months it had achieved ROI.
The company also saw the benefits for its team, with improved employee job satisfaction due to reduced injury rates and risk, and stress, thanks to a production line that now operates seamlessly during peak demand periods.
Space restrictions, waste concerns
A beverage manufacturer approached Foodmach looking for a compact solution to palletise and stretch-wrap products while addressing inefficiencies in film usage and handling fragile items like glass bottles.
The compact design of the space-saving Robopac Palwrapp system meant it fitted seamlessly into the factory’s existing layout and its advanced features made it the obvious choice.
- Integrated palletising and wrapping: No need for separate equipment, saving valuable factory floor space.
- Cube Technology: Optimised film usage reduces stretch film costs by up to 55 per cent with variable pre-stretch and containment force settings.
- High-speed operation: Handles up to 50 cases per minute with a capacity for up to three layers per minute and layer weights of up to 350 kilograms.
- Gentle product handling: Ensures the safety of fragile products through precise placement and wrapping mechanisms.
- Within three months, the company reduced packaging costs by 30 per cent, freeing up factory space for a new production line. The system maintains consistent pallet quality and operators appreciate the intuitive controls.
Labour intensive, error prone
Source: Foodmach
A SME FMCG manufacturer came to us, struggling with manual palletising because its equipment lacked flexibility, was slow, error-prone, and labour-intensive. The company was managing diverse product SKUs and seasonal demand spikes, adding additional strain and productivity losses at critical times. We looked to the Instant Cobot Palletiser, a lightweight, plug and play mobile system. Key features include:
- Quick deployment: Fully portable and ready to operate with just 240V power and air.
- High capacity: Handles cases up to 28 kilograms, or two 14 kilogram cases simultaneously.
- User-friendly interface: The 13-inch touchscreen wizard allows operators without technical skills to input product dimensions and pallet patterns.
- Safety-first design: Integrated zone scanners ensure safe operation at speeds above five cases per minute.
- Dynamic adaptability: Smart software automatically adjusts for barcode placement and optimised pallet stability with interlocking patterns.
Multiple SKU inefficiencies
Australian margarine and spreads manufacturer, Nuttelex, was experiencing inefficiencies due to its existing palletising system‘s inability to handle multiple SKUs concurrently, resulting in frequent stoppages for manual changeovers, increased labour costs, and reduced OEE.
Foodmach’s Robomatrix Multi-SKU Palletiser became the preferred solution by enabling the simultaneous palletisation of multiple products and formats at high speeds.
Its key features include:
- High-Speed Multi-Line Handling: Capable of palletising multiple products to multiple locations simultaneously, effectively managing diverse packaging styles, shapes, and sizes.
- Advanced Pattern Programming: Proprietary Robowizard software with a user-friendly drag-and-drop interface allows operators to create and modify pallet patterns for rapid changeovers, without needing specialised technical skills.
- Modular Design: Palletisers can be added, sharing the same inbound and outbound pallet handling, thereby providing scalability for growth.
Nuttelex reported reduced changeover downtime, leading to a boost in production efficiency. The automation of its palletising process meant it was less reliant on manual labour, reducing its labour costs. And the system’s flexibility allowed Nuttelex to respond swiftly to market demands without major operational disruptions.
By adopting the Robomatrix Multi-SKU Palletiser, Nuttelex overcame existing operational challenges and positioned itself for scalable growth in a dynamic market.
Think palletiser, think Foodmach
Source: Foodmach
Foodmach understands that CAPEX can be a barrier, which is why the company offers Lease2Buy. It allows customers to spread costs over two to five years with low interest rates and no capital investment required.
This flexible payment plan enables access to the latest palletising technology and ROI before payments are complete.
Lease2Buy can be structured as a chattel mortgage, rental, or finance lease, providing a straightforward plan with no balloon payment that allows customers to upgrade production capabilities without depleting capital reserves.
This approach enables investment in advanced equipment – such as palletisers, conveyors, and stretch wrappers – while preserving working capital for other strategic initiatives.
Additionally, depending on the chosen financing structure, Lease2Buy offers potential tax and accounting benefits.
By converting capital expenses into manageable operating expenses, positive cash flow is achievable from day one, making it a smart investment in any company’s future.
It’s fast to set up and can improve cash flow immediately.
From low- to high-speed, mechanical to robotic, Foodmach has a palletising solution for every application. Its systems are intuitive, efficient, and designed to maximise OEE and ROI. Manufacturers can also think beyond palletisers to an end-to-end range of packaging technology from the world’s top suppliers, all of which come with Foodmach’s 50-plus years of OEE expertise.
This article first appeared in the December/January 2025 edition of Food & Drink Business magazine.