Ranpak, a global leader of sustainable paper-based packaging solutions for e-commerce and industrial supply chains, which will be exhibiting on the APPMA Processing & Packaging Pavilion at Industrial Transformation 2025, has introduced three new products, which bring automation and protective paper technology together into integrated solutions.
The comprehensive line of packaging solutions empowers packers to achieve greater productivity, quality, consistency and sustainability, while also improving labour efficiency and ergonomics within packing operations.
Ranpak says these three solutions "represent a synthesis of sustainable packaging expertise built on over 50 years of experience in paper packaging solutions with a dedicated focus on cutting-edge technology and pack station development".
Complementing the development of automation solutions with the sustainability, recycling potential, and renewability of paper materials allows businesses to scale their operations with an eye towards their current sustainability performance and regulatory changes.
Each of these solutions, Ranpak says, also contributes to a more ergonomic workplace within the packaging line, automating some of the most repetitive tasks while allowing employees to focus on more complex and strategic operations.
First up, the PadPak Multi-Station, which combines the best elements of automation and sustainable paper packaging by automatically delivering cushioning pads with exceptional efficiency to the packer, eliminating multiple converters and improving ergonomics.
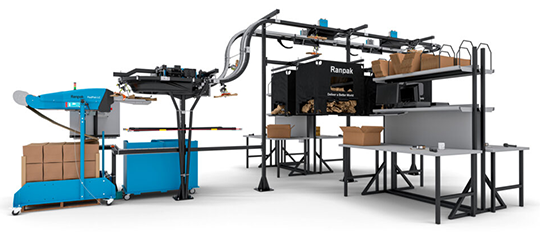
An automated line allows a single central PadPak paper converter to supply 100 per cent recyclable, biodegradable, and renewable paper pads to up to 10 packing stations continuously.
The modular and highly customisable solution saves space and boosts productivity by delivering pads directly to the packer, eliminating the need for a separate converter at each packing station.
The modularity of the solution enables layouts that adapt to specific packing needs, easily integrating into spaces with unique dimensions.
Next up, the DecisionTower with FillPak Trident, which uses machine vision capabilities to measure voids and dispense the perfect amount of fully kerbside recyclable paper void fill material through a connected converter.
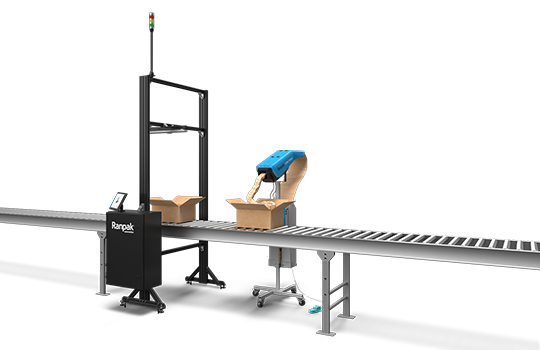
By combining sophisticated vision technology with sustainable paper packaging materials, the packaging process becomes less wasteful, more consistent, and provides a better customer experience during unboxing.
Up to 35 per cent paper reduction is possible due to the combination of active void measurement and the use of the unique triangle-shaped paper pads dispensed by the FillPak Trident converter, which are engineered to fill space with the minimum required amount of paper materials.
The solution automatically adjusts to different box types and void volumes, making it easy to use with limited-to-no operator training.
End customers can simply recycle the paper packaging materials they receive without seeing too much or too little protecting their products, increasing satisfaction.
And finally, the Pad’it! solution, which automatically inserts a unique, waved paper cushioning pad at the bottom, top, or both top and bottom of a package, providing an additional layer of protection in the box.

This fully automated system creates, picks, and places pads, reducing manual labour and requires minimal training to enhance operational productivity.
The system can add additional padding to up to 15 boxes per minute, keeping pace with other automation solutions on a line.
It also ensures precise pad placement for a uniform, visually appealing package by using a robotic arm and the WrapPak Protector converter, improving both in-the-box protection and the unboxing experience.