To ensure pneumatic systems operate efficiently, regular maintenance of fittings and tubing is vital. These components are key to managing the flow of compressed air in industrial automation systems. According to Robert Taylor, SMC Corporation's national product specialist, routine inspections and timely replacements can help avert failures and enhance system performance.
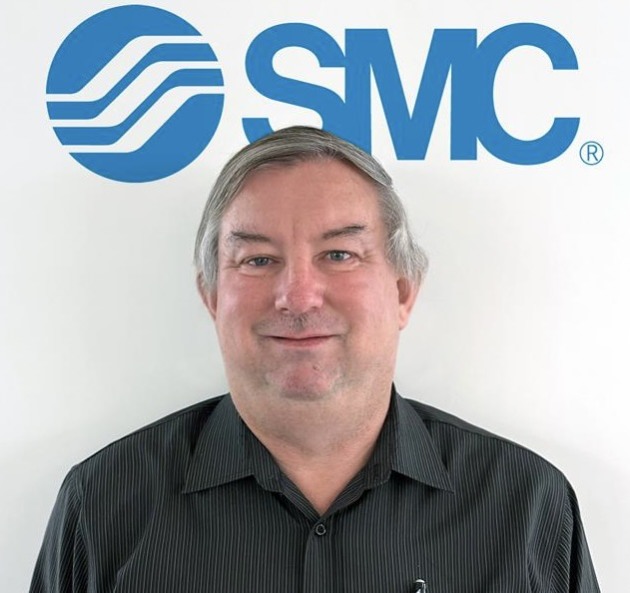
Taylor outlines key factors influencing tubing lifespan, including material type, operating conditions, and environmental exposure. “Polyurethane tubing should typically be replaced every three to seven years, depending on wear and environment, while nylon tubing lasts between five and ten years,” he says. Cracking, brittleness, leaks, reduced airflow, loss of flexibility, swelling, deformation, and discolouration are common indicators that replacement is needed. He advises businesses to allocate resources for annual inspections to maintain optimal airflow.
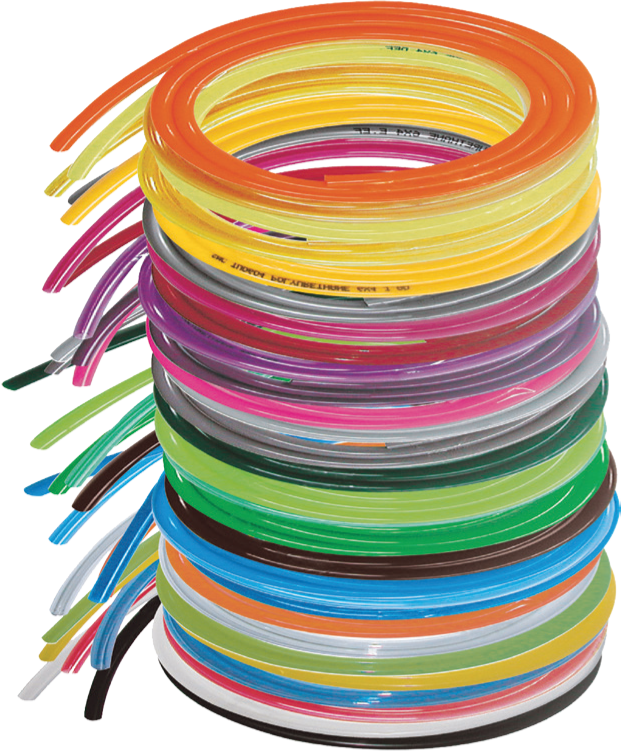
Fittings, unlike tubing, do not have a set lifespan but are influenced by usage frequency, tube condition, and environmental factors. As Taylor notes, “Typically, they should be replaced every five to ten years unless operating in high-stress environments, which may require more frequent replacements.”
SMC offers a range of fittings, including one-touch options in stainless steel, metal, and plastic, as well as insert fittings, miniature fittings, fluoropolymer hyper fittings, and quick couplers. The company also provides tubing solutions in soft nylon, nylon, polyurethane, polyethylene, and PFA, catering to various industrial environments.
Taylor stresses the importance of addressing these overlooked aspects to minimise downtime, “Getting the basics right is essential for ensuring efficient operations. Businesses should focus on overlooked areas of their factories to prevent costly downtime.”