Pack Expo returned to Chicago on 23-26 October after a four-year hiatus and it was bigger and better than ever. Over 44,000 visitors had the chance to see more than 2000 exhibits. Packaging journalist John Henry walked the halls for PKN and dropped by the stands of some APPMA members.
The show opened its doors with the industry ready to do business after years of consistent growth, according to show owner and producer PMMI, The Association for Packaging and Processing Technologies.
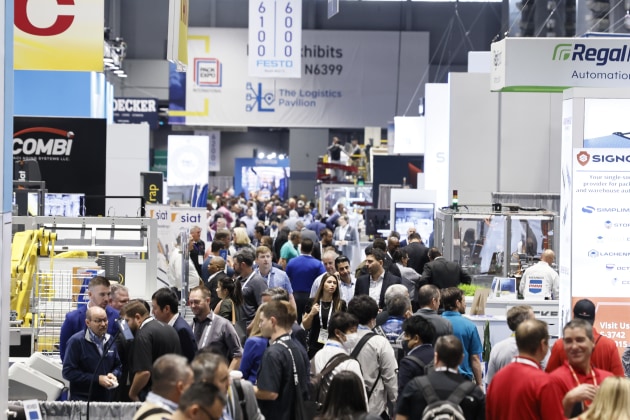
“The success of Pack Expo is a testament to our industry’s continued growth as well as PMMI’s commitment to bringing the industry together to share cutting-edge innovations,” says Jim Pittas, president and CEO, PMMI. “No other event this year showcased so many end-to-end solutions, offering attendees everything they need to compete in a changing marketplace.”
Industry growth translated into buyers coming in significant numbers, ready to see the latest packaging materials as well as technology in action.
Improving operations, reaching sustainability goals, and checking out new innovations are just a few of the drivers that brought consumer packaged goods and life sciences companies to Pack Expo International. The buzz on the show floor confirmed that exhibitors and attendees from companies of all sizes found a rewarding, and some claim unparalleled, experience at the four-day event.
Heat and Control
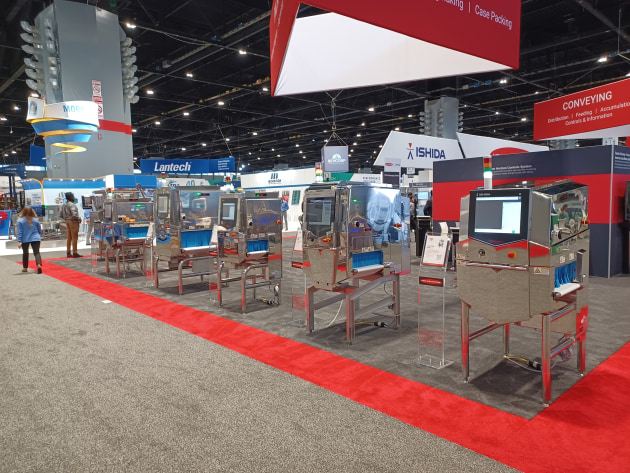
Heat and Control, with manufacturing facilities in Brisbane, showed their line of food processing and packaging equipment. Pride of place went to its new continuous air fryer. Heat and Control’s air fryer allows cooking of products from chicken nuggets to egg rolls replicating the texture of traditional submerged oil frying without all the oil – enabling the manufacture a much healthier product, the company says.
Heat and Control has been a long-time partner with Ishida. Along with food processing equipment, it showed Ishida’s complete line of inspection equipment including X-ray, check-weighing and metal detection. Also on display were the latest in combining scales and vertical form-fill-seal baggers.
Tronics
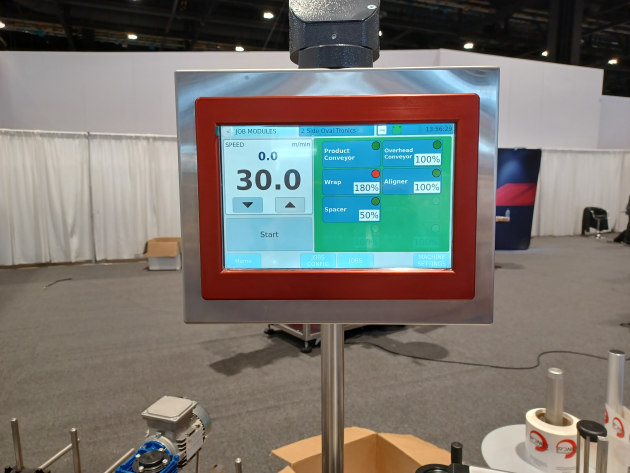
Sydney-based Tronics (part of Aldus Tronics) showed off its line of label applicating machines. Machines on display included several fully integrated labellers, a low-cost but high-performance wrap labeller and a stand-alone side or top labeller. The Model S4 labeler (pictured) has the capability to apply front and back panel labels or wraparound labels at speeds up to 150ppm.
Tronics has long been known for ease of making electronic adjustments on-the-fly. Now the company has taken it a step further with its touchscreen HMI. Once a product/label combination has been determined for the first time, settings are stored in the HMI. The next time the product is run, a simple touch re-establishes the settings. This saves time in setup and mistake-proofs the setup.
tna solutions
Another Australian manufacturer, tna solutions, is known worldwide for its food processing and packaging systems. It supplies and integrates complete lines from initial processing and cooking to final packaging, making it a single-source provider.
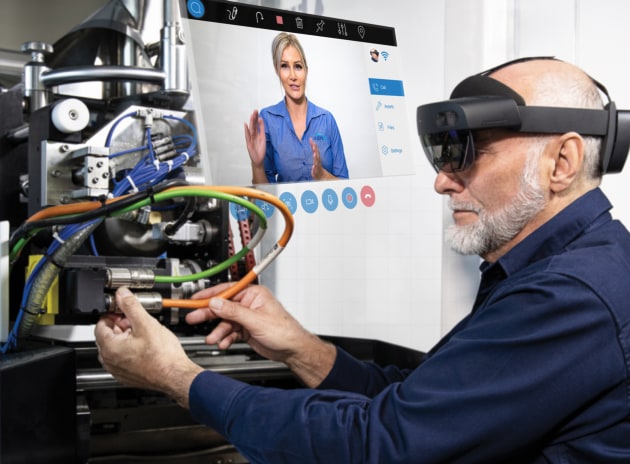
Two interesting services that tna offers its customers are virtual and augmented reality. Its virtual reality system allows engineers and clients around the world to visit a proposed line virtually. They can check dimensions and interferences and collaborate in real time. This allows the design to be fine-tuned before, rather than after, the first metal has been cut.
At PackExpo tna also promoted its augmented reality system, which uses the Microsoft HoloLens to connect the maintenance tech on the line with a support engineer at tna. This head mounted system allows each to share what they see.
The onsite tech can project images of the equipment to the remote engineer. In turn, the engineer can project images of wiring diagrams, machine pictures and more to the onsite tech. Two-way, hands-free voice communication completes the link. This system is almost as good as having the engineer onsite but without the delay and cost.
Robots everywhere
Robots, robots and more robots. Universal, Fanuc, Yaskawa, Staubli, ABB, Epson and many other robot manufacturers were well represented. The trend is robots and cobots that are faster, smarter, simpler and more capable.
Fanuc, for example, showed its new CRX-25iA collaborative robot. With a 25kg payload and 1,900mm reach it was palletising cases without the need for a vertical lift component.
Kuka Robotics showcased its new complete, end-to-end process automation multi-robot cell for the FMCG industry. The demonstration featured completely integrated automation – including robots, mobile platforms, advanced vision and software.
Designed to simulate a real production environment and automation solutions for each step – moving material from receiving and sorting to packing and distribution – the cell includes Kuka’s new KR 3 DELTA Hygienic robot, KR 6 SCARA and KR 6 AGILUS robots, a KMR iiwa autonomous mobile platform and advanced vision software, Kuka VisionTech.
Working with the three cell-based robots and completing a fully automated end-to-end solution for FMCG-related applications was Kuka's KMR iiwa that combines the sensitive KUKA LBR iiwa lightweight robot with a mobile, flexible platform. Designed to move omnidirectionally and execute 360-degree rotations, the KMR iiwa is autonomous, reacting immediately if a person or object is in the way, and achieves a positioning accuracy of up to +/- 5 mm. Equipped with a Kuka AIVI control system that uses artificial intelligence to direct automated guided transport vehicles, the KMR iiwa ensures optimum material flow to the production line.
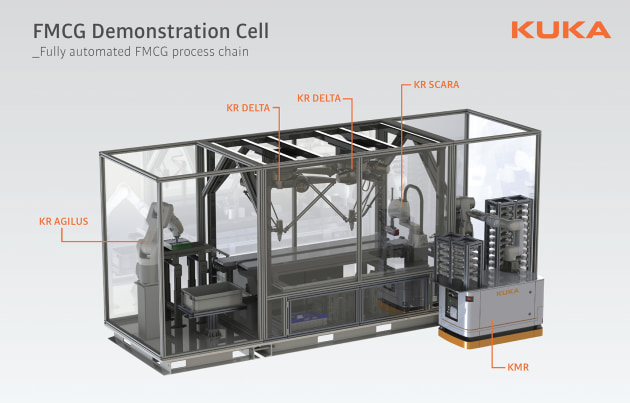
Sick QR codes are the go
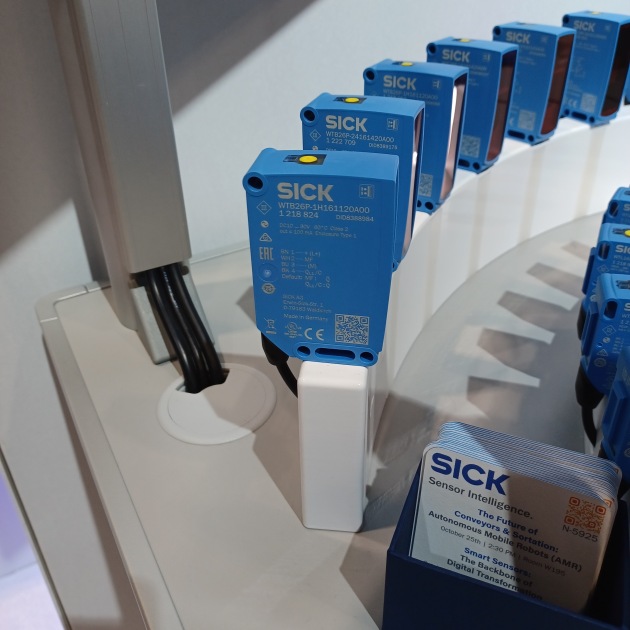
Finally, a shoutout to Sick Sensor Intelligence. Maintenance techs know how hard it can be to get information off machine components that may be inside of a machine. Sick has simplified this by adding QR code to their sensors.
Now, instead of trying to juggle a light, pen and pad to get the part number, all that is needed is a smartphone. Read the QR code and complete information pops up. Replacements can be ordered on the spot.
Any other OEMs reading this? You should be taking Sick's lead and making this industry standard.