At Pack Expo this week, Cama North America invited manufacturers looking to improve production and efficiency to see a demonstration of its innovative secondary packaging systems designed for ease of use and flexibility.
Cama’s flexible cartoning, case packing, tray packing, and robotic loading systems are designed to easily run multiple products and package sizes with quick and easy changeover.
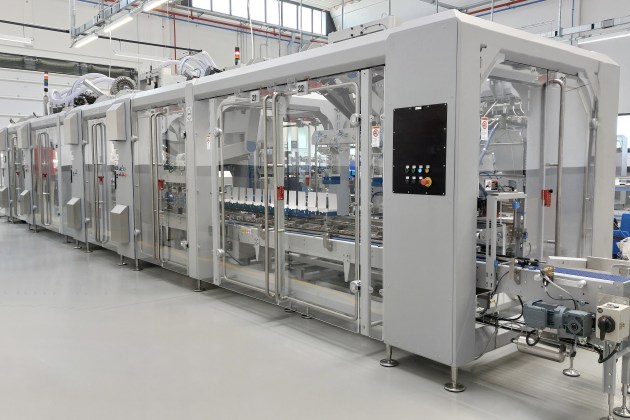
On display was its new MTL monoblock, an extension of the CAMA IF series with three modules: Forming, Loading and Closing cases, boxes.
For this application, Cama integrated the ACOPOStrak magnetic track system by B&R (pictured above). Thanks to this track system its monoblock can serve three or more upstream feeds for similar products with different synchronisations and manage buffers automatically. The result is increased productivity with a reduced footprint. The solution allows decoupling of the process stations, optimising the flow of products and cycle times; processing times were also optimised and the control panel was simplified, making commissioning and maintenance quicker and easier.
In addition to its special design, offering hygiene, ergonomics and flexibility, this solution has the following features:
- Over 1800 products/min
- Magnetic carriers
- Multi-configuration packs management
- Robotic forming, loading, and closing
- Insertion of leaflets
- Compact, ergonomic solution.
- Complemented by Cama 4.0 tools using augmented reality for training, configuration changes and maintenance.
Cama also showcased the next evolution of its class-leading augmented reality (AR) technology. With AR and virtualisation already proving invaluable across the design, build, commission, test and operational phases of its BreakThrough Generation (BTG) line of cartoners, case and tray packers, and sleeving systems, Cama now offers immersive, line side support for warranty, spares and consumables, through its Augmented Machine Assistance Package.