As PP faces an 'existential crisis', multinational brand owner Unilever has joined Nextek’s global project NEXTLOOPP, which aims to create food-grade recycled polypropylene (rPP) from post-consumer packaging waste.
Unilever has committed to halve the use of virgin plastic in its packaging and remove more than 100,000 tonnes of plastic entirely by 2025 through its ‘Less, better, no’ plastic framework to drive its transition towards a circular economy.
“Unilever is committed to bringing sustainability and circularity to its many products and help overcome the significant challenge of using high-quality rPP in food-contact applications,” says Edward Kosior, founder and CEO of Nextek.
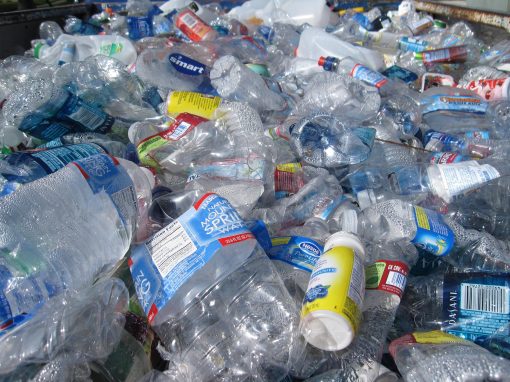
“As such, creating a long-term solution for PP packaging boosts Unilever’s contribution to a better outcome for everyone.”
Unilever and Nextek, together with other partners in the project are set to embark on the challenge to produce rPP through conventional mechanical recycling infrastructure that meets the regulatory standards for use in food packaging.
“Unilever supports the advancement of mechanical recycling infrastructure to produce food-grade rPP to complement other technology routes,” explains Sanjeev Das, global packaging director in Foods & Refreshment Division.
“Unlocking the mechanical recycling route to produce food-grade rPP will help boost our efforts to keep plastics in a loop and out of the environment.
“NEXTLOOPP looks forward to achieving the goal of creating a long-term solution for PP packaging so that consumers can be confident that when they participate in recycling, they are contributing to a better outcome for everyone.”
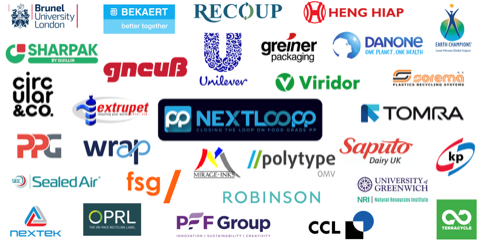
The other global organisations that have joined the multi-participant project (pictured right) include brand-owners, packaging converters, technology companies, universities and industry associations, through to end-users in the PP supply chain, who all bring their unique expertise to this cutting-edge project.
Their roles in the project are as follows:
- Unilever, Danone and Saputo Dairy UK will use the food-grade rPP in their products to create the circular pathway for PP.
- Tomra Sorting, Gneuss and Sorema will contribute their expertise in marker sorting, decontamination extrusion and intensive washing equipment for the demonstration plant, respectively.
- Sharpak, Greiner, Klockner Pentaplast, Robinson, PPG, PFF packaging, OMV, Extrupet, Bekaert, Polymer Extrusions, TerraCycle, Circular and Co, and FSG will be involved in the processing evaluation of the rPP grades by manufacturing packaging for filling and migration testing for their current customers, including UK’s largest food packaging manufacturers and retailers.
- CCL Labels and Mirage Inks will use their expertise for innovative label development, enabling separation of food and non-food packaging. CCL Labels and Mirage Inks, are both highly experienced participants of the recent Innovate UK PolyPRISM marker labels project.
- Wrap, Recoup and OPRL are key industry organisations that will develop critical design guidelines for food-grade PP packaging recycling, ensuring the long-term improvement of packaging to simplify and boost rPP recycling efficiency and quality.
- Brunel University London, Greenwich University, and the Natural Resources Institute will be involved in developing new markers and food packaging evaluation.
NEXTLOOPP will use Nextek’s Trade Marked technologies – PolyPRISMto sort packaging into food-grade categories and the PPristine process to decontaminate the packaging to the high level required for food applications.
PolyPRISM uses traditional labelling and branding methods to identify a host of different materials applying multiple markers for a wide range of codes.
“We have calculated that the 10,000tpa produced at the first plant will be quickly pre-ordered, as it will be the first material of its type in the EU and the UK, and the goal is to use rPP to manufacture a range of products such as film, sheet, thermoformed trays and injection moulded pots, tubs and trays to test all participants’ own products for processability and suitability for food applications,” says Kosior.
“This will help ensure participants are ready to implement recycled content into their packaging once the production facilities are up and running.
“This is by no means a speculative project as the technologies have been proven and early trials have been 100 per cent successful in production and have passed food-grade migration tests.
“As such, we see this as a transformational pathway to circular PP packaging, and a timely one at that, because PP is now facing an existential crisis.”